-
Zone de développement de Xinqi, Leliu, Foshan, Guangdong
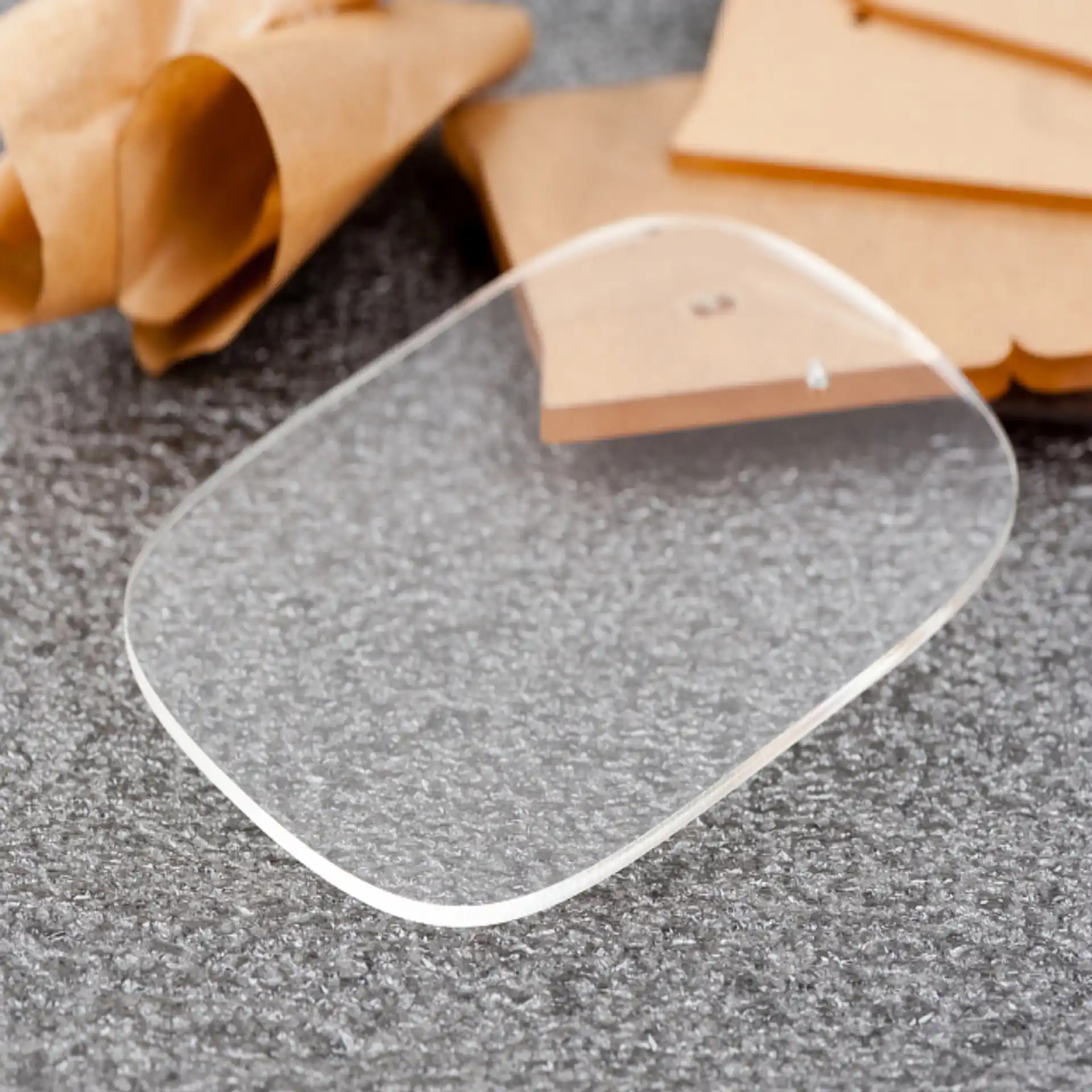
Obtenez des bords acryliques semblables à du verre grâce au polissage à la flamme
Dans les domaines des écrans haut de gamme, des murs-rideaux de bâtiments et des installations artistiques, la finition des bords d'un panneau acrylique détermine souvent la valeur finale du produit. Lorsque le meulage et le polissage traditionnels sont difficiles à réaliser des bords transparents comme du verre, technologie de polissage à la flamme se distingue par sa haute efficacité et ses excellents résultats - l'opérateur balaie le bord de l'acrylique avec un pistolet à flamme, et le bord initialement mat et rugueux devient instantanément aussi transparent que du cristal. Derrière ce processus magique se cache la compréhension précise des propriétés des matériaux et du contrôle thermique.
1. L'essence technique du polissage à la flamme
Le polissage à la flamme est essentiellement une technologie de remodelage par micro-fusion de surface. L'acrylique (PMMA) est un matériau thermoplastique. Lorsqu'il est chauffé à environ 105°C, il atteint son point de ramollissement. À ce moment-là, la couche moléculaire de surface s'écoule mais la structure globale reste solide. Le polissage à la flamme tire parti de cette caractéristique. Il fait fondre les fines imperfections de la surface à une température élevée et courte, utilise la tension superficielle pour ré-égaliser le matériau et forme un bord optiquement transparent après refroidissement.
Comparé au polissage mécanique, le polissage à la flamme présente des avantages significatifs pour structures géométriques complexes. Qu'il s'agisse des rainures courbes des caractères publicitaires en cristal ou de la structure des trous intérieurs des sculptures de formes spéciales, la flamme peut atteindre les coins morts difficiles à manipuler avec les outils traditionnels. Les données expérimentales montrent qu'il ne faut que 15 à 20 secondes à un opérateur professionnel pour effectuer le polissage des bords d'un mètre d'acrylique, ce qui est plus de 5 fois plus efficace que le polissage mécanique. Cependant, cette technologie a des exigences de base pour l'épaisseur du matériau. Seules les plaques de plus de 3 mm peuvent résister aux chocs thermiques sans se déformer. Les plaques minces nécessitent des compétences plus avancées.
2. Sélection de l'équipement et optimisation de la flamme
La qualité de la flamme est le facteur clé du succès du polissage :
- Polisseuse à flamme hydrogène-oxygène: Elle produit un mélange gazeux hydrogène-oxygène par électrolyse de l'eau, avec une température de combustion d'environ 1537,8°C. La flamme est pure et exempte de particules de carbone, évitant ainsi la contamination de la surface acrylique. C'est le premier choix pour le traitement haut de gamme
- Pistolet à propane: Il a un faible coût mais doit être ajusté avec précision à une flamme conique bleue (longueur 5-10cm). La pointe de la flamme jaune provoquera un dépôt de suie
- Micro-torche à butane: Elle convient aux réparations de petites surfaces et est facile à contrôler
Le mécanisme de pulvérisation de flamme automatique développé dans la technologie brevetée (CN202311144808.2) réalise un réglage en temps réel de l'intensité de la flamme grâce à un système d'alimentation en gaz à double voie pour assurer un chauffage uniforme des plaques de différentes épaisseurs. La configuration de sécurité est tout aussi importante. La zone de travail doit être équipée d'un système de ventilation antidéflagrant, et l'opérateur doit porter des gants résistants à la chaleur en fibre de carbone (niveau de protection ≥800℃) et un masque anti-UV.
3. Processus d'opération standardisé
Prétraitement du substrat Le bord acrylique après la coupe doit être initialement poli avec du papier de verre de grain 400 pour éliminer les marques de scie, puis finement poli avec du papier de verre à l'eau de grain 800 ou plus jusqu'à ce qu'il n'y ait pas de grain évident. Après chaque processus, il doit être nettoyé avec alcool anhydre et un chiffon non pelucheux. Toute tache d'huile ou de poussière formera des défauts permanents à haute température.
Technologie de contrôle thermique dynamique
- Gardez une distance de 5 à 10 cm entre le pistolet et la plaque, et déplacez-vous à une vitesse uniforme de 10cm/s
- Chaque bord est traité pendant pas plus de 1 seconde
- La plaque épaisse adopte la stratégie de « brûlage flash multiple » (refroidissement après 30 secondes à chaque fois)
Observer l'état de fusion est le point technique central : Si la réflexion du miroir apparaît sur la surface, retirez immédiatement la flamme. Si de minuscules bulles ou des marques blanches brumeuses sont générées, cela signifie qu'il est surchauffé. Pour les plaques minces d'une épaisseur inférieure à 3 mm, une plaque de cuivre peut être fixée à l'arrière pour aider à dissiper la chaleur.
4. Solutions de polissage pour les structures spéciales
Polissage des trous internes (telles que les structures de trous d'un diamètre de 16 mm et d'une épaisseur de paroi de 2,5 mm) nécessite des méthodes créatives :
- Convertir le micro pistolet en un buse incurvée en forme de L
- Ajuster l'intensité de la flamme à 1/3 de la valeur normale
- Utiliser un fonctionnement intermittent de « brûlage ponctuel de 0,5 seconde + rotation de la pièce »
- Pré-intégrer le tige centrale métallique dans le trou pour absorber l'excès de chaleur
Bord incurvé Le traitement nécessite une combinaison avec un équipement automatisé. Le dispositif de polissage à la flamme à déplacement décrit dans le brevet CN117584436B contrôle la trajectoire du pistolet à travers un système servo programmable et fait tourner de manière synchrone la pièce pour maintenir l'angle de polissage optimal. Pour les plaques très grandes (>2m), il est recommandé d'utiliser un établi de positionnement avec une couche intermédiaire refroidie à l'eau pour éviter l'accumulation de température locale.
5. Analyse et contrôle des défauts de qualité
Les problèmes courants dans le polissage à la flamme sont essentiellement le produit d'un emballement thermique :
- Enroulement des bords: principalement dû à la concentration de chaleur sur le bord à angle droit de la plaque épaisse, le pré-chanfreinage à 45° peut disperser la contrainte
- Taches blanches atomisées: la flamme reste trop longtemps, provoquant une dégradation moléculaire, et doit être légèrement polie avec du papier de verre de grain 800 avant de repolir
- Piqûres de bulles: la teneur en humidité du matériau dépasse la norme (doit être <0,2%), et il doit être séché à 80℃ pendant 4 heures avant le traitement
Les facteurs environnementaux sont souvent ignorés : Lorsque l'humidité>70%, la vapeur d'eau se condense sur la surface de la plaque froide, ce qui entraîne des fissures en forme d'étoile sur la surface polie ; Vitesse du vent>1m/s provoque un refroidissement et une déformation inégaux. Il est recommandé de travailler dans un atelier à température et humidité constantes (température 23±2℃, humidité 50±5%).
6. Évolution technologique et direction de l'innovation
Les technologies de pointe actuelles se concentrent sur contrôle intelligent:
- Le module de mesure de la température infrarouge surveille la température de surface de la carte en temps réel
- Le système visuel identifie automatiquement les caractéristiques géométriques des bords
- Ajustement adaptatif des paramètres (tel que le système de liaison servo dans le brevet de Longnan Xintao Acrylic Technology)
Les machines de polissage à l'hydrogène-oxygène évoluent vers fabrication verte. La nouvelle génération d'équipements intègre un système de circulation des eaux usées, et l'efficacité de l'électrolyse est augmentée à 3,2 kWh/m³, ce qui est 40% plus économe en énergie que les équipements traditionnels. Le processus composite (tel que l'assistance liquide de polissage chimique + flamme) peut traiter des panneaux ultra-minces de 0,8 mm, élargissant ainsi les limites techniques.
Comparaison des données d'un fabricant de présentoirs haut de gamme : Le polissage traditionnel des roues en tissu prend 7 minutes par pièce, avec un taux de réussite de 85% ; après la transformation intégrée du système de polissage à la flamme, le traitement d'une seule pièce est réduit à 1,2 minute, et le taux de réussite passe à 98%.
Conclusion : La philosophie de la température de Seiko Art
Le polissage à la flamme transforme l'énergie thermique apparemment destructrice en un moyen de créer la perfection. L'essence de cette compétence réside dans le équilibre précis de la chaleur et du temps. De l'agilité des pistolets de pulvérisation manuels à la précision des équipements automatisés, l'évolution de la technologie a toujours tourné autour d'un objectif central : capturer le moment magique du gel du brillant au moment où les molécules d'acrylique commencent à s'écouler. Lorsque le premier faisceau de lumière pénètre le bord poli sans entrave, la sublimation des produits industriels aux œuvres d'art optiques est achevée.
Expansion des ressources faisant autorité:
- Association internationale des fabricants d'acrylique – Normes techniques des matériaux
- Rapport de test des matériaux SGS – Données sur l'altération de la surface polie
- Équipement de polissage à la flamme allemand Roth – Solutions de qualité industrielle
- Société américaine des ingénieurs plastiques – Livre blanc sur la technologie de transformation des thermoplastiques
FAQs
Q1 : Quel type de flamme est le meilleur pour le polissage de l'acrylique ?
R : Le mélange hydrogène-oxygène crée des flammes sans suie, tandis que le propane nécessite un ajustement précis du cône bleu pour éviter les dépôts de carbone.
Q2 : Les feuilles d'acrylique minces (<3 mm) peuvent-elles être polies à la flamme ?
R : Oui, en utilisant un support de dissipateur thermique en cuivre et des intervalles de chauffage flash de 0,5 seconde pour éviter la déformation.
Q3 : Pourquoi des stries blanches apparaissent-elles pendant le polissage ?
R : Causé par une surchauffe. Refroidir la feuille, poncer légèrement avec du papier de verre de grain 800 et repolir à une température plus basse.
Q4 : Comment polir efficacement les bords acryliques incurvés ?
R : Utilisez des systèmes servo programmables avec des supports de pièces rotatifs pour maintenir un angle de flamme optimal.
Q5 : Quel niveau d'humidité est requis ?
R : Maintenir 50±5% HR. Au-dessus de 70%, cela provoque des micro-fissures dues à la condensation de l'humidité.