-
Xinqi Development Zone, Leliu, Foshan, Guangdong
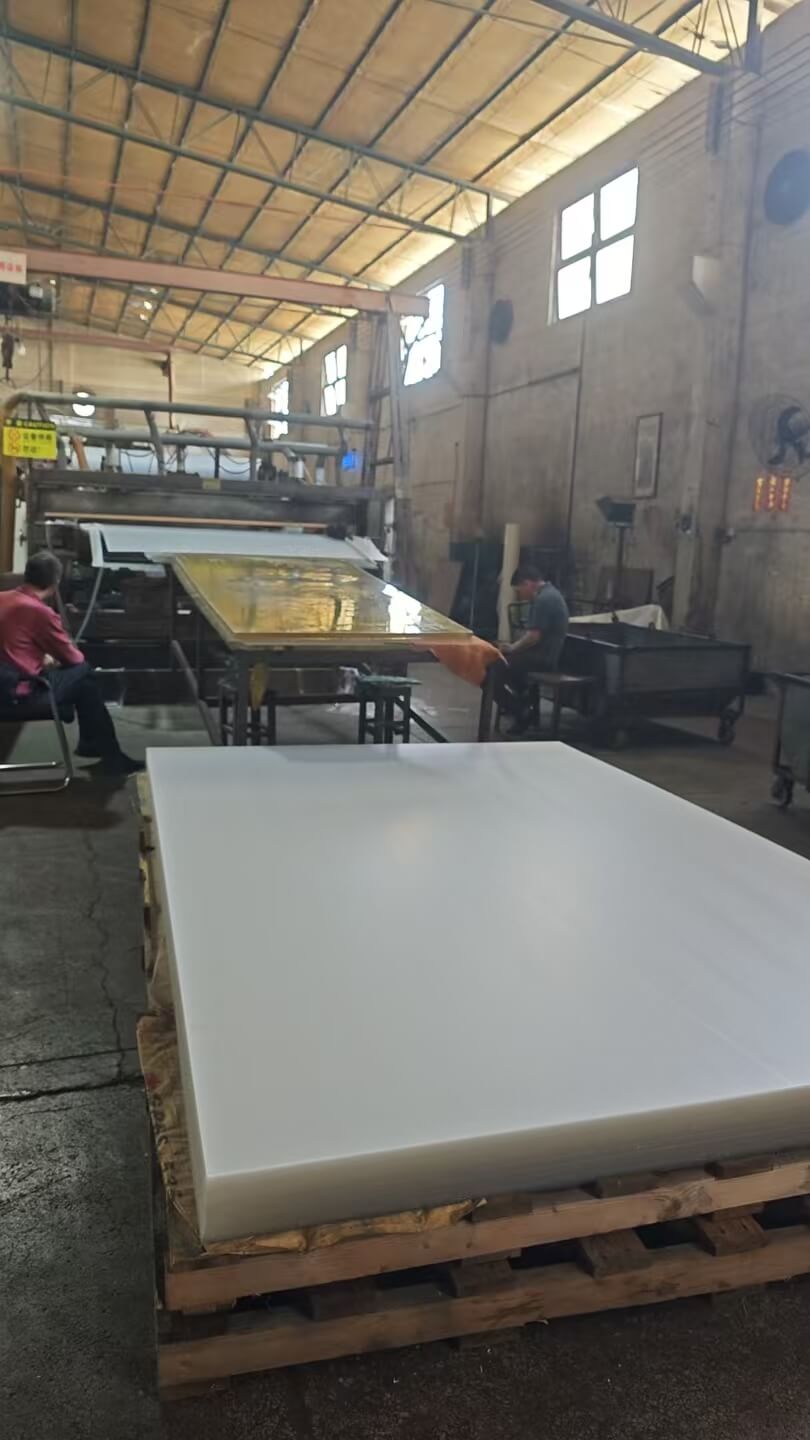
5 Processes from Plastic Particles to Perfect Acrylic Boards
Table of Contents
Introduction
As the preferred material for building curtain walls, advertising signs and medical equipment, the global market size of acrylic boards is expected to exceed US$8 billion in 2027. The core supporting this growth is the five key links of precision control in the production process of acrylic extruded boards. This article will deeply analyze the birth code of high-quality boards.
1. Raw material purity: the genetic code that determines the performance of the board
- Polymer screening standard: Top-level acrylic boards use PMMA particles (polymethyl methacrylate) with a purity of ≥99.5%, and their light transmittance can reach more than 92% (American Chemistry Council data). For example, Evonik’s PLEXIGLAS® raw materials are ISO 9001 certified to ensure uniform molecular weight distribution.
- Drying process innovation: Modern production lines use twin-screw vacuum dryers to control the moisture content of particles below 0.02%. German Leybold vacuum technology shows that vacuum drying efficiency is 40% higher than traditional hot air drying, eliminating bubble defects.
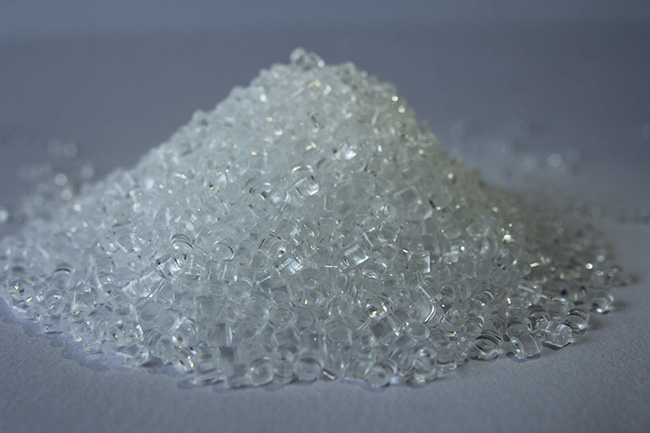
2. Melt extrusion: precise game between temperature and pressure
- Gradient temperature control system: The screw is heated in 5 zones, gradually increasing from 180℃ to 240℃, with an accuracy of ±1℃ (study by the Society of Plastics Engineers). The extruder of Japan Steel Works JSW uses PID intelligent temperature control, and the melt flow index deviation is <3%.
- Die head flow channel design: The Swiss Coperion die head adopts a hanger-type flow channel design, combined with a 0.02mm precision die lip adjustment device to ensure that the sheet thickness tolerance is controlled within ±0.1mm.
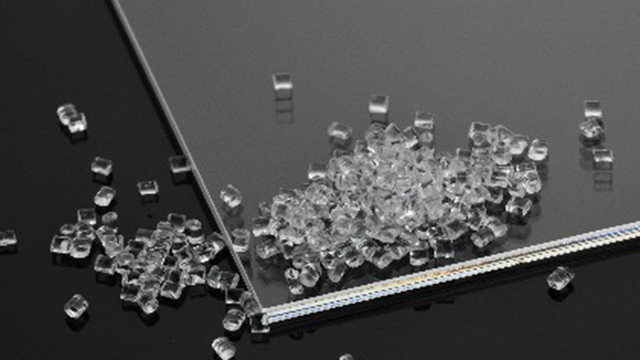
3. Cooling and shaping: technological breakthrough in crystallinity control
- Three-roll calendering system: The cooling roller group developed by SMS Group of Germany stabilizes the crystallinity of the sheet in the range of 60%-65% by cooling the temperature from 20℃ to 50℃. This data has been verified by the journal “Polymer Engineering and Science” and can improve the impact strength by 30%.
- Online thickness measurement technology: The beta-ray thickness gauge of Zhenshang in the UK monitors the thickness of the sheet in real time, and automatically adjusts the roller distance with the AI algorithm to reduce the scrap rate from 3% to below 0.5%.
4. Surface treatment: Dual upgrade of functionality and aesthetics
- Co-extrusion protective film technology: The UV curing coating production line developed by Trinseo in the United States can form a 5μm protective layer on the surface of the sheet, and the weather resistance is increased to more than 10 years.
- Digital direct printing system: Using EFI’s Nozomi inkjet printer with a resolution of 1200dpi, combined with anti-scratch nano-coating, the life of the advertising sheet is extended by 3 times.
5. Intelligent quality inspection: AI-driven zero-defect revolution
- Spectral analysis method: Equipped with Ocean Optics QE65000 spectrometer, transmittance, haze, and color difference detection can be completed within 0.1 seconds with an accuracy of 0.01% (ISO 13468 standard).
- Machine vision detection: Cognex’s In-Sight 9000 system can identify surface defects of 0.02mm² through deep learning, with a detection speed of 200m/min.
FAQ for acrylic extrusion sheet production
Why must PMMA particles be used for high-quality acrylic sheets?
PMMA particles have a purity of ≥99.5%, a transmittance of more than 92% (data from the American Chemistry Council), and strong weather resistance, suitable for precision processing.
How to avoid bubble defects during production?
Use vacuum drying technology (such as German Leybold equipment) to reduce the moisture content of particles to below 0.02%, and completely eliminate bubbles caused by moisture.
How to control the thickness tolerance of acrylic sheets?
The Swiss Coperion die head is equipped with a 0.02mm precision die lip adjustment device, combined with an online thickness gauge (still available in the UK), with a thickness tolerance within ±0.1mm.
How does surface treatment extend the life of the sheet?
UV-cured coatings (such as American Trinseo technology) form a 5μm protective layer, which passes the ASTM G154 test and has a weather resistance of more than 10 years.
What are the advantages of the intelligent quality inspection system?
The AI visual system (Cognex of Israel) can identify 0.02mm² defects, with a detection speed of 200m/min, and the scrap rate is reduced from 3% to 0.5%.
Is acrylic sheet environmentally friendly?
Data from the European Plastic Recycling Association shows that the new PMMA recycling technology can achieve more than 90% material recycling.
Conclusion
From raw material molecular structure control to AI quality inspection system, modern acrylic extrusion board production has developed into a deep integration of material science, mechanical engineering and information technology. With the breakthrough of environmentally friendly PMMA recycling technology, future board production will achieve a higher level of sustainable development. Only by mastering these core processes can we gain an advantage in this high-end manufacturing competition. Contact Sanyu Acrylic for more professional information if you’re interested in the production.