-
Зона развития Синьци, Лелю, Фошань, Гуандун
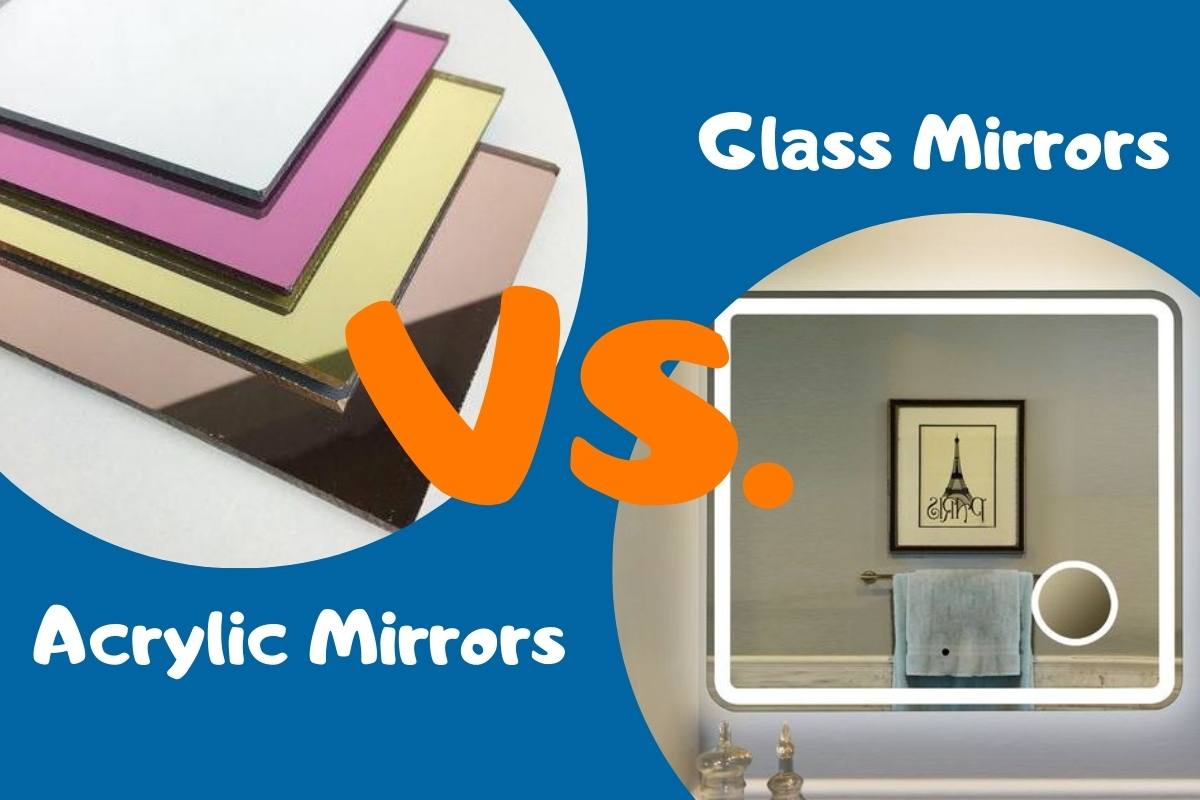
Mirror Selection: Acrylic or Glass? Pros, Cons & Uses
The choice of a mirror may determine the operating cost of a gym, the safety factor of a children’s room, and even the range of a new energy vehicle.
When decorating a house, designing a commercial space, or developing an industrial product, the choice of mirror material is often simply attributed to the “appearance” issue. However, with the rapid progress of material science today, the difference between acrylic mirrors and glass mirrors has far exceeded the surface.
With its anti-shatter properties and lightweight design, acrylic mirrors have quietly occupied more than 75% of the global gym, amusement park and car rearview mirror market.
And glass mirrors, with their irreplaceable optical precision, still firmly control the application of high-end retail, medical imaging and precision instruments.
With the innovation of material technology, the performance boundary between the two mirrors is becoming blurred – new coatings and composite materials are constantly emerging, challenging traditional cognition.
Material properties and basic differences
Acrylic mirrors (also known as organic glass mirrors) are made of polymethyl methacrylate (PMMA), while traditional glass mirrors are made of float glass with silver or aluminum plating. This difference in core materials determines the fundamental difference in physical properties between the two.
- Acrylic mirrors have a density of only 1.18g/cm³, **less than half of glass mirrors (2.5g/cm³), which gives them a significant advantage in large ceiling installations or movable furniture applications.
- The molecular structure of glass mirrors gives them higher rigidity and stability, but also brings the risk of brittle fracture.
- Acrylic exhibits the toughness unique to polymer materials: plastic deformation occurs instead of direct shattering when impacted.
In terms of manufacturing technology, the silver plating process of glass mirrors has a greater environmental pollution, while the vacuum aluminum plating technology used in modern acrylic mirrors is more environmentally friendly. Processing flexibility is the trump card of acrylic – through hot bending, engraving and other processes, it can be made into curved and special-shaped mirrors that are difficult to achieve with traditional glass, meeting the special needs of sports car rearview mirrors or art installations.
Safety and durability
When mirrors are used in children’s activity areas, schools or stadiums, safety performance becomes the primary consideration.
- Ordinary glass mirrors produce sharp fragments when broken, and the instantaneous splash may cause serious injuries.
- The impact resistance of acrylic mirrors makes it only crack or dent under the same impact force, and will not suddenly disintegrate.
In the field test of car rearview mirrors, the breakage rate of acrylic mirrors under harsh road conditions is 30% lower than that of glass mirrors. Driving safety is not only about material strength, but also about the “failure mode” when impacted – the plastic failure characteristics of acrylic avoid the sudden shattering of glass.
However, the surface hardness defect of acrylic mirrors cannot be ignored: the Mohs hardness is only 2-3, far lower than the 5.5 level of glass. This means that scratches from branches or improper cleaning may leave permanent scratches. According to statistics, the probability of surface damage on acrylic mirrors is 50% higher than that on glass mirrors under the same use environment.
Optical performance and visual effects
Why do high-end retail stores insist on using glass for fitting mirrors? The answer lies in the stringent requirements of optical precision.
Glass mirrors have a light transmittance of 90%-95% and extremely high surface flatness, providing real reflections with almost no distortion. This feature is crucial for clothing color reproduction, medical imaging instruments and optical experimental equipment.
Although the light transmittance of acrylic mirrors is also 92%, the molecular orientation may cause slight deformation during processing. Especially in high temperature environments (>70℃), its thermal deformation characteristics may cause mirror curvature changes, resulting in image distortion.
The latest technology, such as the SHD super-strong thin film technology developed by Foshan Huaguo Optics, significantly improves the transmittance of the infrared band (8-12μm) to more than 92% by coating a multi-layer functional film (ZnS/Ge/YbF3) on the acrylic surface. This breakthrough technology is gradually bridging the performance gap between the two types of mirrors in the military and medical fields.
Environmental adaptability and maintenance costs
The environment in which the mirror is located determines its lifespan – this is particularly evident in outdoor applications.
- Glass mirrors show excellent stability under ultraviolet radiation and can still maintain their initial reflectivity after ten years of use.
- After a year of exposure to the sun in tropical areas, about 20%-30% of ordinary acrylic mirrors will turn yellow or become brittle.
Temperature adaptability is also critical: glass can withstand temperatures above 150℃, while acrylic begins to soften at around 80℃. This makes glass mirrors more suitable for scenes such as high-temperature areas in kitchens or observation windows of industrial boilers.
The difference in maintenance costs has a more direct impact on the long-term use experience:
- Glass mirrors can be cleaned with ordinary detergents
- Acrylic mirrors require special detergents (containing ammonia or chlorine will corrode the surface)
- When cleaning, you must use a microfiber cloth, otherwise the accumulation of scratches will significantly reduce the clarity of the reflection
Application scenarios and space adaptability
Choosing a mirror is like choosing a tool – specific scenarios require specific solutions.
- Acrylic mirrors have become the mainstream choice for car rearview mirrors due to their light weight (50% weight reduction) and impact resistance. For every 1kg weight reduction of new energy vehicles, the range can be increased by 2-3 kilometers, making acrylic rearview mirrors a strategic component of lightweight design for car companies.
- In safety-sensitive areas such as children’s rooms, swimming pools or gyms, its anti-shattering properties provide safety protection.
- In commercial displays, the hot bending properties of acrylic allow the production of curved mirror display cabinets, creating an immersive shopping experience through light refraction.
Glass mirrors are still irreplaceable in situations where high-precision reflection is required:
- Oral mirrors in dental clinics
- Fitting mirrors in high-end clothing stores
- Optical laboratory equipment
- Infrared chalcogenide glass lenses (Foshan Huaguo Optics patented technology) achieve a transmittance of more than 92% in the 8-12μm band, becoming a core component of thermal imagers and military night vision equipment.
Future trends and technological innovations
Breakthroughs in materials science are driving the ablation of the performance boundaries of the two types of mirrors.
- Acrylic mirror field: Nano-hardening coating technology makes its surface hardness close to the level of glass
- The addition of UV stabilizers increases weather resistance by 300%
- Glass mirror industry: Composite lamination process sandwiches polymer materials between two layers of glass, combining the optical properties of glass and the impact resistance of plastic
As an emerging cross-border product, smart mirrors are integrating the advantages of two types of materials:
- Acrylic substrate reduces weight
- Glass protective layer ensures the flatness of the touch screen
- LED and sensor embedded in the middle realize functions such as human body sensing, temperature and humidity display
Environmental regulations also drive change: The EU RoHS directive restricts the use of cadmium in the glass silver plating process, prompting more manufacturers to turn to aluminum-coated acrylic mirrors – whose reflectivity is close to 92%, but carbon emissions are reduced by 40%.
Decision guide: When to choose which mirror material
Selecting a mirror requires a three-dimensional evaluation system: safety weight, environmental challenges and optical requirements.
- Scenarios where acrylic mirrors are preferred:
- Kindergarten protection height design (walls below 1.2m)
- Car mirrors (weight reduction requirements > 1kg/car)
- Movable exhibits (transportation frequency > 2 times/month)
- Buildings in earthquake-prone areas
- Fields where glass mirrors are used:
- Laser calibration instruments (flatness tolerance < 0.001mm)
- Historical building restoration (need to match the original glass spectroscopic characteristics)
- High temperature working area (continuous temperature > 80℃)
- Luxury goods display (requires zero image distortion)
Cost-sensitive projects can adopt a hybrid strategy: use acrylic mirrors for the main body to reduce the budget, and embed small-sized glass mirrors at key observation points to ensure accuracy. The walls of educational institutions can adopt a partition design of acrylic below 1.5m + high-rise glass mirrors, taking into account both safety and cost.
With the chalcogenide glass lens transmittance exceeding 92% и acrylic surface nano-hardening technology being commercialized, the mirror material market will move towards integration rather than substitution in the future.
High-end medical imaging equipment may use glass-acrylic composite layers – glass ensures optical accuracy, and acrylic substrate reduces the weight of the equipment. The smart rearview mirror of new energy vehicles will integrate transparent circuits on curved acrylic substrate to achieve a double breakthrough in weight and function.
The essence of mirror selection is not a material competition, but an art of matching needs. The next time you stand in front of a mirror, you might as well touch its edge: behind the cold or warm touch is the real magic carefully woven by humans with material science.