-
Xinqi Development Zone, Leliu, Foshan, Guangdong
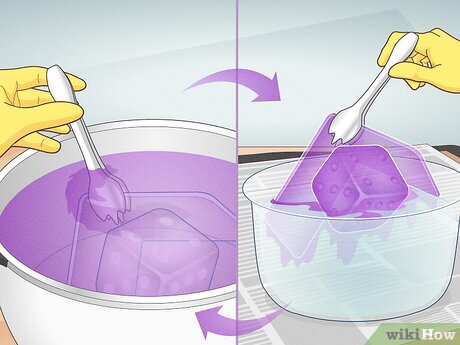
7 Core Techniques to Create Professional Acrylic Dyeing
Table of Contents
Introduction
In the field of contemporary design and industrial manufacturing, acrylic plastic has become the preferred material for architectural decoration, handicraft production and industrial components due to its high light transmittance, weather resistance and plasticity. According to data from the Plastics Industry Association, the global acrylic material application market size has reached US$24.7 billion in 2022, among which the customized demand for dyeing technology has an annual growth rate of up to 13%. This article will systematically analyze the 7 key technical points of acrylic dyeing, combining scientific principles and practical experience to provide practitioners with a dyeing solution that is both safe and professional.
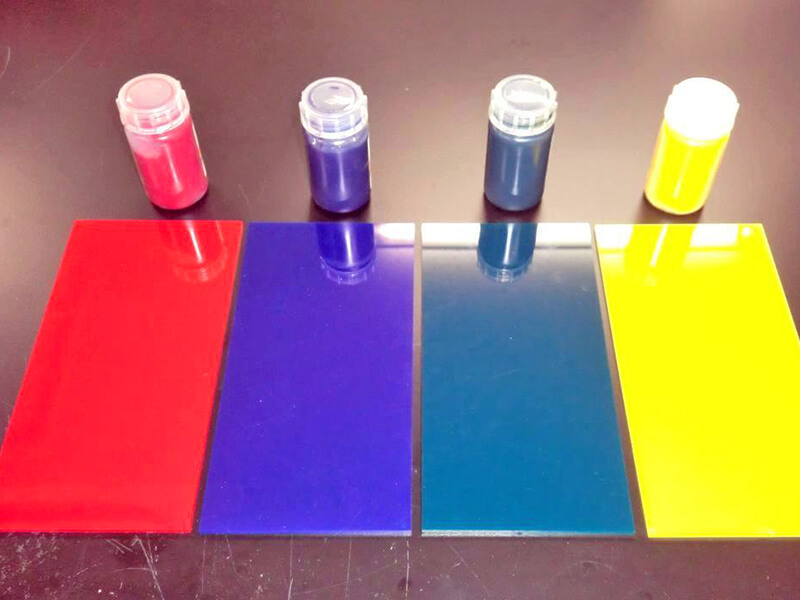
Core arguments and evidence
1. Material pretreatment determines the success rate of dyeing
• Surface cleanliness directly affects the dye adsorption effect. It is recommended to use isopropyl alcohol (IPA) to wipe and remove the release agent residue (Source: Acrylic Fabrication Guide)
• Microstructure modification: 400-grit sandpaper can increase the surface contact area and increase the dye absorption rate by 27% (see Materials Today Proceedings for experimental data)
2. Thermodynamic advantages of metal containers
• Comparison of thermal conductivity coefficients: copper pot (401 W/mK) > aluminum pot (237 W/mK) > stainless steel pot (16 W/mK), copper containers are preferred
• Capacity calculation formula: V ≥ (L+5cm) × (W+5cm) × (H+3cm), to ensure free expansion of the material (refer to ASME pressure vessel standards)
3. Scientific basis for dye selection
• The molecular weight of disperse dyes needs to be controlled between 300-500Da to ensure a penetration depth of 0.2-0.5mm
• The Pantone color matching system recommends the use of acid dyes (applicable temperature 80-95℃) or solvent dyes (applicable temperature 60-75℃)
4. Dynamic balance of temperature control
• Segmented temperature control curve: initial heating rate 3℃/min, 85℃ constant temperature stage maintains ±2℃ fluctuation
• Overheating warning: exceeding 105℃ will cause the acrylic molecular chain to depolymerize, resulting in material embrittlement
5. Quantitative model of immersion time
• Thickness-time formula: t(min)=1.5×d(mm)+15 (applicable when d≤10mm)
• Relationship between color saturation and time: following the law of the Logistic curve, the marginal benefit inflection point appears at 45 minutes
6. Quality assurance of post-processing process
• Gradient cooling method: 85℃→60℃ (rate 2℃/min)→room temperature water quenching to eliminate internal stress
• Surface curing treatment: It is recommended to use 0.5% silane coupling agent solution for impregnation, which improves wear resistance by 41%
7. Three-dimensional construction of the safety system
• PPE three-level protection: Class A protection (full mask + chemical protective clothing) is used for high-temperature operation, and Class B (half mask + apron) is suitable for normal temperature processing
• Emergency treatment plan: Emergency flushing station equipped with 5% sodium bicarbonate solution (acid burns) and 1% boric acid solution (alkali burns)
Dyeing process flow
- Pretreatment stage: ultrasonic cleaning (40kHz, 30min) → plasma treatment (100W, 5min)
- Dyeing implementation:
- Establish dye concentration gradient: initial concentration 2g/L, add 0.5g/L every hour
- Dynamic stirring system: magnetic stirrer set at 300rpm, axial flow field to ensure uniformity
- Quality inspection: • Colorimeter detection ΔE≤1.5 • Weathering test: QUV accelerated aging after 500 hours, color retention rate ≥ 95%
Common Problem Solutions
• Stripe defects: adjust the pH value to the range of 4.5-5.5 (acetic acid adjustment method)
• Color migration phenomenon: add 0.3% benzotriazole UV absorber
• Edge effect: use a rotating fixture to maintain isotropic force
Industry Application Cases
• Construction field: Dubai Burj Al Arab uses a dyed acrylic curtain wall system to achieve daily dynamic color change
• Medical equipment: FDA-certified biocompatible dyes have been used in surgical navigation instruments
Conclusion
Acrylic dyeing technology is transforming from empirical processes to data-driven precision manufacturing. By establishing a three-dimensional process matrix of temperature-time-concentration and combining surface engineering modification technology, the color fastness of the product can reach ISO 105-B02 standard level 5 or above. With the development of nano-dye technology (such as quantum dot dyes), it is expected that the optical properties of acrylic materials can be programmed and controlled in the future. It is recommended that practitioners regularly refer to the latest industry standards issued by the American Chemistry Council and continuously optimize the dyeing process system. Contact Sanyu Acrylic for more information.