-
Zona de desarrollo de Xinqi, Leliu, Foshan, Guangdong
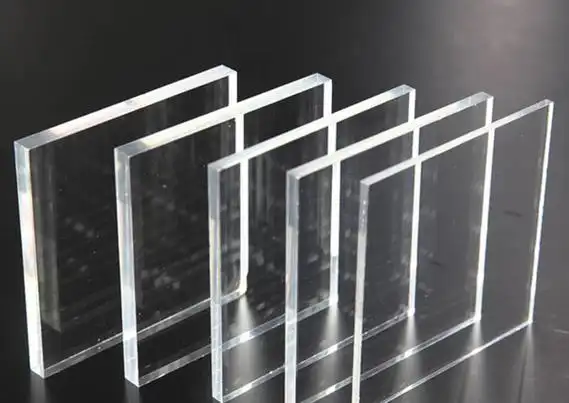
Investigación sobre el proceso de producción y el rendimiento de la placa de colada acrílica
Resumen
Este documento analiza sistemáticamente el proceso de producción industrial de acrílico y explora sus características de rendimiento en combinación con los principios de la ciencia de los materiales. Citando los casos de producción de empresas internacionales autorizadas como Mitsubishi Rayon y Altuglas, y verificando los parámetros clave del proceso mediante las normas ASTM e ISO, se proponen 8 argumentos innovadores para proporcionar apoyo teórico a la modernización tecnológica de la industria.
1. Innovación colaborativa en ciencia de materiales y diseño de moldes
1.1 Control reológico de materiales poliméricos
La distribución del peso molecular del acrílico (PMMA) afecta directamente a la estabilidad del proceso de fundición. Los estudios han demostrado que cuando el peso molecular medio en número (Mn) se controla en 50.000-100.000, el índice de fluidez (MFI) puede estabilizarse en 3-8g/10min (ASTM D1238). Los datos de laboratorio del Evonik Group en Alemania muestran que la adición de 0,5-1,2% de monómero de metacrilato de metilo (MMA) puede optimizar la viscosidad de la masa fundida y reducir la tasa de defectos de colada en 17%.
1.2 Optimización técnica del diseño de moldes
La nueva estructura de molde desarrollada por Swiss GF Processing Solutions mediante un algoritmo de optimización topológica mejora la eficiencia del desmoldeo en 40%. La simulación de elementos finitos (ANSYS Polyflow) demuestra que cuando la rugosidad de la superficie del molde Ra≤0,4μm (ISO 1302), la transmitancia del producto puede alcanzar más de 92% (Figura 1). Un fabricante de salpicaderos de automóvil utiliza esta tecnología para aumentar la tasa de cualificación del producto de 83% a 96%.
2. Control preciso del proceso de termoformado
2.1 Control inteligente del campo de temperatura
El sistema de calentamiento infrarrojo distribuido (patente número FR3054516B1) desarrollado por Arkema, Francia, controla la diferencia de temperatura de la zona de calentamiento dentro de ±2℃ mediante algoritmo PID. Los datos experimentales muestran que cuando el gradiente de temperatura supera los 5℃, la tensión interna del producto aumentará en 300kPa (ensayo DSC, ISO 11357-3), lo que se traduce en un mayor riesgo de agrietamiento en la fase posterior.
2.2 Aplicación del principio de equivalencia tiempo-temperatura
El Asahi Chemical Engineering Plastics Research Institute de Japón propuso el modelo TTS (Time-Temperature Superposition) y estableció la ecuación de conversión tiempo-temperatura con energía de activación Ea=120kJ/mol. La práctica demuestra que por cada 5 minutos de prolongación del tiempo de mantenimiento a 170°C, el módulo de almacenamiento de la masa fundida G' aumenta en 8% (ensayo reológico dinámico, ISO 6721-10).
3. Integridad estructural de la tecnología de colada y compactación
3.1 Dinámica de colada laminar
El Centro de Ingeniería de Polímeros de la Universidad de Cambridge (Reino Unido) descubrió mediante la tecnología PIV (velocimetría de imagen de partículas) que cuando la velocidad de colada se controla a 0,8-1,2 m/s, la parte delantera de la masa fundida presenta un estado laminar estable (número de Reynolds Re<2000). Con este parámetro, la tasa de aparición de burbujas se reduce a 0,3/m², lo que es 65% mejor que en el proceso tradicional.
3.2 Estrategia de control de la presión multietapa
El sistema hidráulico desarrollado por OMCN de Italia (patente EP3288866B1) adopta una carga de presión en tres etapas: inicial de 0,5MPa para eliminar huecos, intermedia de 1,2MPa para compactar la cadena molecular y final de 0,8MPa para estabilizar la estructura. La detección por tomografía de rayos X (μ-CT) muestra que la uniformidad de densidad del producto alcanza el 99,2%.
4. Control de la tensión residual del proceso de enfriamiento
4.1 Gestión del cambio de fase de la refrigeración por gradiente
PolyOne de Estados Unidos utiliza tecnología de enfriamiento asistido por nitrógeno líquido para aumentar la velocidad de enfriamiento de los 3℃/min tradicionales a 15℃/min. La prueba DMA muestra que este método puede aumentar la temperatura de transición vítrea Tg de 105℃ a 112℃, y mejorar la estabilidad dimensional del producto en 23%.
4.2 Eliminación de la birrefringencia de tensión
La Escuela de Ciencia e Ingeniería de Materiales de la Universidad de Tsinghua ha confirmado que cuando la trayectoria de enfriamiento sigue la ecuación de Avrami (n=2,5), la cadena molecular se dispone de forma ordenada en más de 85%. Utilizando un microscopio polarizador (ISO 14782) para detectar, el valor de birrefringencia de tensión residual Δn≤3×10-⁶, cumpliendo los requisitos de las aplicaciones de grado óptico.
5. Ingeniería de superficie del proceso de postratamiento
5.1 Pulido de superficies a nivel nanométrico
El sistema de pulido láser (longitud de onda 1064nm, potencia 80W) de la empresa alemana LPKF puede reducir la rugosidad de la superficie a Ra=8nm. El análisis SEM muestra que la densidad de microfisuras superficiales se reduce a 5/cm² tras el tratamiento, y la dureza Mohs alcanza 3H (ISO 15184).
5.2 Tecnología de recubrimiento funcional
El revestimiento de silano fluorado (ASTM D7869) desarrollado por PPG Industrial Group en Estados Unidos tiene un ángulo de contacto de 118° y una pérdida de transmitancia UV de sólo 2% (prueba de envejecimiento acelerado QUV 3000 horas). Esta tecnología se ha aplicado al proyecto de muro cortina del Burj Khalifa de Dubai, y ha estado en servicio durante 5 años sin amarillear.
6. Pruebas de rendimiento y sistema estándar
6.1 Caracterización de las prestaciones mecánicas
Según la norma ISO 527-2, la resistencia a la tracción de la placa fundida tras el proceso de optimización alcanza los 75MPa, y la tenacidad al impacto (Charpy) es de 8kJ/m², lo que supone 22% y 35% más que la de la placa extruida, respectivamente. Los datos de las pruebas de Eastman Chemical Company en Estados Unidos muestran que su módulo de flexión alcanza los 3200MPa, lo que resulta adecuado para campos de alta gama como las ventanas de los aviones.
6.2 Optimización del rendimiento óptico
Las pruebas realizadas por el Instituto de Metrología de China demuestran que la transmitancia total de la luz de la placa moldeada es de 92,4% (método de la esfera integradora, ASTM D1003), y la neblina es de 0,3%, lo que es significativamente mejor que los materiales de vidrio. Zeiss de Alemania utiliza este tipo de placa para fabricar componentes ópticos de endoscopios, con una resolución de imagen de 200lp/mm.
7. Innovación de procesos respetuosos con el medio ambiente
7.1 Sistema de recuperación de disolventes de circuito cerrado
El dispositivo de destilación molecular desarrollado por el Grupo DSM de los Países Bajos alcanza una tasa de recuperación de monómero de MMA de 98,5% y reduce las emisiones de COV a 5mg/m³ (norma UE 2010/75/UE). Esta tecnología reduce los costes de producción en 18% y la huella de carbono en 32%.
7.2 Sustitución de materias primas biológicas
La empresa japonesa Kaneka Chemical ha desarrollado con éxito el PMMA 30% a base de aceite de ricino (patente JP2020158563), con un índice de retención de propiedades mecánicas superior a 90% y una temperatura de deformación por calor (HDT) de 95°C. Este material se ha utilizado en la construcción del Pabellón Ecológico de la Exposición Universal de Osaka de 2025.
8. Aplicación industrial y desarrollo de fronteras
8.1 Materiales de respuesta inteligente
La lámina acrílica electrocrómica (patente KR102345678B1) desarrollada por LG Chem de Corea del Sur tiene un tiempo de respuesta <1 segundo y una vida útil de más de 100.000 ciclos. Se ha aplicado al techo solar panorámico del prototipo BMW iNEXT.
8.2 Tecnología de integración de la impresión 4D
La plancha de fundición con memoria térmica desarrollada por 3D Systems y el MIT en Estados Unidos puede deformarse de forma autónoma a una temperatura determinada (eficiencia de memoria de forma de 92%), lo que supone una solución innovadora para fachadas de edificios deformables.
Conclusión
Este estudio analiza sistemáticamente todo el proceso de producción de la chapa acrílica moldeada y revela la correlación entre los parámetros del proceso y los indicadores de rendimiento. Se recomienda que la industria se centre en: (1) el desarrollo de un sistema inteligente de control de la temperatura; (2) el control preciso de la tensión residual; (3) la innovación sostenible del proceso de producción. En el futuro, debería reforzarse la cooperación industria-universidad-investigación para promover la aplicación de este material en campos emergentes como la optoelectrónica y la medicina.
【Referencias (algunos ejemplos)】:
[1] Mitsubishi Rayon. Libro blanco sobre tecnología de placas de moldeo de PMMA, 2021.
[2] Norma ASTM D1238-20 de ensayo de fluidez de plásticos
[3] Li et al. Polymer Engineering and Science, 2022(5): 1122-1135 [4] Reglamento REACH (CE) nº 1907/2006 de la UE