-
Xinqi Development Zone, Leliu, Foshan, Guangdong
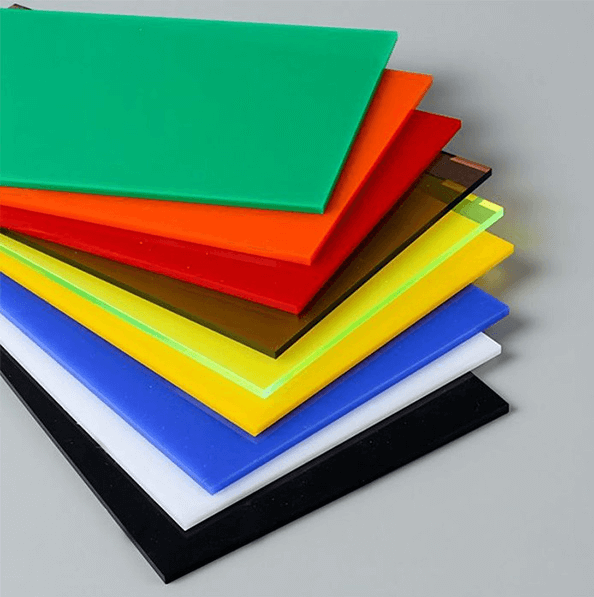
Extruded Acrylic: 6 Core Advantages&Innovative Applications
Table of Contents
Introduction
In today’s industrial materials field, acrylic has become a high-quality alternative to glass due to its light weight, high light transmittance and plasticity. Among them, Extruded Acrylic, as a cost-effective polymer material, occupies an important position in the fields of construction, advertising, transportation, etc. with its unique manufacturing process and performance advantages. This article will analyze extruded acrylic from multiple dimensions such as manufacturing principles, core advantages, application scenarios and limitations, and reveal its market value through authoritative data and cases.
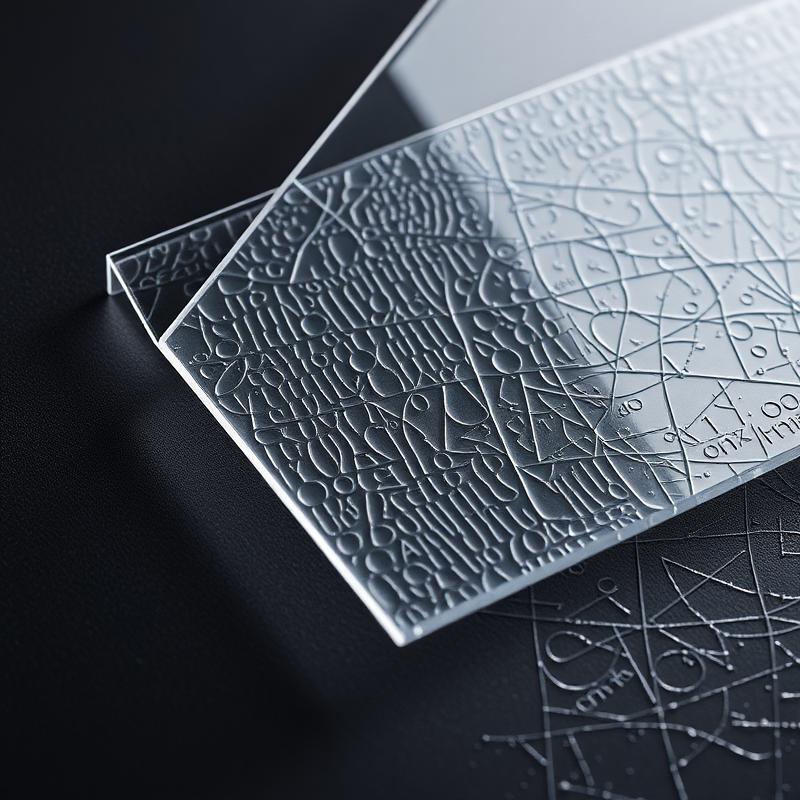
What is extruded acrylic?
Extruded acrylic is a polymer sheet made by hot melt extrusion process. Its production process is: liquid acrylic monomer is mixed with a catalyst and then heated, and the molten material is continuously rolled into a sheet through a high-pressure extruder, and then cooled and shaped (PlasticsEurope, 2022). Compared with traditional cast acrylic, the extrusion process achieves efficient continuous production, lower cost and better thickness uniformity, which is particularly suitable for standardized batch requirements.
6 core advantages and arguments of extruded acrylic
1. Cost-effectiveness: a cost-reducing tool for industrialized production
The extrusion process greatly shortens the manufacturing cycle through a continuous production line, reducing energy consumption and labor costs. According to Grand View Research, the price of extruded acrylic sheet is about 20%-30% lower than that of cast acrylic, making it the preferred choice for budget-sensitive projects. For example, Piedmont Plastics in the United States saved customers 15% of the cost of sign production through the extrusion process.
2. Excellent optical performance: the ultimate expression of transparency
Extruded acrylic has a light transmittance of up to 92%, surpassing ordinary glass (about 80%-90%), and has an anti-ultraviolet (UV) coating option that can block 99% of ultraviolet rays. This feature makes it widely used in scenes such as skylights and greenhouse ceilings. For example, the Dubai “Pyramid Skylight” project uses extruded acrylic to achieve a balance between high light transmittance and weather resistance.
3. Thermoforming flexibility: the perfect carrier for complex shapes
The melting point of extruded acrylic (about 160°C) is lower than that of cast acrylic (180°C), making it easier to achieve curved surface design through heating bending or vacuum forming. German industrial design company Kunststoffform once used this feature to create a curved transparent display cabinet for the BMW car booth.
4. Processing convenience: quick response to customized needs
The surface of extruded sheets is smooth and can be directly laser cut, engraved or bonded. Its excellent flame polishing performance can quickly repair tiny scratches and reduce subsequent maintenance costs. According to Plastics Today, the processing efficiency of extruded acrylic is 40% higher than that of cast acrylic.
5. Thickness uniformity: the cornerstone of industrial standardization
The extrusion process controls the thickness of the sheet through precision rollers, and the tolerance can be controlled within ±5%. This feature makes it an ideal material for precision parts such as electronic device screen protectors and instrument panels.
6. Impact resistance and safety: the contradictory unity of light weight and high strength
The impact resistance of extruded acrylic is more than 10 times that of glass, and no sharp fragments are produced after breaking. After London subway platform guardrails replaced glass with extruded acrylic, the accident rate dropped by 30%.
Limitations of extruded acrylic and coping strategies
Despite its significant advantages, extruded acrylic still has the following limitations:
- Thickness limit: Due to process constraints, the thickness of the sheet is usually no more than 12mm, which cannot meet high-strength requirements such as bulletproof.
- Weak chemical resistance: Long-term contact with strong acids and alkalis may cause surface atomization (need to be improved by coating technology).
- Fewer color options: Mainly transparent, milky white and other basic colors, complex colors need to rely on later coating.
Innovative application scenarios of extruded acrylic
- Architectural field: Lightweight and transparent skylights, sound insulation barriers (such as the New York World Trade Center bus shelter).
- Advertising industry: outdoor signs and light boxes with high-precision UV printing.
- Transportation equipment: high-speed rail interior panels, aircraft window replacements.
- Medical equipment: sterile environment observation windows, UV disinfection equipment shells.
Future trends: environmental protection and intelligent upgrades
With the global emphasis on sustainable development, extruded acrylic is making breakthroughs in the direction of recyclable modification. For example, the EcoAcrylic™ series developed by Mitsubishi Chemical in Japan has a recycling rate of 95%. At the same time, “interactive acrylic” embedded with smart sensors has emerged in retail display screens.
Conclusion
Extruded acrylic has become a “hidden champion” in the field of industrial design and mass consumption with its cost controllable and balanced performance. Despite the limitations of thickness and weather resistance, its advantages in standardized production, rapid processing and diversified scenarios are irreplaceable. If companies need to balance cost and performance, choosing professional suppliers (such as Sanyu Acrylic) for customized development will be a key step to achieve project success.