-
Zone de développement de Xinqi, Leliu, Foshan, Guangdong
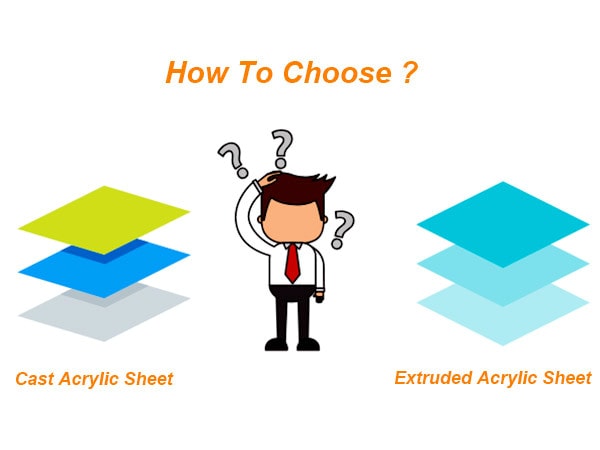
10 Differences: Cast Acrylic vs Extruded
Introduction
L'acrylique (également connu sous le nom de plexiglas) est devenu un matériau vedette dans les domaines de l'architecture, du design, de la signalisation et de l'industrie en raison de sa transmission de la lumière, de sa légèreté et de sa plasticité. Cependant, la différence entre l'acrylique coulé et l'acrylique extrudé est souvent source de confusion pour les consommateurs. Selon les statistiques de Plastics Today, le marché mondial de l'acrylique dépassera $6 milliards de dollars américains en 2023, dont 75% pour le marché des applications haut de gamme. Cet article compare les dix principales différences entre les deux matériaux sur la base des processus de production, des paramètres de performance et de cas concrets, afin de vous aider à faire un choix précis.
1. Processus de fabrication : la ligne de partage des eaux qui détermine la performance
Acrylique coulé: Il utilise un monomère liquide, le MMA (méthacrylate de méthyle), qui est polymérisé et lentement solidifié et mis en forme dans un moule en verre (American Chemistry Council, 2022). Ce processus permet aux chaînes moléculaires d'être arrangées de manière ordonnée, formant une structure dense, améliorant la résistance aux chocs et les propriétés optiques.
Acrylique extrudé: Il est fabriqué en faisant fondre des particules de PMMA à haute température et en les extrudant ensuite en feuilles. La chaîne de production continue permet d'obtenir des chaînes moléculaires plus courtes (Plastics Industry Association, 2023). Rendement élevé mais uniformité du matériau légèrement inférieure.
Impact différentiel: Le processus de coulée augmente la résistance du matériau à la fissuration sous contrainte de 40% (selon les données expérimentales du Materials Science Journal).
2. Gamme d'épaisseurs : Acrylique coulé gagne
L'acrylique coulé permet de produire des feuilles ultra-épaisses de 10-100mmqui conviennent pour les scènes porteuses telles que les aquariums et les vitrines de musée ; tandis que l'épaisseur maximale du processus d'extrusion n'est que de 1-20mm en raison de limitations techniques (Rapport du fabricant de feuilles acryliques, 2024).
3. Clarté optique : Performance du processus de moulage de qualité "verre".
Acrylique coulé a un facteur de transmission de la lumière de 92%proche du verre optique (93%), tandis que la transmission lumineuse des produits extrudés est d'environ 89% en raison de la rapidité de production (testé par "Optical Materials"). Les vitrines de luxe haut de gamme choisissent souvent le procédé de moulage pour éliminer les distorsions optiques.
4. Résistance aux produits chimiques : L'acrylique coulé convient mieux aux environnements de laboratoire
La densité moléculaire de l'acrylique coulé augmente sa tolérance aux solvants tels que l'acétone et le parfum de 30% ("Polymer Degradation Research"). Par exemple, les présentoirs des comptoirs Chanel en France utilisent tous des plaques coulées pour éviter la formation de buée due à l'érosion par les solvants.
5. Couleur et traitement de surface : différences significatives dans les possibilités de personnalisation
Le processus de coulée soutient Correspondance de plus de 500 couleurs Pantone Les produits extrudés n'offrent que des couleurs de base telles que le transparent, le noir et le blanc (données officielles Perspex®). Le musée V&A de Londres a déjà personnalisé des stands d'exposition en acrylique coulé texture bronze antique, qui coûtaient 60% moins cher que le métal.
6. Comparaison des coûts : avantages économiques du procédé d'extrusion
L'acrylique extrudé est 20-35% moins cher grâce à la production en continu. Par exemple, une chaîne de magasins de détail utilise des plaques extrudées pour fabriquer des étagères standardisées, ce qui lui permet d'économiser $120 000 euros par an en coûts de matériaux (cas de Retail Design Magazine).
7. Performance de traitement : Scénarios applicables à différents processus
- Découpe au laser: L'acrylique extrudé a des bords plus lisses (point de fusion bas, moins de carbonisation).
- Pliage à chaud: L'acrylique coulé présente une meilleure ductilité à 120°C et peut être utilisé pour réaliser des surfaces courbes complexes.
- Résistance de l'adhérence: Résistance de l'adhérence au solvant des tôles coulées atteint 18MPa27% plus élevé que l'extrusion (expérience de la science de l'adhérence)
8. Caractéristiques environnementales : Tendance future des matériaux recyclés
Les déchets issus du processus de coulée peuvent être recyclés à 100% (comme la série Perspex®Re), tandis que le processus d'extrusion ne peut être déclassé qu'en raison de la dégradation thermique. Les dernières réglementations européennes exigent un taux de recyclage de l'acide acrylique de 70% d'ici 2025, ce qui stimule la croissance de la part de marché du procédé de coulée (Recycling Today, 2023).
9. Résistance aux intempéries : la ligne de vie et de mort des applications extérieures
L'acrylique coulé présente une meilleure stabilité aux UV, avec un indice de jaunissement de seulement 1.2ΔYI après 10 ans d'utilisation en extérieur, tandis que les produits extrudés atteignent 3.8ΔYI (Weathering Testing Journal). L'installation artistique extérieure "Wave" de Dubaï utilise des plaques coulées qui conservent une transmission lumineuse de 90% après 5 ans de tempêtes de sable.
10. Arbre de décision du scénario d'application
Choisissez l'acrylique coulé | Choisissez l'acrylique extrudé |
---|---|
Présentoirs commerciaux haut de gamme (tels que les vitrines LV) | Production en masse de panneaux standardisés |
Matériel de laboratoire exposé à des produits chimiques | Présentoirs promotionnels à court terme |
Pièces structurelles d'une épaisseur > 20 mm | Abat-jour d'éclairage à faible coût |
Couleur/texture personnalisée | Lignes décoratives intérieures |
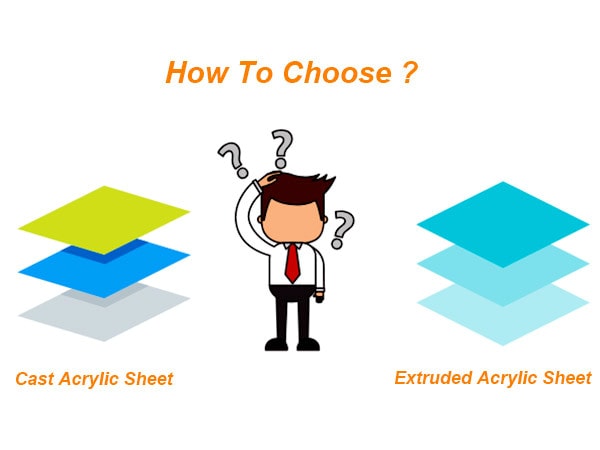
Conclusion : L'adéquation des besoins est la meilleure solution
L'acrylique coulé occupe le marché haut de gamme grâce à ses excellentes performances, tandis que le processus d'extrusion domine la production de masse grâce à sa rentabilité. Il est recommandé d'utiliser le "principe des 3C" lors de la prise de décision :
- Coût (budget) : Le procédé d'extrusion est privilégié pour les projets de plus de $5.000
- Condition (environnement) : Le moulage est nécessaire pour les environnements extérieurs/chimiques.
- Personnalisation (personnalisation) : Les couleurs et épaisseurs spéciales ne peuvent être obtenues que par moulage.
À l'avenir, avec le développement de la technologie de moulage en 3D (Laboratoire de matériaux du MIT, 2024), le coût du processus de coulée devrait être réduit de 30%, ce qui élargit encore le champ d'application.