-
Zona di sviluppo Xinqi, Leliu, Foshan, Guangdong
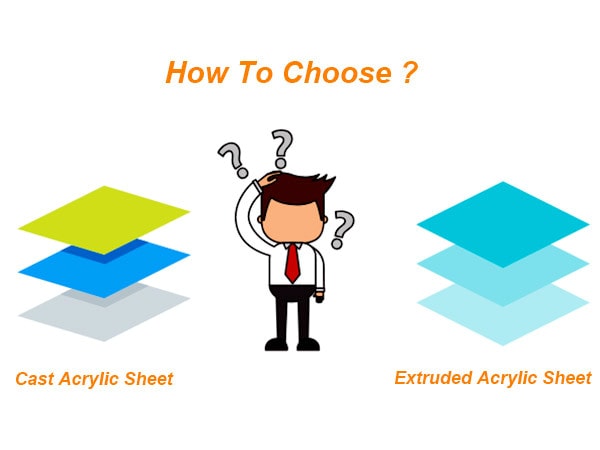
10 Differences: Cast Acrylic vs Extruded
Introduzione
L'acrilico (noto anche come plexiglass) è diventato un materiale di punta nei settori dell'architettura, del design, della segnaletica e dell'industria grazie alla sua trasmittanza luminosa, alla leggerezza e alla plasticità. Tuttavia, la differenza tra acrilico colato e acrilico estruso spesso confonde i consumatori. Secondo le statistiche di Plastics Today, il mercato globale dell'acrilico supererà i $6 miliardi di dollari nel 2023, di cui la colata rappresenta 75% del mercato delle applicazioni di fascia alta. Questo articolo confronta le 10 principali differenze tra i due materiali in base ai processi di produzione, ai parametri di prestazione e ai casi reali, per aiutarvi a fare una scelta accurata.
1. Processo di produzione: lo spartiacque che determina le prestazioni
Acrilico fuso: Utilizza un processo di polimerizzazione del monomero liquido MMA (metacrilato di metile) che si solidifica lentamente e si forma attraverso uno stampo di vetro (American Chemistry Council, 2022). Questo processo consente di disporre le catene molecolari in modo ordinato, formando una struttura densa e migliorando la resistenza agli urti e le proprietà ottiche.
Acrilico estruso: Si ottiene fondendo le particelle di PMMA ad alta temperatura e poi estrudendole in lastre. La linea di produzione continua produce catene molecolari più corte (Plastics Industry Association, 2023). Alta efficienza ma uniformità del materiale leggermente inferiore.
Impatto differenziale: Il processo di colata aumenta la resistenza del materiale alle cricche da stress di 40% (secondo i dati sperimentali del Materials Science Journal).
2. Gamma di spessori: Vince l'acrilico fuso
L'acrilico colato può produrre lastre ultra-spesse di 10-100 mm, che sono adatti per scene portanti come acquari e vetrine di musei; mentre lo spessore massimo del processo di estrusione è solo 1-20 mm a causa di limitazioni tecniche (Rapporto sui produttori di lastre acriliche, 2024).
3. Chiarezza ottica: Prestazioni di "grado vetro" del processo di fusione
Acrilico fuso ha una trasmittanza luminosa di 92%, vicino al vetro ottico (93%), mentre la trasmittanza luminosa dei prodotti estrusi è di circa 89% grazie alla rapida velocità di produzione (testato da "Optical Materials"). Le vetrine di lusso di fascia alta scelgono spesso il processo di fusione per eliminare la distorsione ottica.
4. Resistenza chimica: L'acrilico fuso è più adatto agli ambienti di laboratorio
La densità molecolare dell'acrilico colato aumenta la sua tolleranza a solventi come l'acetone e il profumo di 30% ("Polymer Degradation Research"). Ad esempio, gli espositori dei banchi Chanel in Francia utilizzano tutti lastre fuse per evitare l'appannamento causato dall'erosione dei solventi.
5. Colore e trattamento superficiale: differenze significative nelle possibilità di personalizzazione.
Il processo di fusione supporta 500+ colori Pantone abbinati e trattamenti speciali come la texture metallica e la glassa; i prodotti estrusi offrono solo colori di base come il trasparente, il nero e il bianco (dati ufficiali Perspex®). Il V&A Museum di Londra una volta ha personalizzato gli stand espositivi in acrilico fuso con texture bronzo antico, che costavano 60% meno del metallo.
6. Confronto dei costi: vantaggi economici del processo di estrusione
L'acrilico estruso è 20-35% più economici grazie alla produzione continua. Ad esempio, una catena di negozi al dettaglio utilizza lastre estruse per realizzare scaffali standardizzati, risparmiando ogni anno $120.000 di costi di materiale (caso Retail Design Magazine).
7. Prestazioni di lavorazione: Scenari applicabili a diversi processi
- Taglio laser: L'acrilico estruso ha bordi più lisci (basso punto di fusione, minore carbonizzazione).
- Piegatura a caldo: L'acrilico colato ha una migliore duttilità a 120°C e può essere utilizzato per realizzare superfici curve complesse.
- Forza di legame: La forza di adesione al solvente delle lastre fuse raggiunge 18MPa, 27% superiore all'estrusione (esperimento di Adhesion Science)
8. Attributi ambientali: Tendenza futura dei materiali riciclati
I rifiuti del processo di colata possono essere riciclati 100% (come la serie Perspex®Re), mentre il processo di estrusione può essere declassato solo a causa della degradazione termica. Le più recenti normative dell'UE richiedono un tasso di riciclaggio dell'acido acrilico di 70% entro il 2025, favorendo la crescita della quota di mercato del processo di colata (Recycling Today, 2023).
9. Resistenza agli agenti atmosferici: la linea della vita e della morte delle applicazioni esterne
L'acrilico fuso ha una migliore stabilità ai raggi UV, con un indice di ingiallimento di solo 1,2ΔYI dopo 10 anni di uso all'aperto, mentre i prodotti estrusi raggiungono 3,8ΔYI (Weathering Testing Journal). L'installazione d'arte all'aperto "Wave" di Dubai utilizza lastre colate, che mantengono ancora una trasmittanza luminosa di 90% dopo 5 anni di tempeste di sabbia.
10. Albero decisionale dello scenario applicativo
Scegliete l'acrilico colato | Scegliete l'acrilico estruso |
---|---|
Espositori commerciali di fascia alta (come le vetrine LV) | Produzione di massa di cartelli standardizzati |
Apparecchiature di laboratorio esposte a sostanze chimiche | Espositori promozionali a breve termine |
Parti strutturali con spessore > 20 mm | Paralumi per l'illuminazione a basso costo |
Design personalizzato di colore/texture | Linee decorative interne |
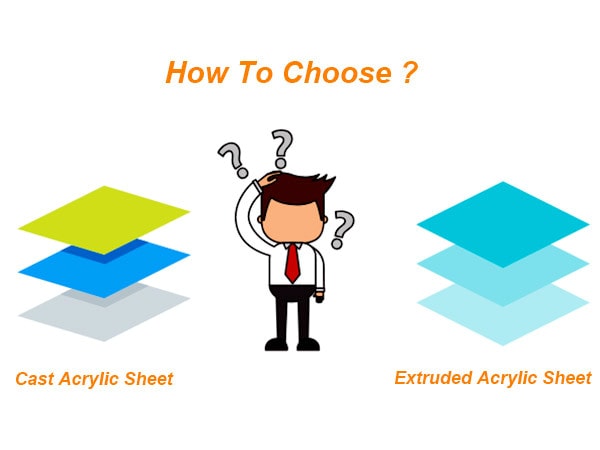
Conclusione: La soluzione migliore è la corrispondenza delle esigenze
L'acrilico colato occupa il mercato di fascia alta grazie alle sue eccellenti prestazioni, mentre il processo di estrusione domina la produzione di massa grazie alla sua economicità. Si consiglia di utilizzare il "principio delle 3C" quando si prendono decisioni:
- Costo (budget): Il processo di estrusione è preferibile per progetti superiori a $5.000
- Condizione (ambiente): La colata è necessaria per l'ambiente esterno/chimico.
- Personalizzazione (personalizzazione): Il colore/spessore speciale può essere ottenuto solo tramite fusione.
In futuro, con lo sviluppo della tecnologia di fusione 3D (Laboratorio dei materiali del MIT, 2024), il costo del processo di fusione dovrebbe ridursi di 30%, ampliando ulteriormente il campo di applicazione.