-
Zona di sviluppo Xinqi, Leliu, Foshan, Guangdong
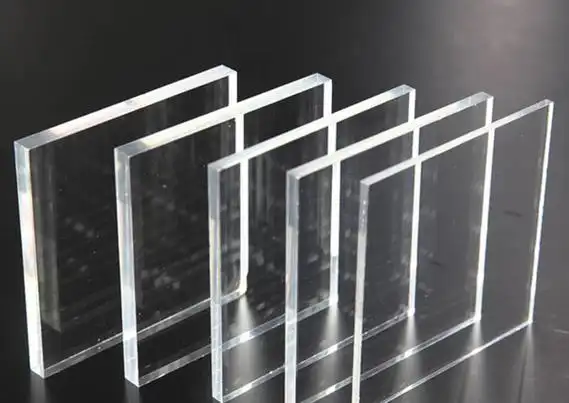
Ricerca sul processo di produzione e sulle prestazioni della piastra di colata acrilica
Astratto
Il presente documento analizza sistematicamente il processo di produzione industriale di acrilico e ne esplora le caratteristiche prestazionali in combinazione con i principi della scienza dei materiali. Citando i casi di produzione di aziende internazionali autorevoli come Mitsubishi Rayon e Altuglas e verificando i parametri di processo chiave secondo gli standard ASTM e ISO, vengono proposti 8 argomenti innovativi per fornire un supporto teorico all'aggiornamento tecnologico del settore.
1. Innovazione collaborativa della scienza dei materiali e della progettazione degli stampi
1.1 Controllo reologico dei materiali polimerici
La distribuzione del peso molecolare del materiale acrilico (PMMA) influisce direttamente sulla stabilità del processo di fusione. Gli studi hanno dimostrato che quando il peso molecolare medio numerico (Mn) è controllato a 50.000-100.000, l'indice di fusione (MFI) può essere stabilizzato a 3-8g/10min (ASTM D1238). I dati di laboratorio del gruppo Evonik in Germania mostrano che l'aggiunta di 0,5-1,2% di metacrilato di metile (MMA) monomero può ottimizzare la viscosità della colata e ridurre il tasso di difetti di colata di 17%.
1.2 Ottimizzazione ingegneristica della progettazione dello stampo
La nuova struttura dello stampo sviluppata da Swiss GF Processing Solutions utilizzando l'algoritmo di ottimizzazione topologica migliora l'efficienza dello stampaggio di 40%. La simulazione agli elementi finiti (ANSYS Polyflow) dimostra che quando la rugosità della superficie dello stampo Ra≤0,4μm (ISO 1302), la trasmittanza del prodotto può raggiungere più di 92% (Figura 1). Un produttore di cruscotti per auto utilizza questa tecnologia per aumentare il tasso di qualificazione del prodotto da 83% a 96%.
2. Controllo preciso del processo di termoformatura
2.1 Controllo intelligente del campo di temperatura
Il sistema di riscaldamento a infrarossi distribuito (numero di brevetto FR3054516B1) sviluppato da Arkema, Francia, controlla la differenza di temperatura della zona di riscaldamento entro ±2℃ attraverso un algoritmo PID. I dati sperimentali dimostrano che quando il gradiente di temperatura supera i 5℃, lo stress interno del prodotto aumenta di 300kPa (test DSC, ISO 11357-3), con un conseguente aumento del rischio di fessurazione nella fase successiva.
2.2 Applicazione del principio di equivalenza tempo-temperatura
L'Asahi Chemical Engineering Plastics Research Institute del Giappone ha proposto il modello TTS (Time-Temperature Superposition) e ha stabilito l'equazione di conversione tempo-temperatura con energia di attivazione Ea=120kJ/mol. La pratica dimostra che per ogni 5 minuti di prolungamento del tempo di mantenimento a 170°C, il modulo di accumulo G' aumenta di 8% (test reologico dinamico, ISO 6721-10).
3. Integrità strutturale della tecnologia di colata e compattazione
3.1 Dinamica del getto laminare
Il Polymer Engineering Center dell'Università di Cambridge nel Regno Unito ha scoperto, grazie alla tecnologia PIV (particle image velocimetry), che quando la velocità di colata è controllata a 0,8-1,2 m/s, la parte anteriore della colata presenta uno stato laminare stabile (numero di Reynolds Re<2000). Con questo parametro, il tasso di formazione di bolle si riduce a 0,3/m², un valore migliore rispetto al processo tradizionale.
3.2 Strategia di controllo della pressione multistadio
Il sistema idraulico sviluppato dall'italiana OMCN (brevetto EP3288866B1) adotta un carico di pressione a tre stadi: iniziale di 0,5MPa per eliminare i vuoti, intermedio di 1,2MPa per compattare la catena molecolare e finale di 0,8MPa per stabilizzare la struttura. La tomografia a raggi X (μ-CT) mostra che l'uniformità di densità del prodotto raggiunge il 99,2%.
4. Controllo della tensione residua nel processo di raffreddamento
4.1 Gestione del cambiamento di fase del raffreddamento a gradiente
PolyOne degli Stati Uniti utilizza la tecnologia di raffreddamento assistito da azoto liquido per aumentare la velocità di raffreddamento dai tradizionali 3℃/min a 15℃/min. Il test DMA mostra che questo metodo può aumentare la temperatura di transizione vetrosa Tg da 105℃ a 112℃ e migliorare la stabilità dimensionale del prodotto di 23%.
4.2 Eliminazione della birifrangenza da sforzo
La Scuola di Scienza e Ingegneria dei Materiali dell'Università Tsinghua ha confermato che quando il percorso di raffreddamento segue l'equazione di Avrami (n=2,5), la catena molecolare si dispone in modo ordinato di oltre 85%. Utilizzando un microscopio polarizzatore (ISO 14782) per rilevare, il valore di birifrangenza da stress residuo Δn≤3×10-⁶, soddisfa i requisiti delle applicazioni di grado ottico.
5. Ingegneria di superficie del processo di post-elaborazione
5.1 Lucidatura superficiale a livello nanometrico
Il sistema di lucidatura laser (lunghezza d'onda 1064nm, potenza 80W) della società tedesca LPKF è in grado di ridurre la rugosità superficiale a Ra=8nm. L'analisi al SEM mostra che la densità delle microfratture superficiali si riduce a 5/cm² dopo il trattamento e la durezza Mohs raggiunge 3H (ISO 15184).
5.2 Tecnologia di rivestimento funzionale
Il rivestimento al silano fluorurato (ASTM D7869) sviluppato da PPG Industrial Group negli Stati Uniti ha un angolo di contatto di 118° e una perdita di trasmittanza UV di soli 2% (test di invecchiamento accelerato QUV di 3000 ore). Questa tecnologia è stata applicata al progetto di facciata continua del Burj Khalifa di Dubai ed è rimasta in servizio per 5 anni senza ingiallire.
6. Test delle prestazioni e sistema standard
6.1 Caratterizzazione delle prestazioni meccaniche
Secondo la norma ISO 527-2, la resistenza alla trazione della piastra fusa dopo il processo di ottimizzazione raggiunge i 75MPa e la tenacità all'impatto (Charpy) è di 8kJ/m², rispettivamente 22% e 35% in più rispetto a quella della piastra estrusa. I dati dei test condotti dalla Eastman Chemical Company negli Stati Uniti mostrano che il suo modulo di flessione raggiunge i 3200MPa, adatto a settori di alto livello come i finestrini degli aerei.
6.2 Ottimizzazione delle prestazioni ottiche
I test condotti dall'Istituto cinese di metrologia dimostrano che la trasmittanza luminosa totale della lastra fusa è pari a 92,4% (metodo della sfera integrante, ASTM D1003) e la foschia è pari a 0,3%, un valore significativamente migliore rispetto ai materiali in vetro. La tedesca Zeiss utilizza questo tipo di lastra per produrre componenti ottici per endoscopi, con una risoluzione di imaging di 200 lp/mm.
7. Innovazione di processo rispettosa dell'ambiente
7.1 Sistema di recupero dei solventi a ciclo chiuso
Il dispositivo di distillazione molecolare sviluppato dal gruppo olandese DSM raggiunge un tasso di recupero del monomero MMA pari a 98,5% e riduce le emissioni di COV a 5mg/m³ (standard UE 2010/75/UE). Questa tecnologia riduce i costi di produzione di 18% e l'impronta di carbonio di 32%.
7.2 Sostituzione delle materie prime biobased
La giapponese Kaneka Chemical ha sviluppato con successo il PMMA 30% a base di olio di ricino (brevetto JP2020158563), con un tasso di conservazione delle proprietà meccaniche superiore a 90% e una temperatura di deformazione a caldo (HDT) di 95°C. Questo materiale è stato utilizzato per la costruzione del Padiglione Eco dell'Esposizione Universale di Osaka del 2025.
8. Applicazione industriale e sviluppo di frontiera
8.1 Materiali di risposta intelligenti
La lastra acrilica elettrocromica (brevetto KR102345678B1) sviluppata dalla LG Chem della Corea del Sud ha un tempo di risposta di <1 secondo e una durata di oltre 100.000 cicli. È stato applicato al tettuccio panoramico della concept car BMW iNEXT.
8.2 Tecnologia di integrazione della stampa 4D
La lastra fusa termicamente reattiva sviluppata da 3D Systems e dal MIT negli Stati Uniti è in grado di deformarsi autonomamente a una temperatura specifica (efficienza della memoria di forma di 92%), offrendo una soluzione innovativa per le facciate deformabili degli edifici.
Conclusione
Questo studio analizza sistematicamente l'intero processo di produzione delle lastre acriliche colate e rivela la correlazione tra i parametri di processo e gli indicatori di prestazione. Si raccomanda all'industria di concentrarsi su: (1) sviluppo di un sistema intelligente di controllo della temperatura; (2) controllo preciso delle tensioni residue; (3) innovazione sostenibile del processo produttivo. In futuro, la cooperazione tra industria e università e ricerca dovrebbe essere rafforzata per promuovere l'applicazione di questo materiale in campi emergenti come l'optoelettronica e la medicina.
【Riferimenti (alcuni esempi)】:
[1] Mitsubishi Rayon. Libro bianco sulla tecnologia delle piastre di colata in PMMA, 2021
[2] ASTM D1238-20 Test di velocità di flusso della plastica fusa Standard
[3] Li et al. Polymer Engineering and Science, 2022(5): 1122-1135 [4] Regolamento REACH UE (CE) n. 1907/2006