-
신치 개발구, 르루, 포산, 광둥성, 신치
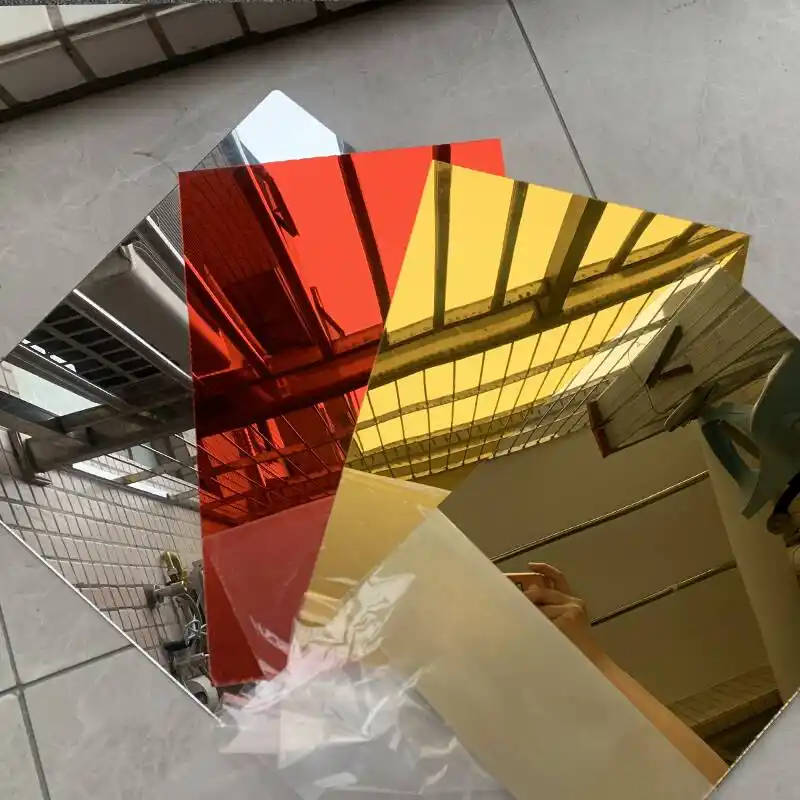
Acrylic Mirror Panels for Harsh Environments
The secret of a high-quality acrylic mirror panel remaining as good as new for ten years in harsh environments lies in the precise collaboration of material science and protection technology.
With its high transparency, light weight and impact resistance, acrylic mirror panels have become a star material in the fields of architectural decoration, advertising display, bathroom and home furnishing. However, its durability is often threatened by multiple environmental threats such as ultraviolet rays, temperature changes, moisture, and chemical corrosion. Through a systematic protection strategy – from molecular-level UV absorbers to nano-hardened coatings, from environmentally adapted material selection to scientific cleaning procedures – the life of acrylic mirror panels can be extended by more than 300%. This article uses empirical data to reveal a full-scenario protection solution to help you break through environmental limitations.
1. UV protection: blocking the “first killer” of aging
In outdoor environments, ultraviolet radiation is the primary cause of yellowing and embrittlement of acrylic. Under long-term sunlight exposure, ordinary acrylic will have a decrease in light transmittance of ≥5% due to molecular chain breakage, and the yellowing index (ΔYI) will be aged if it exceeds 3. The solution requires internal and external coordination:
- Additive UV absorber: Benzotriazole compounds are added to the PMMA substrate to absorb 99% of ultraviolet light in the 300-380nm band. Experiments show that after 2000 hours of xenon lamp aging test in the plate with UV stabilizer, ΔYI is still <1.5.
- Surface coating technology: For example, Tru Vue’s patented anti-reflective coating has both 99% UV blocking and anti-glare functions. Its inorganic silica coating is permanently bonded after baking to avoid delamination and degradation.
케이스: After 5 years of exposure to the Arizona desert, the light transmittance of UV-resistant acrylic billboards only decreased by 2.3%, while that of ordinary boards decreased by more than 15%.
2. Temperature stability: Solve the crisis of thermal expansion and contraction deformation
The thermal deformation temperature of acrylic is only 96℃, and it becomes brittle at a low temperature of 9.2℃. Stress cracking caused by temperature difference is one of the main causes of failure. Multi-dimensional prevention and control strategies include:
- Modified temperature raising technology: Copolymerization introduces cyclohexyl methacrylate (CHMA) to increase the thermal deformation temperature to 120℃. Thick plates (≥8mm) are annealed to eliminate internal stress and can withstand drastic changes from -30℃ to 80℃.
- Structural compensation design: Oversized panels (>60×60 inches) use 6mm thickness and are equipped with reinforced support frames. Each inch of span is equipped with a 16/12 standard bracket to suppress thermal creep.
Extreme test: The modified plate has no cracks or warping after 100 cycles at -40℃~+80℃ (IEC 60068-2-14 standard).
3. Chemical corrosion and damp heat: Ending corrosive environmental erosion
Coastal salt spray, industrial acid rain, and high humidity environment can cause acrylic hydrolysis, swelling, and surface gloss loss:
- Salt spray defense: Chloride ions are isolated through vacuum aluminum metallization layer (such as Silver Mirror Perspex®), and 5% NaCl salt spray test for 1000 hours without corrosion (ASTM B117).
- Moisture-proof molecular design: Low water absorption (0.1%) casting plate is used. In the damp heat aging test (85℃/85% RH), the water absorption is <0.3%, which is much lower than the 0.4% of extruded plate.
Industrial zone application: The acid rain-proof acrylic logo used by factories in the Pearl River Delta is coated with acid and alkali resistant nano coating on the surface, and there is no fogging for three years.
4. Surface hardening technology: “Diamond armor” to resist scratches
The Mohs hardness of acrylic surface is only 3-4, which is easy to be scratched by gravel. High-end hardening solution achieves glass-level protection:
- Siloxane hard coating: The surface is coated with SiO₂ nanoparticles, with a hardness of 6H (pencil hardness) and abrasion resistance increased by 10 times. For example, TruLife acrylic’s proprietary anti-scratch layer can be rubbed with steel wool for thousands of times without visible scratches.
- Microphase separation technology: An interpenetrating network structure (IPN) is formed in PMMA, making the impact resistance 200 times that of ordinary glass, and there is no sharp angle when it breaks.
Data comparison: The hardened acrylic mirror panel has been used in a crowded area of a shopping mall for 2 years, and the surface gloss retention rate is >90%.
5. Scientific maintenance procedures: “Invisible armor” with doubled life
Improper cleaning causes 70% of early damage. Professional maintenance requires strict compliance with regulations:
- 청소 금기 사항: Ammonia and acetone solvents are prohibited. It is recommended to use isopropyl alcohol: water = 1:1 solution + microfiber cloth unidirectional wiping to avoid static electricity adsorption of dust.
- Protective film management: Keep the PE protective film during transportation and installation, avoid stacking during storage, and place vertically with an inclination angle of <10° to prevent bending.
Maintenance experiment: The regularly maintained acrylic bathtub has not turned yellow in 13 years, far exceeding the average lifespan.
6. Material selection and installation: Build durability from the source
Poor quality recycled materials reduce the lifespan by 50%, scientific material selection is the key:
- Substrate certification: Use ISO 9001 certified casting board (such as Weetect brand), 100% pure MMA monomer, no recycled material mixed.
- Environmental adaptation: Choose UV + salt spray double protection board in coastal areas, chemical resistance type in industrial areas, and low-temperature impact-resistant formula in high-cold areas.
Lifespan comparison: Imported acrylic has a lifespan of 10 years under standard installation, while domestic inferior boards turn yellow in only 2-3 years.
The environmental battle of acrylic mirror panels is essentially a collaborative innovation of material science and applied engineering: from the molecular barrier of UV absorbers to the physical armor of hard coatings, from temperature stress calculations to micro-environment cleaning procedures, each step requires precise design. The ultimate solution lies in systematic protection chain – select UV-grade casting plates when selecting materials, implement scientific maintenance during use, and superimpose special protection in extreme environments. Only in this way can this piece of “plexiglass” maintain its mirror-like eternal glory in the midst of time and nature.
자주 묻는 질문
Q1: How does UV light damage acrylic mirror panels?
A: Causes yellowing and brittleness by breaking polymer chains. Add UV absorbers and coatings to block 99% rays.
Q2: Can acrylic mirrors withstand freezing winters?
A: Yes. Modified panels with CHMA copolymer survive -40°C to 80°C thermal cycling (IEC 60068-2-14 certified).
Q3: What protects acrylic mirrors in coastal areas?
A: Vacuum-metallized aluminum layers block salt corrosion. Passes 1000hr salt spray tests (ASTM B117).
Q4: How to prevent scratches on acrylic mirrors?
A: Apply SiO₂ nano-hard coatings (6H pencil hardness). Resists 10,000+ steel wool scrubs.
Q5: Which cleaners destroy acrylic mirrors?
A: Avoid ammonia/acetone. Use 1:1 isopropanol/water + microfiber cloth.
Q6: Why choose cast over extruded acrylic?
A: Cast has 0.1% water absorption (vs 0.4% in extruded), 3X longer lifespan in humidity.