-
Strefa rozwoju Xinqi, Leliu, Foshan, Guangdong
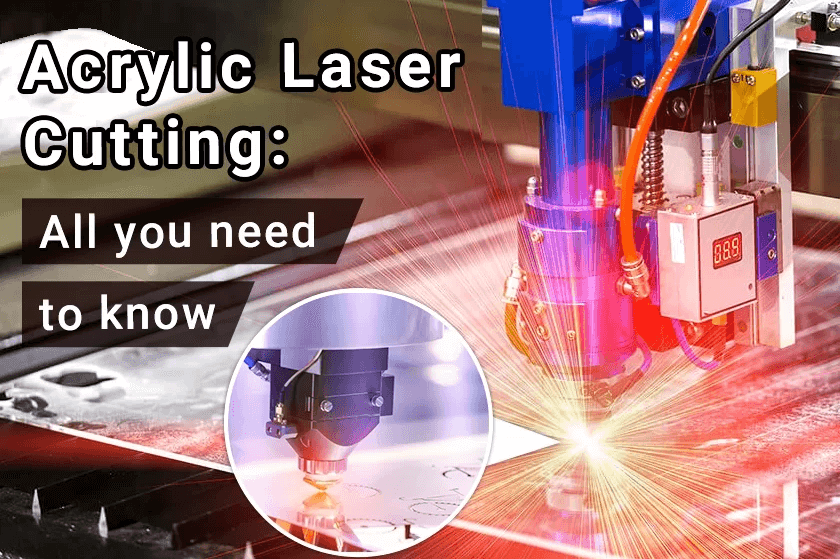
8 podstawowych umiejętności cięcia laserowego arkuszy akrylowych
Spis treści
Wprowadzenie: Innowacyjna wartość technologii cięcia laserowego
Według najnowszego raportu Global Market Insights, globalny rynek urządzeń do cięcia laserowego ma przekroczyć $8 miliardów USD w 2027 roku, z czego obróbka akrylu stanowi 23% udziału w aplikacji. Ten lekki i przepuszczający światło materiał stał się pierwszym wyborem w znakach reklamowych, produkcji przemysłowej, projektowaniu artystycznym i innych dziedzinach ze względu na jego doskonałą plastyczność i estetykę. Aby jednak w pełni wykorzystać zalety techniczne cięcia laserowego, konieczne jest opanowanie umiejętności obsługi systemu. Niniejszy artykuł łączy wiarygodne dane branżowe i praktyczne doświadczenie, aby ujawnić naukowe zasady i praktyczne metody 8 kluczowych umiejętności.
1. Wybór materiału: przełom między akrylem wylewanym a wytłaczanym
Badania przeprowadzone przez Amerykańskie Stowarzyszenie Przemysłu Tworzyw Sztucznych (SPI) pokazują, że gęstość molekularna akrylu wylewanego jest o 15% wyższa niż akrylu wytłaczanego, co bezpośrednio determinuje różnicę w efekcie cięcia:
- Odlew akrylowyŚrednia prędkość skrawania może zostać zwiększona o 20%, a gładkość krawędzi osiąga Ra 0,8 μm (odpowiednik klasy lustrzanej).
- Wytłaczany akrylPod wpływem naprężeń wewnętrznych łatwo powstają mikropęknięcia o wielkości 0,5-1,2 mm.
Porady ekspertów: Płyty wylewane marki Polycast® (parametry produktu) są preferowane do precyzyjnego pakowania komponentów elektronicznych, podczas gdy wytłaczane materiały o wyższej wydajności kosztowej mogą być brane pod uwagę w przypadku krótkoterminowych rekwizytów ekspozycyjnych
2. Trójwymiarowy model optymalizacji parametrów lasera
W białej księdze technicznej firmy TRUMPF Laser (TRUMPF) w Niemczech wskazano, że formuła złotego podziału mocy-prędkości-częstotliwości to:
P = (T×V)/K
Gdzie P to moc (W), T to grubość (mm), V to prędkość (mm/s), a K to współczynnik materiałowy (odlew akrylowy K=120, typ wytłaczany K=90).
Przypadek praktyczny: W przypadku cięcia płyty odlewanej o grubości 3 mm zalecana kombinacja parametrów to: Moc 45 W | Prędkość 12 mm/s | Częstotliwość 2000 Hz (źródło danych: Podręcznik parametrów TRUMPF).
3. Sprzeczne rozwiązanie dla obróbki folii ochronnej
Test przeprowadzony przez Laboratorium Inżynierii Materiałowej MIT wykazał, że zachowanie dolnej folii ochronnej może zmniejszyć uszkodzenia spowodowane zarysowaniami przez 73%, ale należy zauważyć, że:
- Usuń górną folię, aby uniknąć zwęglenia (folia ochronna przyklei się, gdy temperatura przekroczy 160°C).
- Użyj taśmy maskującej 3M serii 2080 (odpornej na temperaturę do 200°C) zamiast oryginalnej folii (Raport z testów produktu)
4. Precyzyjna kontrola wspomagania aerodynamicznego
- Zalecana wartość ciśnienia powietrza: 0,3-0,5 MPa (grubość ≤5 mm); 0,6-0,8 MPa (grubość>5 mm)
- Kąt nachylenia dyszy: Kąt nachylenia 15° może zwiększyć wydajność usuwania zanieczyszczeń o 42%
- Kluczowa rola: Zapobieganie powstawaniu warstwy zwęglenia krawędzi spowodowanej wtórnym spalaniem (redukcja grubości o 0,05-0,1 mm)
5. Praktyka inżynieryjna izolacji termodynamicznej
Przez Trójwymiarowa analiza termowizyjnaStwierdzono, że podniesienie płyty o 2-3 mm może obniżyć temperaturę dna o 58%:
- Rozwiązanie wspierające: płyta o strukturze plastra miodu + ceramiczna kolumna pozycjonująca (przewodność cieplna <1 W/m-K)
- Efekt izolacji: skuteczne unikanie przesunięcia ostrości spowodowanego "efektem soczewki termicznej".
6. Nanopoziomowa precyzja kalibracji ścieżki optycznej
Standardowe wymagania Europejskiego Stowarzyszenia Optycznego (EOS):
- Sprawdzaj przesunięcie reflektora co tydzień (dopuszczalny błąd ±0,02 mm).
- Lusterko ustawiające ostrość należy wymieniać co miesiąc (łączny czas pracy ≥120 godzin).
- Narzędzie do kalibracji: Użyj lokalizatora światła czerwonego + mikrometrycznego systemu pomiarowego
7. Chemiczna optymalizacja procesu przetwarzania końcowego
Eksperymenty porównawcze pokazują, że polerowanie parami dichlorometanu ma najlepszy efekt:
- Czas przetwarzania: 30-45 sekund (15 sekund dłużej na każdy 1 mm wzrostu grubości)
- Chropowatość powierzchni: od Ra 3,2 μm do Ra 0,4 μm
- Wskazówki dotyczące bezpieczeństwa: musi pracować w wyciągu podciśnieniowym (norma OSHA 29 CFR 1910.1450).
8. Konstrukcja optyczna grawerowania odwrotnego
Grawerowanie z tyłu powinno być wykonane na lustrzanym akrylu:
- Wstępne przetwarzanie obrazu: lustrzane odbicie + kompensacja skali szarości 30%
- Regulacja ostrości: Podniesienie osi Z 0,8 razy grubość materiału
- Gęstość energii: 15-20% niższa niż w przypadku grawerowania przedniego
Wnioski: Ulepszony łańcuch wartości dzięki postępowi technologicznemu
Opanowanie tych technik może zwiększyć wydajność przetwarzania o ponad 35% i kontrolować wskaźnik złomu w granicach 2%. Zaleca się regularne uczestnictwo w szkoleniach certyfikacyjnych American Laser Institute (LIA) (Katalog kursów) i utworzenie bazy danych parametrów w celu ciągłej optymalizacji przebiegu procesu. Wraz z rozwojem inteligentnych systemów sterowania, cięcie laserowe osiągnie w przyszłości dokładniejsze dopasowanie parametrów AI, ale podstawowe poznanie materiału i zasady procesu są zawsze kamieniem węgielnym przełomów technologicznych.