-
Zona de desarrollo de Xinqi, Leliu, Foshan, Guangdong
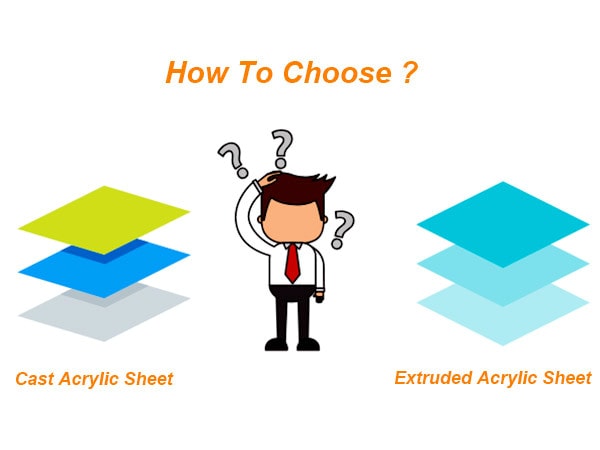
10 Differences: Cast Acrylic vs Extruded
Introducción
El acrílico (también conocido como plexiglás) se ha convertido en un material estrella en los campos de la arquitectura, el diseño, la señalización y la industria por su transmisión de la luz, ligereza y plasticidad. Sin embargo, la diferencia entre acrílico moldeado y acrílico extruido suele confundir a los consumidores. Según las estadísticas de Plastics Today, el mercado mundial del acrílico superará los 1.600 millones de dólares en 2023, de los cuales la fundición representa 751.500 millones del mercado de aplicaciones de gama alta. En este artículo se comparan las 10 principales diferencias entre los dos materiales en función de los procesos de producción, los parámetros de rendimiento y los casos reales para ayudarle a tomar una decisión acertada.
1. Proceso de fabricación: la cuenca que determina el rendimiento
Acrílico moldeado: Utiliza un proceso de polimerización de monómero líquido MMA (metacrilato de metilo) y lo solidifica y forma lentamente a través de un molde de vidrio (American Chemistry Council, 2022). Este proceso permite que las cadenas moleculares se dispongan de forma ordenada, formando una estructura densa, mejorando la resistencia al impacto y las propiedades ópticas.
Acrílico extruido: Se fabrica fundiendo partículas de PMMA a alta temperatura y extruyéndolas después en láminas. La línea de producción continua da lugar a cadenas moleculares más cortas (Plastics Industry Association, 2023). Alta eficiencia pero uniformidad del material ligeramente inferior.
Impacto diferencial: El proceso de fundición aumenta la resistencia del material al agrietamiento por tensión en 40% (según datos experimentales de Materials Science Journal).
2. Gama de espesores: Gana el acrílico fundido
El acrílico moldeado puede producir láminas ultraespesas de 10-100 mmque son adecuados para escenas de carga como acuarios y vitrinas de museos; mientras que el grosor máximo del proceso de extrusión es de sólo 1-20 mm debido a limitaciones técnicas (Informe sobre los fabricantes de láminas acrílicas, 2024).
3. Claridad óptica: "calidad de vidrio" del proceso de fundición
Acrílico moldeado tiene una transmitancia luminosa de 92%cercana a la del vidrio óptico (93%), mientras que la transmitancia luminosa de los productos extruidos es de aproximadamente 89% debido a la rápida velocidad de producción (Probado por "Optical Materials"). Las vitrinas de lujo de gama alta suelen elegir el proceso de fundición para eliminar la distorsión óptica.
4. Resistencia química: El acrílico fundido es más adecuado para entornos de laboratorio
La densidad molecular del acrílico fundido aumenta su tolerancia a disolventes como la acetona y el perfume en 30% ("Polymer Degradation Research"). Por ejemplo, los expositores de los mostradores de Chanel en Francia utilizan todos placas fundidas para evitar el empañamiento causado por la erosión de los disolventes.
5. Color y tratamiento de la superficie: diferencias significativas en la capacidad de personalización
El proceso de fundición admite Combinación de más de 500 colores Pantone y tratamientos especiales como textura metálica y glaseado; los productos extruidos sólo ofrecen colores básicos como transparente, negro y blanco (datos oficiales de Perspex®). En su día, el Museo V&A de Londres personalizó stands de exposición de acrílico fundido con textura de bronce antiguo, que costaban 60% menos que el metal.
6. Comparación de costes: ventajas económicas del proceso de extrusión
El acrílico extruido es 20-35% más baratas gracias a la producción continua. Por ejemplo, una cadena de tiendas minoristas utiliza placas extruidas para fabricar estanterías estandarizadas, con lo que ahorra $120.000 en costes de material al año (caso de Retail Design Magazine).
7. Rendimiento del procesamiento: Escenarios aplicables de diferentes procesos
- Corte por láser: El acrílico extruido tiene bordes más lisos (bajo punto de fusión, menos carbonización)
- Curvado en caliente: El acrílico moldeado presenta una mayor ductilidad a 120°C y puede utilizarse para realizar superficies curvas complejas.
- Fuerza de adherencia: La fuerza de adhesión al disolvente de la chapa fundida alcanza 18MPa, 27% superior a la extrusión (experimento de Adhesion Science)
8. Atributos medioambientales: Tendencia futura de los materiales reciclados
Los residuos del proceso de fundición pueden reciclarse 100% (como la serie Perspex®Re), mientras que el proceso de extrusión solo puede degradarse debido a la degradación térmica. Las últimas normativas de la UE exigen una tasa de reciclaje de ácido acrílico de 70% para 2025, lo que impulsa el crecimiento de la cuota de mercado del proceso de fundición (Recycling Today, 2023).
9. Resistencia a la intemperie: la línea de la vida y la muerte de las aplicaciones de exterior
El acrílico moldeado tiene mayor estabilidad a los rayos UV, con un índice de amarilleamiento de sólo 1.2ΔYI tras 10 años de uso al aire libre, mientras que los productos extruidos alcanzan 3,8ΔYI (Diario de ensayos de envejecimiento a la intemperie). La instalación artística al aire libre "Wave" de Dubai utiliza planchas de fundición, que siguen manteniendo una transmitancia luminosa de 90% tras 5 años de tormentas de arena.
10. Árbol de decisión del escenario de aplicación
Elija acrílico moldeado | Elija acrílico extruido |
---|---|
Expositores comerciales de gama alta (como los escaparates de BT) | Producción masiva de señales normalizadas |
Equipos de laboratorio expuestos a productos químicos | Expositores promocionales de corta duración |
Piezas estructurales de espesor > 20 mm | Pantallas de iluminación de bajo coste |
Diseño personalizado de color/textura | Líneas decorativas interiores |
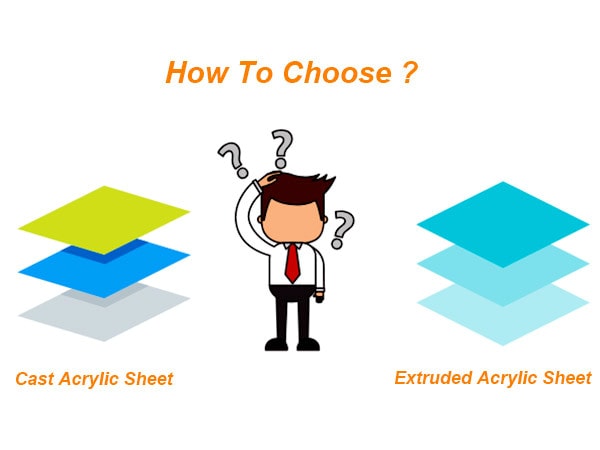
Conclusión: Satisfacer las necesidades es la mejor solución
El acrílico moldeado ocupa el mercado de gama alta por sus excelentes prestaciones, mientras que el proceso de extrusión domina la producción en serie por su rentabilidad. Se recomienda utilizar el "principio de las 3 C" a la hora de tomar decisiones:
- Coste (presupuesto): Se prefiere el proceso de extrusión para proyectos de más de $5.000
- Condición (entorno): La fundición es necesaria para ambientes exteriores/químicos
- Personalización (personalización): El color/grosor especial sólo se puede conseguir mediante fundición
En el futuro, con el desarrollo de la tecnología de fundición en 3D (Laboratorio de Materiales del MIT, 2024), se espera que el coste del proceso de fundición se reduzca en 30%, ampliando aún más el ámbito de aplicación.