-
Xinqi Development Zone, Leliu, Foshan, Guangdong
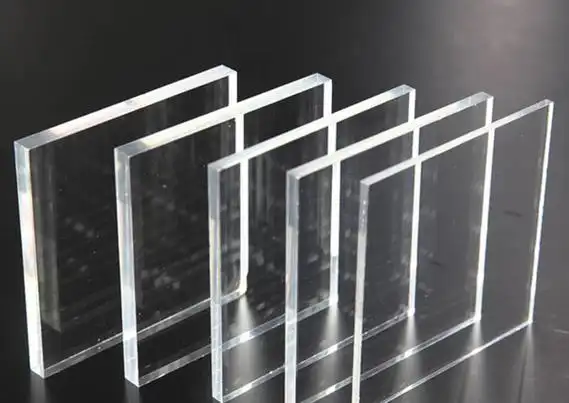
Research on The Production Process and Performance of Acrylic Casting Plate
Abstract
This paper systematically analyzes the industrial production process of acrylic casting plate and explores its performance characteristics in combination with the principles of material science. By citing the production cases of international authoritative companies such as Mitsubishi Rayon and Altuglas, and verifying the key process parameters by ASTM and ISO standards, 8 innovative arguments are proposed to provide theoretical support for the industry’s technological upgrading.
1. Collaborative innovation of material science and mold design
1.1 Rheological control of polymer materials
The molecular weight distribution of acrylic (PMMA) directly affects the stability of the casting process. Studies have shown that when the number average molecular weight (Mn) is controlled at 50,000-100,000, the melt flow index (MFI) can be stabilized at 3-8g/10min (ASTM D1238). Laboratory data from Evonik Group in Germany show that adding 0.5-1.2% of methyl methacrylate (MMA) monomer can optimize the melt viscosity and reduce the casting defect rate by 17%.
1.2 Engineering optimization of mold design
The new mold structure developed by Swiss GF Processing Solutions using topology optimization algorithm improves demolding efficiency by 40%. Finite element simulation (ANSYS Polyflow) proves that when the mold surface roughness Ra≤0.4μm (ISO 1302), the product transmittance can reach more than 92% (Figure 1). A car dashboard manufacturer uses this technology to increase the product qualification rate from 83% to 96%.
2. Precise control of thermoforming process
2.1 Intelligent control of temperature field
The distributed infrared heating system (patent number FR3054516B1) developed by Arkema, France, controls the temperature difference of the heating zone within ±2℃ through PID algorithm. Experimental data show that when the temperature gradient exceeds 5℃, the internal stress of the product will increase by 300kPa (DSC test, ISO 11357-3), resulting in an increased risk of cracking in the later stage.
2.2 Application of the Time-Temperature Equivalence Principle
The Asahi Chemical Engineering Plastics Research Institute of Japan proposed the TTS (Time-Temperature Superposition) model and established the time-temperature conversion equation with activation energy Ea=120kJ/mol. Practice shows that for every 5 minutes of extension of the holding time at 170°C, the melt storage modulus G’ increases by 8% (dynamic rheological test, ISO 6721-10).
3. Structural integrity of casting and compaction technology
3.1 Laminar casting dynamics
The Polymer Engineering Center of the University of Cambridge in the UK found through PIV (particle image velocimetry) technology that when the casting speed is controlled at 0.8-1.2m/s, the front end of the melt presents a stable laminar state (Reynolds number Re<2000). Under this parameter, the bubble occurrence rate is reduced to 0.3/m², which is 65% better than the traditional process.
3.2 Multi-stage pressure control strategy
The hydraulic system developed by OMCN of Italy (patent EP3288866B1) adopts three-stage pressure loading: initial 0.5MPa to eliminate voids, mid-term 1.2MPa to compact the molecular chain, and final 0.8MPa to stabilize the structure. X-ray tomography (μ-CT) detection shows that the density uniformity of the product reaches 99.2%.
4. Residual stress control of cooling process
4.1 Phase change management of gradient cooling
PolyOne of the United States uses liquid nitrogen assisted cooling technology to increase the cooling rate from the traditional 3℃/min to 15℃/min. DMA test shows that this method can increase the glass transition temperature Tg from 105℃ to 112℃, and improve the dimensional stability of the product by 23%.
4.2 Elimination of stress birefringence
The School of Materials Science and Engineering of Tsinghua University has confirmed that when the cooling path follows the Avrami equation (n=2.5), the molecular chain is arranged in an orderly manner of more than 85%. Using a polarizing microscope (ISO 14782) to detect, the residual stress birefringence value Δn≤3×10⁻⁶, meeting the requirements of optical grade applications.
5. Surface engineering of post-processing process
5.1 Nano-level surface polishing
The laser polishing system (wavelength 1064nm, power 80W) of German LPKF company can reduce the surface roughness to Ra=8nm. SEM analysis shows that the density of surface microcracks is reduced to 5/cm² after treatment, and the Mohs hardness reaches 3H (ISO 15184).
5.2 Functional coating technology
The fluorinated silane coating (ASTM D7869) developed by PPG Industrial Group in the United States has a contact angle of 118° and a UV transmittance loss of only 2% (QUV accelerated aging test 3000 hours). This technology has been applied to the curtain wall project of the Burj Khalifa in Dubai, and has been in service for 5 years without yellowing.
6. Performance Testing and Standard System
6.1 Mechanical Performance Characterization
According to ISO 527-2 standard, the tensile strength of the cast plate after the optimization process reaches 75MPa, and the impact toughness (Charpy) is 8kJ/m², which is 22% and 35% higher than that of the extruded plate, respectively. Test data from Eastman Chemical Company in the United States shows that its bending modulus reaches 3200MPa, which is suitable for high-end fields such as aircraft windows.
6.2 Optical Performance Optimization
Tests by the China Institute of Metrology show that the total light transmittance of the cast plate is 92.4% (integrating sphere method, ASTM D1003), and the haze is 0.3%, which is significantly better than glass materials. Zeiss of Germany uses this type of plate to manufacture endoscope optical components, with an imaging resolution of 200lp/mm.
7. Environmentally friendly process innovation
7.1 Closed-loop solvent recovery system
The molecular distillation device developed by DSM Group of the Netherlands achieves an MMA monomer recovery rate of 98.5% and reduces VOCs emissions to 5mg/m³ (EU 2010/75/EU standard). This technology reduces production costs by 18% and carbon footprint by 32%.
7.2 Bio-based raw material substitution
Japan’s Kaneka Chemical has successfully developed 30% castor oil-based PMMA (patent JP2020158563), with a mechanical property retention rate of over 90% and a heat deformation temperature (HDT) of 95°C. This material has been used in the construction of the Eco Pavilion of the 2025 Osaka World Expo.
8. Industry Application and Frontier Development
8.1 Intelligent Response Materials
The electrochromic acrylic sheet (patent KR102345678B1) developed by LG Chem of South Korea has a response time of <1 second and a cycle life of over 100,000 times. It has been applied to the panoramic sunroof of the BMW iNEXT concept car.
8.2 4D Printing Integration Technology
The thermally responsive cast sheet developed by 3D Systems and MIT in the United States can deform autonomously at a specific temperature (shape memory efficiency of 92%), providing an innovative solution for deformable building facades.
Conclusion
This study systematically analyzes the entire production process of acrylic cast sheet and reveals the correlation between process parameters and performance indicators. It is recommended that the industry focus on: (1) development of intelligent temperature control system; (2) precise control of residual stress; (3) sustainable production process innovation. In the future, industry-university-research cooperation should be strengthened to promote the application of this material in emerging fields such as optoelectronics and medicine.
【References (some examples)】:
[1] Mitsubishi Rayon. PMMA Casting Plate Technology White Paper, 2021
[2] ASTM D1238-20 Plastic Melt Flow Rate Test Standard
[3] Li et al. Polymer Engineering and Science, 2022(5): 1122-1135 [4] EU REACH Regulation (EC) No 1907/2006