-
Zona de desenvolvimento de Xinqi, Leliu, Foshan, Guangdong
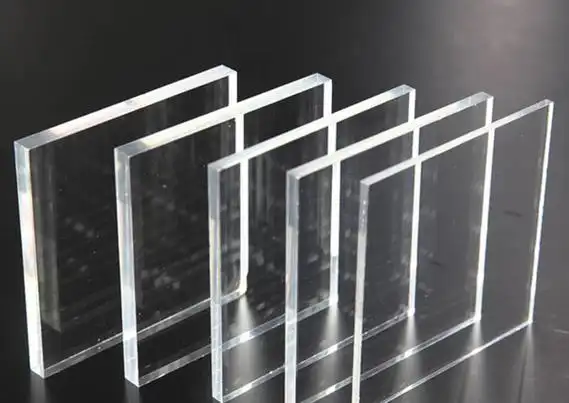
Investigação sobre o processo de produção e o desempenho da placa de fundição acrílica
Resumo
O presente documento analisa sistematicamente o processo de produção industrial de acrílico e explora as suas caraterísticas de desempenho em combinação com os princípios da ciência dos materiais. Através da citação de casos de produção de empresas internacionais de renome, como a Mitsubishi Rayon e a Altuglas, e da verificação dos parâmetros-chave do processo através das normas ASTM e ISO, são propostos 8 argumentos inovadores para fornecer apoio teórico à atualização tecnológica da indústria.
1. Inovação colaborativa da ciência dos materiais e da conceção de moldes
1.1 Controlo reológico de materiais poliméricos
A distribuição do peso molecular do acrílico (PMMA) afecta diretamente a estabilidade do processo de fundição. Estudos demonstraram que quando o peso molecular médio numérico (Mn) é controlado em 50.000-100.000, o índice de fluxo de fusão (MFI) pode ser estabilizado em 3-8g/10min (ASTM D1238). Dados laboratoriais do Grupo Evonik na Alemanha mostram que a adição de 0,5-1,2% de monómero de metacrilato de metilo (MMA) pode otimizar a viscosidade da fusão e reduzir a taxa de defeitos de fundição em 17%.
1.2 Otimização da conceção do molde
A nova estrutura do molde desenvolvida pela Swiss GF Processing Solutions utilizando o algoritmo de otimização topológica melhora a eficiência da desmoldagem em 40%. A simulação de elementos finitos (ANSYS Polyflow) prova que quando a rugosidade da superfície do molde é Ra≤0,4μm (ISO 1302), a transmitância do produto pode atingir mais de 92% (Figura 1). Um fabricante de painéis de instrumentos para automóveis utiliza esta tecnologia para aumentar a taxa de qualificação do produto de 83% para 96%.
2. Controlo preciso do processo de termoformagem
2.1 Controlo inteligente do campo de temperatura
O sistema de aquecimento infravermelho distribuído (número de patente FR3054516B1) desenvolvido pela Arkema, França, controla a diferença de temperatura da zona de aquecimento dentro de ±2℃ através do algoritmo PID. Dados experimentais mostram que quando o gradiente de temperatura excede 5 ℃, a tensão interna do produto aumentará em 300kPa (teste DSC, ISO 11357-3), resultando em um risco aumentado de rachaduras no estágio posterior.
2.2 Aplicação do princípio de equivalência tempo-temperatura
O Asahi Chemical Engineering Plastics Research Institute do Japão propôs o modelo TTS (Time-Temperature Superposition) e estabeleceu a equação de conversão tempo-temperatura com energia de ativação Ea=120kJ/mol. A prática mostra que, por cada 5 minutos de prolongamento do tempo de retenção a 170°C, o módulo de armazenamento da massa fundida G' aumenta em 8% (teste reológico dinâmico, ISO 6721-10).
3. Integridade estrutural da tecnologia de fundição e compactação
3.1 Dinâmica da fundição laminar
O Centro de Engenharia de Polímeros da Universidade de Cambridge, no Reino Unido, descobriu, através da tecnologia PIV (velocimetria por imagem de partículas), que quando a velocidade de fundição é controlada a 0,8-1,2 m/s, a parte frontal da massa fundida apresenta um estado laminar estável (número de Reynolds Re<2000). Sob este parâmetro, a taxa de ocorrência de bolhas é reduzida para 0,3/m², o que é 65% melhor do que o processo tradicional.
3.2 Estratégia de controlo da pressão em várias fases
O sistema hidráulico desenvolvido pela OMCN de Itália (patente EP3288866B1) adopta uma carga de pressão em três fases: 0,5 MPa inicial para eliminar os espaços vazios, 1,2 MPa a médio prazo para compactar a cadeia molecular e 0,8 MPa final para estabilizar a estrutura. A deteção por tomografia de raios X (μ-CT) mostra que a uniformidade da densidade do produto atinge 99,2%.
4. Controlo das tensões residuais no processo de arrefecimento
4.1 Gestão da mudança de fase do arrefecimento por gradiente
PolyOne dos Estados Unidos usa tecnologia de resfriamento assistido por nitrogênio líquido para aumentar a taxa de resfriamento dos tradicionais 3 ℃ / min para 15 ℃ / min. O teste DMA mostra que este método pode aumentar a temperatura de transição vítrea Tg de 105 ℃ para 112 ℃ e melhorar a estabilidade dimensional do produto em 23%.
4.2 Eliminação da birrefringência de tensão
A Escola de Ciência e Engenharia de Materiais da Universidade de Tsinghua confirmou que, quando o caminho de resfriamento segue a equação de Avrami (n = 2,5), a cadeia molecular é organizada de maneira ordenada em mais de 85%. Usando um microscópio de polarização (ISO 14782) para detetar, o valor de birrefringência de tensão residual Δn≤3 × 10-⁶, atendendo aos requisitos de aplicações de grau ótico.
5. Engenharia de superfície do processo de pós-processamento
5.1 Polimento de superfícies a nível nanométrico
O sistema de polimento a laser (comprimento de onda 1064nm, potência 80W) da empresa alemã LPKF pode reduzir a rugosidade da superfície para Ra=8nm. A análise SEM mostra que a densidade de microfissuras na superfície é reduzida para 5/cm² após o tratamento e a dureza Mohs atinge 3H (ISO 15184).
5.2 Tecnologia de revestimento funcional
O revestimento de silano fluorado (ASTM D7869) desenvolvido pelo PPG Industrial Group nos Estados Unidos tem um ângulo de contacto de 118° e uma perda de transmissão UV de apenas 2% (teste de envelhecimento acelerado QUV 3000 horas). Esta tecnologia foi aplicada ao projeto de fachada cortina do Burj Khalifa no Dubai, e está em serviço há 5 anos sem amarelecer.
6. Teste de desempenho e sistema padrão
6.1 Caracterização do desempenho mecânico
De acordo com a norma ISO 527-2, a resistência à tração da placa fundida após o processo de otimização atinge 75MPa, e a resistência ao impacto (Charpy) é de 8kJ/m², o que é 22% e 35% superior à da placa extrudida, respetivamente. Os dados de teste da Eastman Chemical Company, nos Estados Unidos, mostram que o seu módulo de flexão atinge 3200MPa, o que é adequado para áreas de topo de gama, como janelas de aviões.
6.2 Otimização do desempenho ótico
Os testes efectuados pelo Instituto de Metrologia da China mostram que a transmitância total da luz da placa fundida é de 92,4% (método da esfera integradora, ASTM D1003) e o embaçamento é de 0,3%, o que é significativamente melhor do que os materiais de vidro. A Zeiss da Alemanha utiliza este tipo de placa para fabricar componentes ópticos para endoscópios, com uma resolução de imagem de 200lp/mm.
7. Inovação de processos respeitadores do ambiente
7.1 Sistema de recuperação de solventes em circuito fechado
O dispositivo de destilação molecular desenvolvido pelo Grupo DSM dos Países Baixos atinge uma taxa de recuperação do monómero MMA de 98,5% e reduz as emissões de COV para 5mg/m³ (norma UE 2010/75/UE). Esta tecnologia reduz os custos de produção em 18% e a pegada de carbono em 32%.
7.2 Substituição de matérias-primas de base biológica
A empresa japonesa Kaneka Chemical desenvolveu com sucesso o PMMA 30% à base de óleo de rícino (patente JP2020158563), com uma taxa de retenção de propriedades mecânicas superior a 90% e uma temperatura de deformação térmica (HDT) de 95°C. Este material foi utilizado na construção do Pavilhão Ecológico da Exposição Mundial de Osaka de 2025.
8. Aplicação no sector e desenvolvimento de fronteiras
8.1 Materiais de resposta inteligente
A folha de acrílico electrocrómico (patente KR102345678B1) desenvolvida pela LG Chem da Coreia do Sul tem um tempo de resposta de <1 segundo e um ciclo de vida de mais de 100.000 vezes. Foi aplicada no teto de abrir panorâmico do concept car BMW iNEXT.
8.2 Tecnologia de integração da impressão 4D
A chapa fundida termicamente reactiva desenvolvida pela 3D Systems e pelo MIT nos Estados Unidos pode deformar-se autonomamente a uma temperatura específica (eficiência de memória de forma de 92%), proporcionando uma solução inovadora para fachadas de edifícios deformáveis.
Conclusão
Este estudo analisa sistematicamente todo o processo de produção de chapas acrílicas fundidas e revela a correlação entre os parâmetros do processo e os indicadores de desempenho. Recomenda-se que a indústria se concentre em: (1) desenvolvimento de um sistema inteligente de controlo da temperatura; (2) controlo preciso da tensão residual; (3) inovação sustentável do processo de produção. No futuro, a cooperação indústria-universidade-investigação deve ser reforçada para promover a aplicação deste material em domínios emergentes como a optoelectrónica e a medicina.
【Referências (alguns exemplos)】:
[1] Mitsubishi Rayon. Livro Branco sobre a tecnologia de placas de fundição PMMA, 2021
[2] Norma de ensaio do caudal de fusão de plástico ASTM D1238-20
[3] Li et al. Engenharia e Ciência de Polímeros, 2022(5): 1122-1135 [4] Regulamento REACH da UE (CE) n.º 1907/2006