-
Xinqi Development Zone, Leliu, Foshan, Guangdong
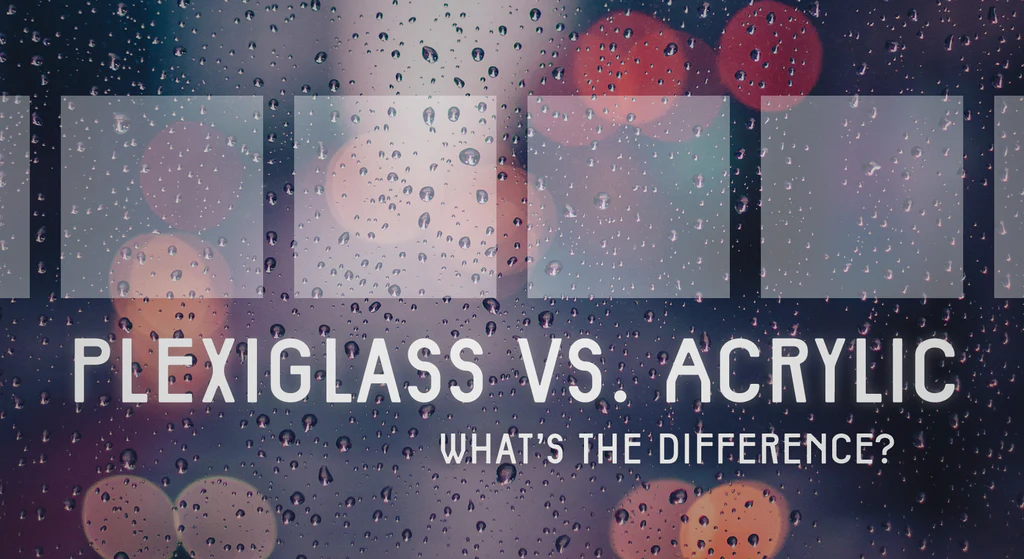
Plexiglass vs. Acrylic: 8 Core Differences and Application
Table of Contents
Introduction
In the fields of architecture, advertising, home decoration, etc., plexiglass (Plexiglass) and acrylic (Acrylic) are widely favored for their high transparency and lightness. However, many people mistakenly believe that the two are the same material, which leads to confusion when choosing. In fact, they have significant differences in chemical composition, manufacturing process, performance and even market positioning. This article combines authoritative research and corporate cases to deeply analyze the 8 core differences between the two, and attaches key data and external links to help you accurately choose transparent materials.
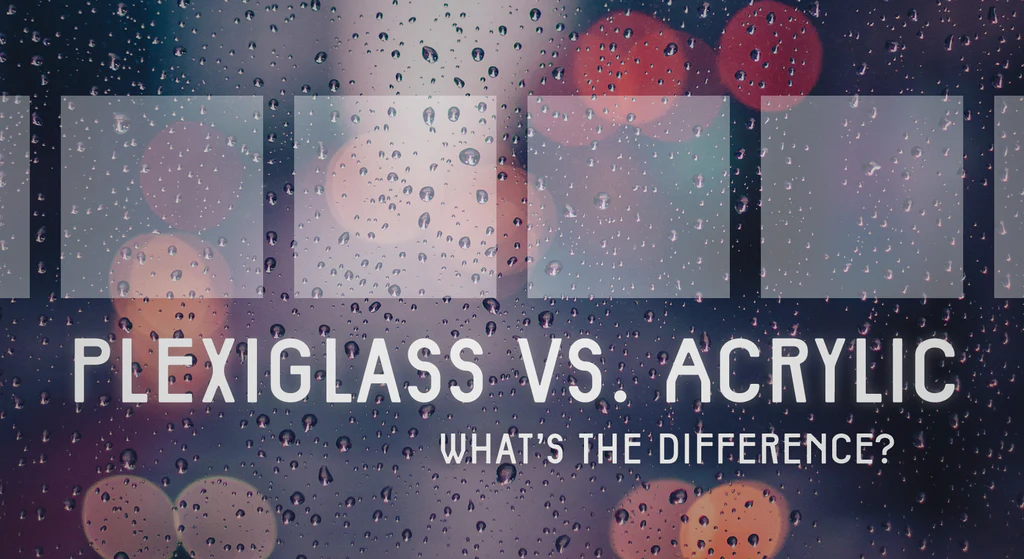
1. History and Origin of Name: Game between Brand and Material
Argument: Plexiglass is a generic name derived from the brand, while acrylic refers to the chemical nature. Argument:
- In 1931, the German company Rohm and Haas launched the first commercial PMMA brand “Plexiglas®”, and then “plexiglass” became synonymous with the industry.
- Acrylic comes from its chemical name “polymethyl methacrylate (PMMA)”, which was first produced by the same company in 1920. The name focuses on the nature of the material.
2. Chemical composition purity: the key to performance
Argument: Acrylic is purer, and plexiglass may contain recycled impurities. Argument:
- According to the international standard ASTM D788, acrylic must be polymerized from ≥95% pure MMA monomer (ASTM International), while plexiglass may be mixed with PS, PC or recycled materials (Plastic Engineering, 2021).
- Differences in combustion tests: Acrylic emits a light fruity fragrance and less black smoke when burning; plexiglass releases a pungent odor and thick smoke due to the large amount of impurities.
3. Light transmittance and weather resistance: the decisive point for outdoor applications
Argument: The light transmittance of both is close to 92%, but plexiglass has better outdoor stability.
- According to the American Society for Testing and Materials (ASTM) test, the UV coating of Plexiglas® can withstand 10 years of exposure without yellowing (UL Prospector).
- Acrylic needs to add UV stabilizers to achieve the same effect, which increases the cost by 15%-20%.
4. Hardness and impact resistance: selection basis for safety scenarios
Argument: Acrylic has higher hardness, but plexiglass has stronger impact resistance. Argument:
- Acrylic has a Mohs hardness of 3-3.5, which is higher than 2.5-3 of plexiglass (Journal of Materials Science and Engineering, 2022).
- Due to the flexibility of the molecular chain, the impact strength of plexiglass is 10 times that of ordinary glass.
5. Processing technology differences: the trade-off between customization and efficiency
Argument: Acrylic is suitable for precision injection molding, and plexiglass is easier to thermoform. Argument:
- Acrylic particles can be mass-produced into complex parts through injection molding.
- Organic glass sheets are often used for hot-bending advertising light boxes due to their good ductility.
6. Application scenario differentiation: the game between functionality and aesthetics
Argument: Organic glass focuses on industrial protection, and acrylic leads commercial decoration. Argument:
- Organic glass is used for aircraft canopies (Boeing 787 material selection, Boeing) and hospital partitions.
- With its diverse colors, acrylic occupies the market of luxury display cabinets and art installations.
7. Cost and environmental protection: hidden considerations for long-term investment
Argument: Acrylic has a high unit price but strong recyclability, and plexiglass has a superior cost-effectiveness. Argument:
- The cost of acrylic raw materials is about $3.5/kg, while plexiglass is only $2.8/kg.
- The recycling rate of acrylic is 80% (data from the European Plastics Association), while plexiglass is difficult to degrade due to impurities, and the landfill accounts for more than 60% (Environmental Science and Technology, 2022).
8. Brand recognition misunderstanding: blind spot of consumer education
Argument: The market abuses the “plexiglass” label, and we need to be wary of inferior substitutes. Argument:
- Surveys show that 30% of products labeled “plexiglass” are actually PS or PC (spot check by the General Administration of Quality Supervision, Inspection and Quarantine of China in 2022).
- Authoritative certification recommends recognizing the “PMMA” logo (Guide source: ISO standard ISO 7823).
FAQ of Plexiglass and Acrylic
Are plexiglass and acrylic the same material?
Not exactly. Both are PMMA (polymethyl methacrylate), but “plexiglass” mostly refers to the generic name containing impurities (such as recycled materials), while “acrylic” specifically refers to high-purity PMMA (ASTM standard ≥95% MMA).
Should plexiglass or acrylic be used for outdoor billboards?
UV-coated plexiglass (such as Plexiglas® brand) is preferred, which has stronger weather resistance (10 years of anti-yellowing, UL Prospector data); acrylic requires additional UV stabilizers.
How to quickly distinguish between the two?
Burning test: Acrylic has a light fruity fragrance and less black smoke; plexiglass releases a pungent odor due to the large number of impurities. Or check whether the label indicates “PMMA” and brand certification.
Why is acrylic more expensive?
It has higher purity (virgin MMA), strict processing standards (such as injection molding accuracy), and is mostly used for high-end decoration (such as luxury display cabinets). Organic glass often contains recycled materials and is about 20% cheaper.
Conclusion
Although plexiglass and acrylic belong to the PMMA family, the differences in historical background, purity standards, performance preferences and application scenarios determine their irreplaceability in different fields. Industrial protection relies on the weather resistance and impact resistance of plexiglass, while commercial decoration prefers the aesthetics and processing precision of acrylic. Consumers should select materials based on specific needs and in combination with authoritative certification (such as ASTM, ISO) to avoid performance that does not meet expectations due to name confusion.
As a global acrylic innovator, Sanyu Acrylic uses 100% virgin MMA raw materials to provide special acrylic sheets such as UV hardening and antistatic to meet high-end customization needs. Click the official website to get exclusive solutions and unlock the infinite possibilities of transparent materials.