-
Xinqi Development Zone, Leliu, Foshan, Guangdong
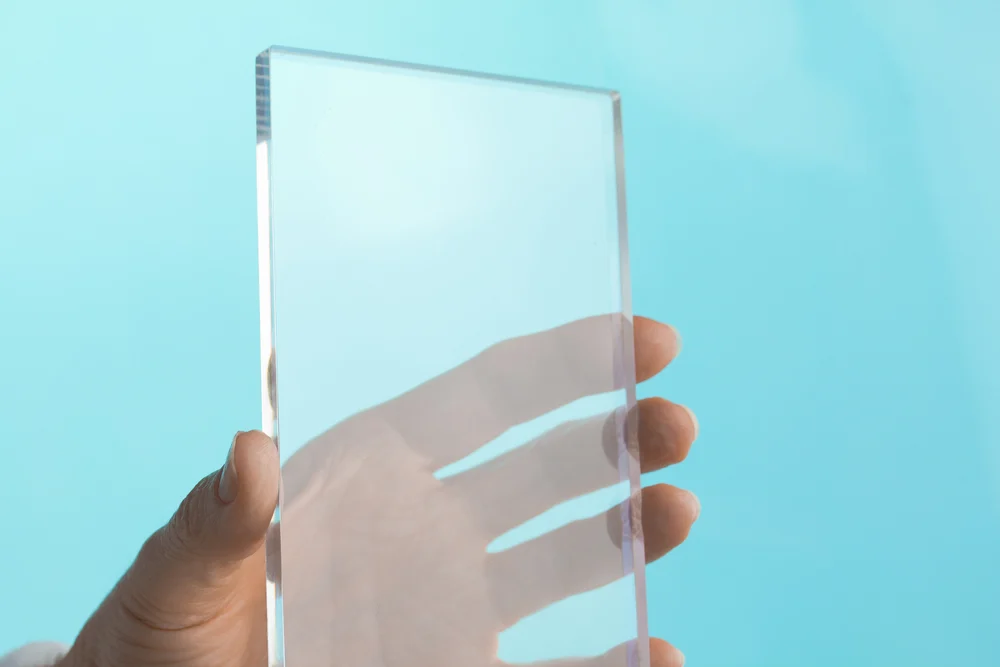
Why Are Acrylic Boards So Expensive?
Introduction
Acrylic board has become a favorite in the fields of building curtain walls, medical equipment and high-end home furnishings with its 92% light transmittance, excellent weather resistance and plasticity. However, its price is 3-5 times that of ordinary PVC board (data source: Plastics Today), which makes many consumers wonder: What exactly drives up the cost of acrylic board? This article will deeply analyze the three dimensions of raw materials, process and technology to reveal the value code of this “transparent gold”.
The butterfly effect of petroleum-based raw materials: MMA monomer cost fluctuations
Methyl methacrylate (MMA), the core raw material of acrylic board, accounts for more than 45% of the production cost (Grand View Research, 2023). This petroleum-derived monomer has been affected by multiple factors in recent years:
- Crude oil price transmission: The average international MMA price in 2022 increased by 23% year-on-year (ICIS data), which directly led to a surge in the cost of acrylic sheets
- Environmental protection policy increase: EU REACH regulations require MMA purity to reach 99.9%, and the energy consumption of the purification process increased by 17% (European Chemical Agency)
- Supply-side concentration: 80% of global production capacity is controlled by five companies including Dow and Mitsubishi (Statista, 2023), and bargaining power is highly concentrated
External link support: MMA Global Market Analysis Report EU Chemical Regulatory Policy
Precision manufacturing process: dual costs of time and technology
Acrylic sheets adopt casting molding process, which is significantly different from extrusion process:
Process link | Casting acrylic sheet | Ordinary extruded board |
---|---|---|
Curing time | 72-120 hours | 3-5 hours |
Thickness tolerance | ±0.1mm | ±0.5mm |
Surface hardness | 6H (pencil hardness) | 2H |
Equipment investment | $2 million/production line | $500,000/production line |
Take Sanyu Acrylic’s 5mm thick board as an example, it needs to go through 12 processes including monomer prepolymerization → mold casting → step-by-step heating (30℃→80℃) → precision annealing, and 4 technicians are required to monitor the whole process. This “slow work and fine work” model makes the unit energy consumption cost 40% higher than the extrusion process.
Performance premium: Each feature is a cost stack
The high price of acrylic sheet is essentially the realization of the value of its engineering performance:
- Optical performance: light transmittance is 15% higher than ordinary glass, haze <1% (ASTM D1003 standard)
- Weather resistance: no yellowing after 3000 hours of QUV accelerated aging test (UL certification data)
- Processing advantage: hot bending molding temperature is 60℃ lower than polycarbonate, saving 25% energy consumption
In the comparative experiment of Technical University of Munich, the crack resistance of acrylic sheet in the temperature difference cycle test from -40℃ to 90℃ is 300% higher than that of PETG sheet (experimental report number: TUM-PSE2022-017). Behind these performance indicators is the continuous investment in raw material ratio, additive research and development and process control.
Innovative paths to solve the cost dilemma
Faced with the challenge of high prices, the industry is seeking breakthroughs through technological innovation:
- Bio-based MMA research and development: Covestro and Cargill cooperate to develop bio-based MMA, which is expected to reduce carbon emissions by 35%
- Continuous casting process: The high-speed production line developed by Toray Machinery shortens the curing time by 30%
- Recycling system construction: The US Acrylic Recycling Coalition achieves a waste recycling rate of 85%
Conclusion
The high price of acrylic sheet is essentially a comprehensive value embodiment of petrochemicals, precision manufacturing and materials science. From the MMA monomer of $1,500 per ton, to the casting production line worth millions of dollars, to the rigorous performance testing system, every link interprets the market law of “high quality and high price”. For users who pursue long-term value, choosing suppliers that are ISO 9001 certified (such as Sanyu Acrylic) can achieve more than 20% comprehensive cost savings over the entire life cycle – after all, in the field of materials, the most expensive is often the cheapest compromise.