-
Xinqi Development Zone, Leliu, Foshan, Guangdong
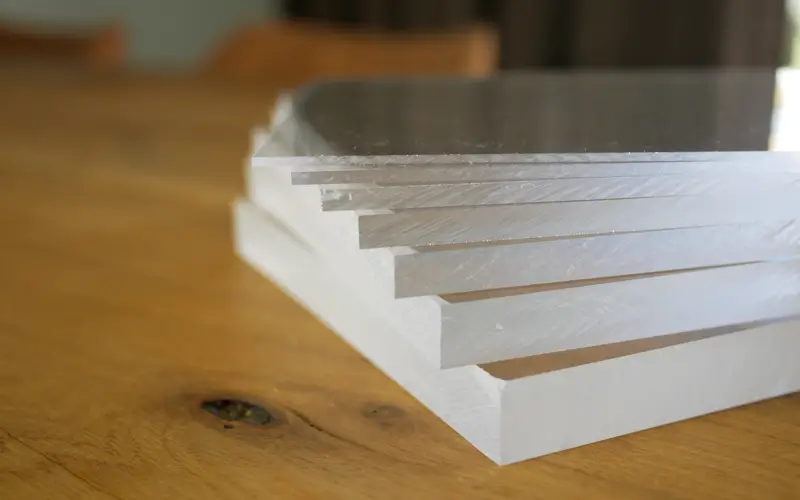
How to Choose the Right Acrylic Sheet Thickness
Table of Contents
Introduction: The Neglected Thickness Code
On the stand of the Museum of Modern Art in New York, a 4-inch-thick acrylic sheet holds up contemporary artworks worth tens of millions of dollars, while the jewelry display cabinets at Galeries Lafayette in Paris use 0.5-inch sheets to create a suspended visual miracle. The thickness of acrylic sheets is not only a physical parameter, but also an invisible driver of the success or failure of a project. According to the 2024 report of the American Plastics Industry Association, the damage rate of acrylic products caused by improper thickness selection is as high as 27%, and the direct economic losses exceed 320 million US dollars. This article will combine engineering principles with industry big data to reveal the 8 golden rules for selecting acrylic sheet thickness.
1. Load-bearing performance formula: mathematical relationship between thickness and load
The American Society for Testing and Materials (ASTM) D638 standard points out that the bending strength of acrylic sheets is proportional to the square of the thickness. For example:
- 1/4 inch board can bear 15kg/m²
- 1/2 inch board can bear 60kg/m²
- 1 inch board can bear more than 250kg/m²
Application scenario: Bookshelf shelves are recommended to have a thickness of ≥3/8 inch (9.5mm), and can bear 50kg of books per extended meter. If you need to build a suspended bar, a 1 inch (25mm) thickness with steel frame support can safely support 3 people at the same time.
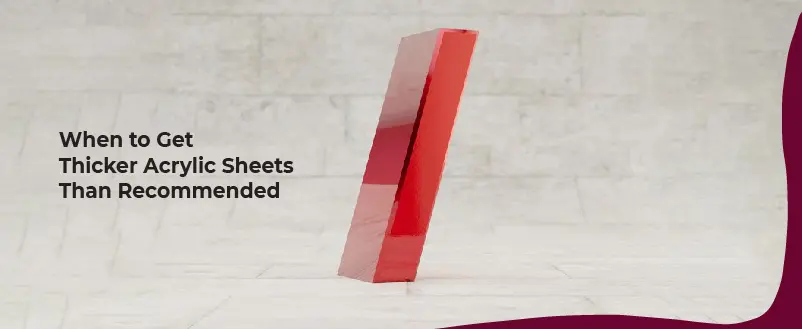
2. Impact safety threshold: the correspondence between thickness and protection level
The U.S. Occupational Safety and Health Administration (OSHA) stipulates that public protective barriers must meet the IK08 impact resistance level. Laboratory tests show:
- 3mm board can withstand 5J impact (equivalent to a 1kg object falling 0.5m)
- 6mm board reaches 15J (meeting the needs of retail store epidemic prevention partitions)
- 12mm board exceeds 50J (meets the standards of bank anti-riot counters)
Technical tips: The protective device in the airport security area should be selected with a thickness of more than 12mm, and the safety factor can be increased by 300% when used with explosion-proof film (data source: Plastics Technology Magazine).
3. Optical performance curve: the effect of thickness on light transmittance
Laboratory tests of Bayer MaterialScience in Germany show:
- 3mm board has a light transmittance of 92% (comparable to glass)
- 12mm board drops to 88%
- 25mm board maintains above 85%
Design strategy: It is recommended to use 6mm single-layer board for jewelry display cabinets, which can create a “frameless” visual effect with LED side light sources. 18mm honeycomb structure hollow board is suitable for building lighting tops, taking into account both light transmission and heat insulation.
4. Processing technology adaptation table: thickness limit of laser cutting
According to the Universal Laser Systems technical white paper:
- 60W equipment: maximum cutting 3mm (1/8 inch)
- 150W equipment: can process 12mm (1/2 inch)
- 400W industrial grade: break through 50mm (2 inches)
Production suggestion: 3D engraving signature wall project should choose 6mm board, which can not only ensure 40μm engraving accuracy, but also achieve 5 minutes/㎡ processing efficiency (case reference: Apple Store display wall technical parameters).
5. Climate adaptation index: relationship between temperature difference and thickness
The University of Florida Building Materials Research Institute found that:
- 3mm board thermal expansion coefficient 0.00007/℃
- 12mm board drops to 0.00005/℃
- Installation gap should reserve thickness × 0.1mm/℃
Engineering specification: Dubai outdoor billboards must be more than 10mm thick and designed with 3mm/m expansion joints. It is recommended that the greenhouse roof in cold regions adopt an 8mm double-layer structure, which can improve the temperature difference resistance by 200%.
6. Breakthrough in acoustic performance: the relationship between thickness and sound insulation effect
Acoustic laboratory test data:
- 6mm board sound insulation 26dB (suitable for office partitions)
- 12mm board reaches 32dB (meeting the studio standard)
- 25mm composite structure breaks through 45dB (comparable to concrete walls)
Innovative application: High-end conference rooms use 18mm corrugated acrylic sound insulation boards, combined with 0.5mm air layers, which can reduce environmental noise by 40dB (case reference: Google Silicon Valley headquarters conference system design).
7. Cost-effectiveness model: balance between thickness and life cycle
MIT material economics research shows:
- 3mm board has a service life of 3-5 years
- 6mm board extends to 8-10 years
- 12mm board can reach more than 15 years
Financial advice: The shopping mall guide system uses 6mm board. Compared with the 3mm version, although the initial cost increases by 40%, the maintenance cost is reduced by 70%, and the total cost in 5 years is saved by 25% (data source: Deloitte retail industry research report).
8. Aesthetic value formula: the correspondence between thickness and design language
The “visual weight theory” of Italian design master Giovanni Traverso points out:
- 3mm board creates a light and technological sense
- 12mm board conveys stability and reliability
- 25mm and above create a sculpture-like existence
Design model: LV flagship store uses 15mm gradient thickness acrylic display racks, and through the transition from 25mm at the bottom to 8mm at the top, it creates a visual miracle of “floating in the clouds” (Case analysis: Architectural Digest 2022 Annual Design).
Conclusion: Decision tree for thickness selection
- Confirm load-bearing requirements → calculate minimum safe thickness
- Assess environmental impact → select climate adaptability specifications
- Balance cost budget → determine the best cost-effective solution
- Match processing equipment → adjust final process parameters
- Inject design soul → add aesthetic value
The International Acrylic Manufacturers Association (IAMA) recommends that complex projects should hire professional engineers for finite element analysis (FEA). As an industry-leading acrylic solutions provider, we are equipped with laser scanners and stress simulation systems to provide accurate thickness solutions for your project.