-
Xinqi Development Zone, Leliu, Foshan, Guangdong
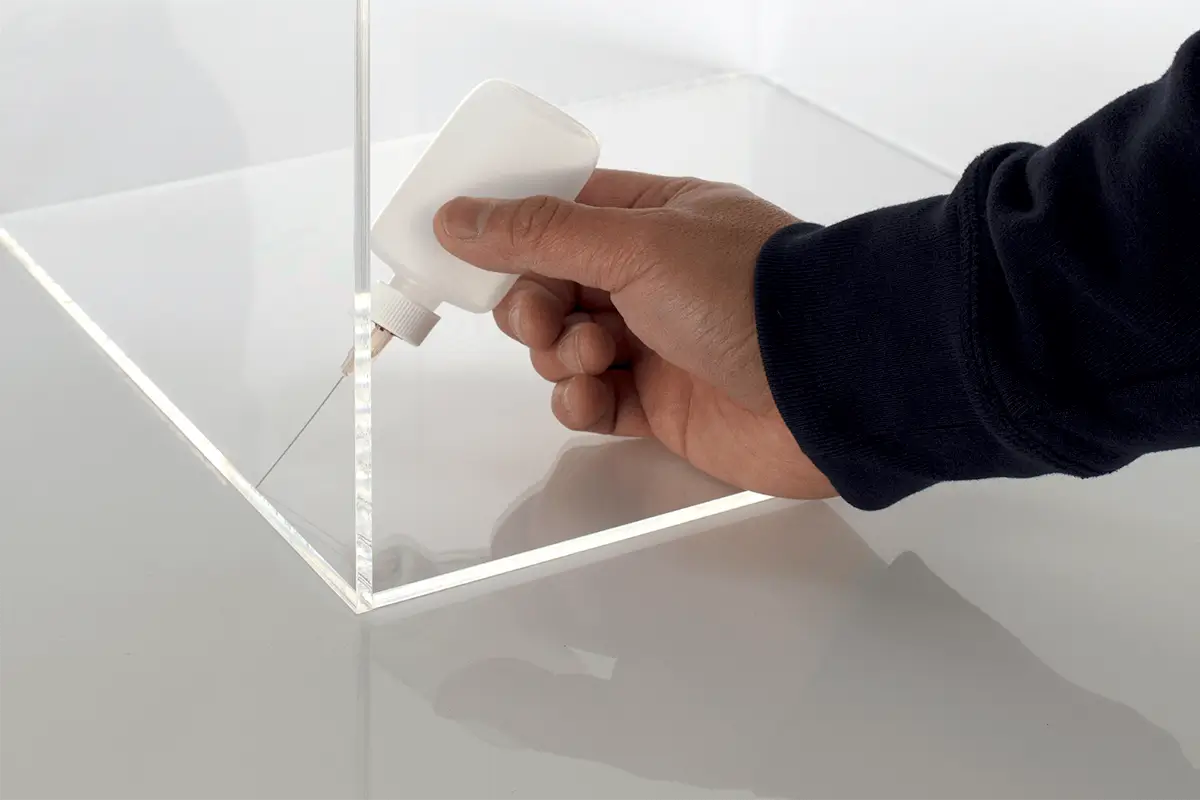
How to Glue Acrylic Sheets: Expert Guide & Safety Tips
Table of Contents
Introduction: Why does acrylic bonding require professional skills?
Acrylic sheet (PMMA) is one of the most popular polymer materials in the 21st century, and its global market size is expected to reach US$8 billion in 2027. From the spiral staircase in the Apple flagship store to the giant viewing window in the Dubai Aquarium, professional-grade acrylic bonding technology has achieved countless amazing engineering miracles. This article will combine the latest research results of the MIT Materials Laboratory with the practical experience of industry experts to systematically analyze the 10 core points of acrylic bonding to help you master this valuable professional skill.
1. Material cognition
Acrylic properties determine the choice of bonding method
The surface energy of acrylic sheet can reach 38-39 mN/m, which directly affects the choice of adhesive. Solvent-based glue achieves molecular-level fusion by dissolving surface molecules, while UV glue relies on light curing to form mechanical anchoring. Professional advice: Weld-On 4 solvent glue is preferred for thick plates (>3mm), and IPS Weld-On 16 UV-curing glue is recommended for thin plates.
Three golden standards for plate quality inspection
- Transmittance inspection: The transmittance of high-quality acrylic should be ≥92% (ASTM D1003 standard)
- Stress test: Use a polarized light detector to observe stress distribution (refer to TAP Plastics inspection guide)
- Thickness tolerance: The thickness error of industrial-grade plates must be controlled within ±0.1mm (Acrylite production specification)
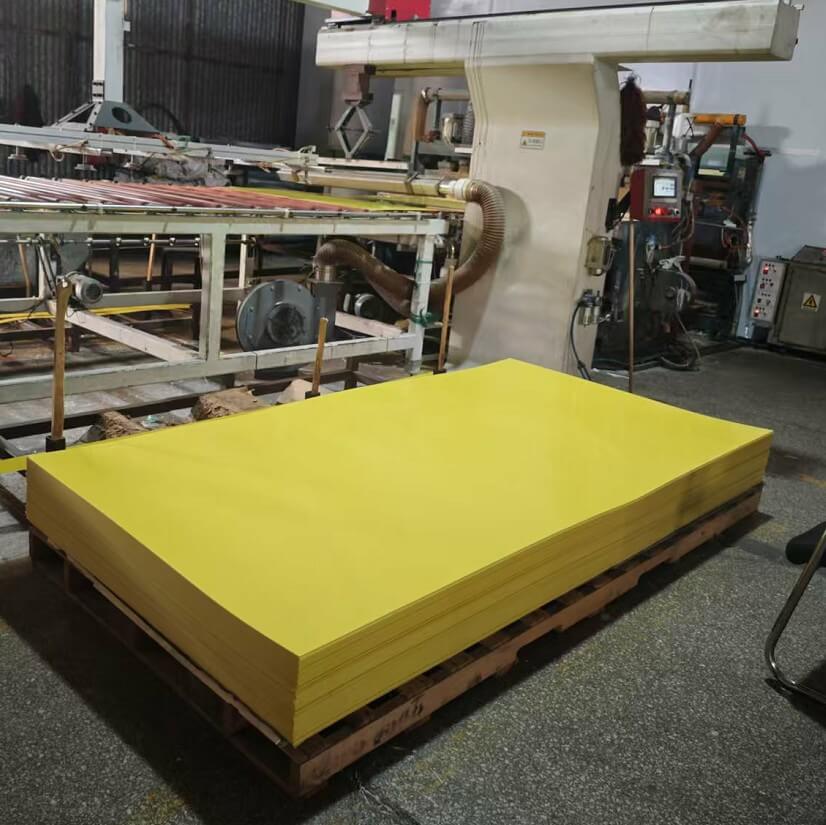
2. Bonding preparation
Five-element system of environmental control
Elements | Standard values | Inspection tools |
---|---|---|
Temperature | 18-25℃ | Digital thermometer and hygrometer |
Humidity | 40-60% RH | Same as above |
Dust concentration | <1000 particles/m³ | Laser particle counter |
Ventilation rate | 0.3-0.5m/s | Anemometer |
Light intensity | <500 lux | Illuminance meter |
Advanced surface treatment techniques
- Chemical treatment: Isopropyl alcohol (IPA) needs to be left to stand for 3 minutes to evaporate after wiping (3M technical white paper recommendation)
- Physical treatment: Use 800-1200 grit sandpaper for 45° cross-grinding (increase specific surface area by 30%)
- Plasma treatment: Industrial-grade equipment can increase surface energy to 72mN/m
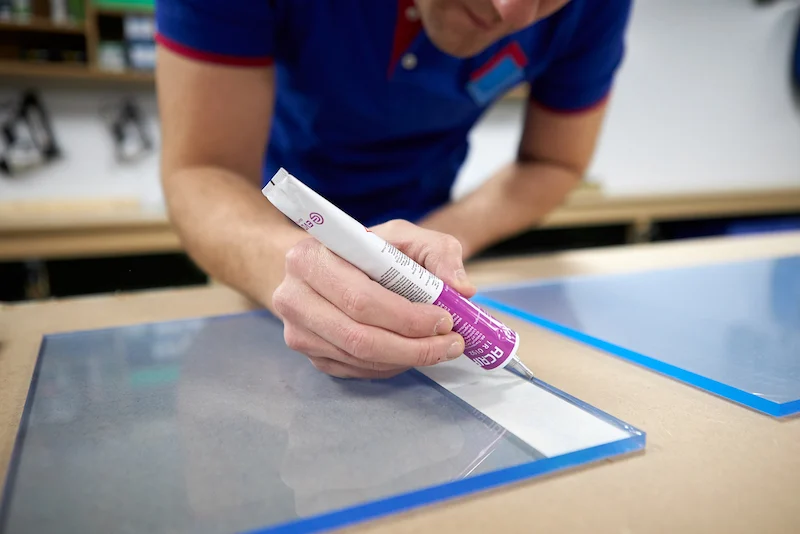
3. Bonding operation
Glue selection decision tree
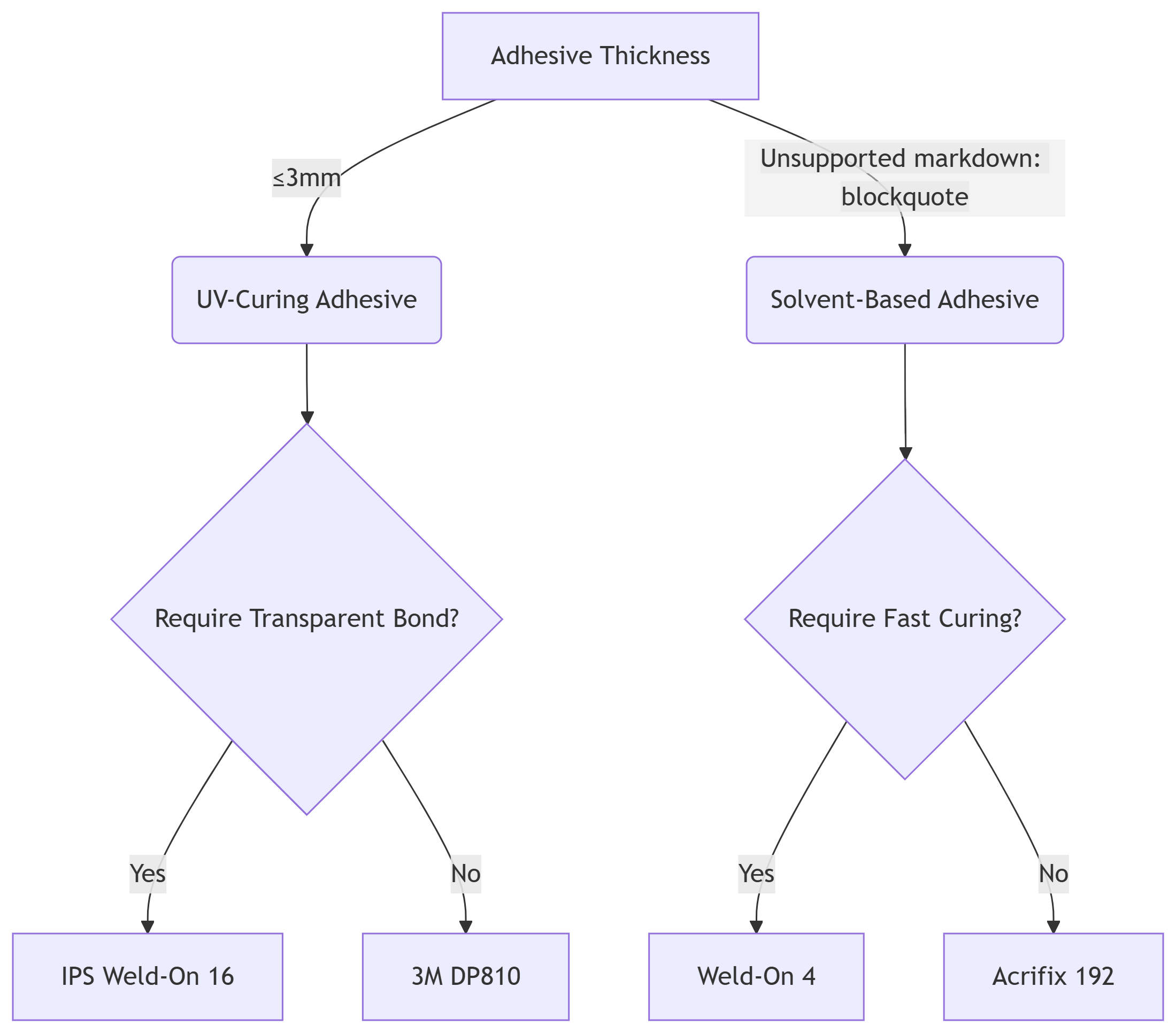
Six-step method for precision injection
- Use 27G precision needle (inner diameter 0.2mm)
- Maintain 45° injection angle
- Control flow rate 0.1ml/s
- Form a continuous “bead chain” glue line
- Apply 0.2-0.3N/cm² pressure
- Maintain pressurized state for 120-180 seconds
4. Quality Control
Three-dimensional monitoring of the curing process
- Time dimension: Establish a curing progress curve (refer to the glue MSDS document)
- Temperature dimension: Use infrared thermal imager to monitor exothermic reaction
- Stress dimension: Apply strain gauge to detect internal stress changes
Professional testing of six indicators
- Shear strength test (ASTM D1002)
- Transmittance test (spectrophotometer)
- Weather resistance test (QUV accelerated aging instrument)
- Impact resistance test (drop ball impact test)
- Dimensional stability (laser rangefinder)
- Chemical resistance (solvent wiping test)
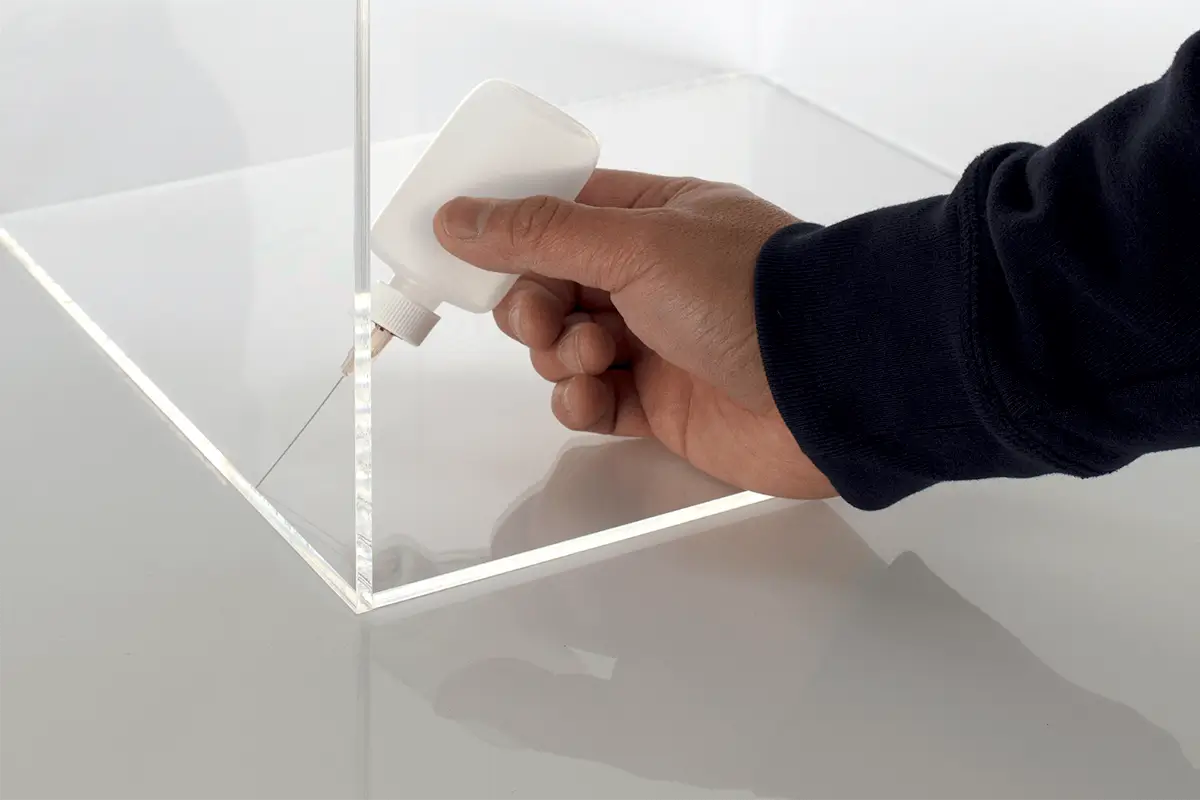
5. Solutions to common problems
Golden rule for bubble elimination
- Prevention plan: Use vacuum injection equipment (vacuum degree ≤ 0.1mbar)
- Repair plan: Syringe extraction method combined with UV curing repair
- Emergency plan: Hot needle perforation exhaust + surface polishing
Stress crack prevention system
- Thermal stress control: Use PID temperature control heating plate (heating rate ≤ 3℃/min)
- Mechanical stress elimination: Design 5% flexible buffer structure
- Chemical stress balance: Apply stress dispersion coating (such as Evonik ACRYLITE® AR coating)
FAQs of Gluing Acrylic Sheet
What’s the best adhesive for thick acrylic sheets?
Use solvent-based cement like Weld-On 4 for sheets >3mm.
How to remove air bubbles during bonding?
Apply vacuum injection (≤0.1mbar) or use a fine needle for extraction.
Can I use super glue for acrylic?
No – cyanoacrylate causes stress cracks. Opt for UV-cured adhesives instead.
Conclusion: From craft to art
Acrylic bonding technology is undergoing a transformation from experience-oriented to data-driven. The latest research from RWTH Aachen University in Germany shows that the use of AI visual inspection can reduce the bonding defect rate to 0.03%. It is recommended that practitioners regularly participate in the bonding engineer certification training held by ASM International, and pay attention to the latest research results of the International Journal of Adhesion and Adhesives. Remember: excellent bonding is not only a victory of technology, but also a deep understanding of the nature of materials. Contact Sanyu Acrylic Sheet for more professional information.