-
Zona de desarrollo de Xinqi, Leliu, Foshan, Guangdong
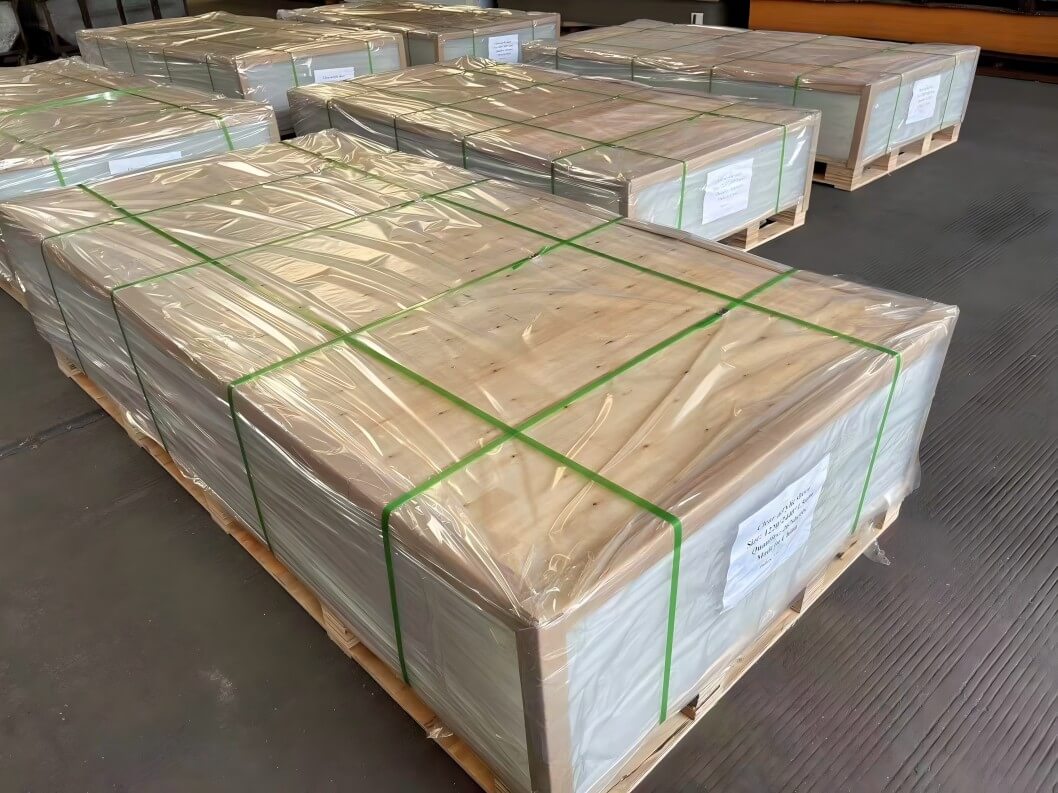
¿Cómo influyen el grosor y la densidad en los costes de transporte de las planchas acrílicas?
Índice
Introducción
Láminas acrílicas se han convertido en el material preferido de sectores como la publicidad, la construcción y el mobiliario debido a su elevada transmisión de la luz, su resistencia a la intemperie y su facilidad de procesamiento. Sin embargo, sus costes de transporte suelen fluctuar significativamente debido a las diferencias de grosor y densidad. Los estudios han demostrado que los costes de transporte pueden suponer el 15%-30% del coste total del material. Este artículo analiza cómo afectan el grosor y la densidad de las planchas acrílicas a los costes de transporte desde cinco dimensiones: cálculo del peso, eficacia de la carga, refuerzo del embalaje, riesgo de daños y estrategia de transporte, en combinación con datos y casos fidedignos, para ofrecer a las empresas una solución científica de reducción de costes.
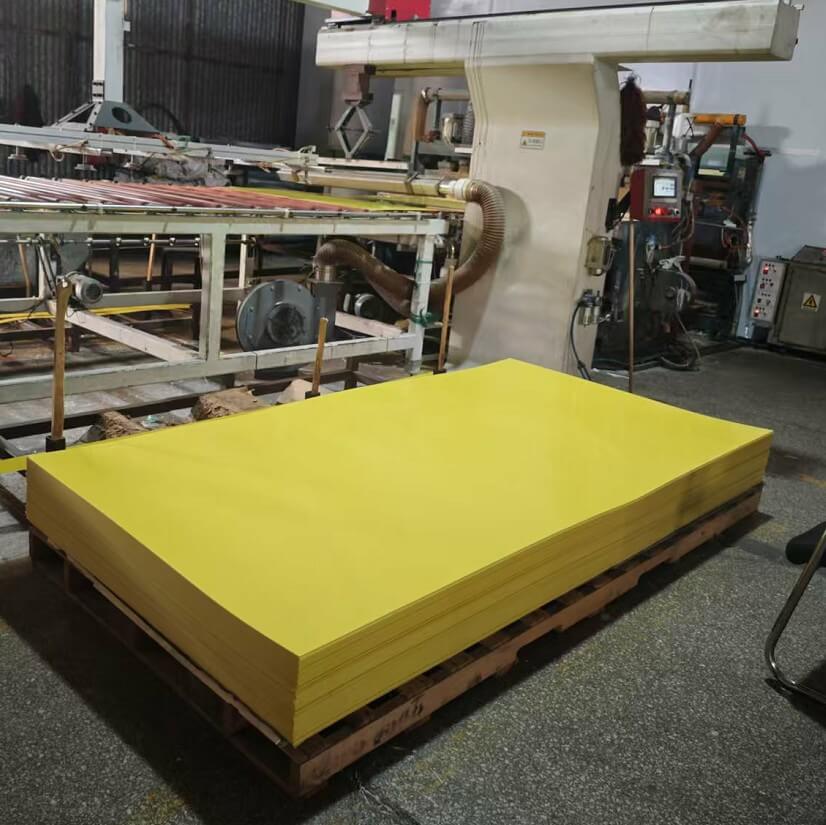
Cálculo de peso y flete: "Costes ocultos" con densidad constante
La densidad de las láminas acrílicas se mantiene estable en 1,19~1,20g/cm³ , pero el grosor afecta directamente al peso de una sola lámina. Por ejemplo, una lámina de 3 mm de grosor (1220 mm×2440 mm) pesa unos 8,7 kg, mientras que una de 10 mm del mismo tamaño pesa 29 kg, lo que supone un aumento de 233%. En un modelo logístico que cobra por peso (como el transporte aéreo o el transporte terrestre LTL), el flete aumenta linealmente con el grosor. Sobre la base del precio unitario de transporte terrestre de FedEx de $0,5/kg, el coste de flete de una sola plancha de 10 mm es $10,15 superior al de una plancha de 3 mm, y la diferencia de coste puede alcanzar decenas de miles de dólares cuando se transporta en grandes cantidades (referencia del caso: Calculadora de carga de FedEx).
Eficacia de carga: Cómo el grosor "comprime" el beneficio espacial
El coste del transporte no sólo está relacionado con el peso, sino también con la utilización del espacio. Las planchas acrílicas más finas pueden apilarse en varias capas para aprovechar al máximo el volumen del contenedor. Tomando como ejemplo un contenedor estándar de 40 pies (volumen 67 m³), las planchas de 3 mm pueden cargar 1.500 planchas, mientras que las de 10 mm sólo pueden alojar 450 planchas, lo que reduce la utilización del espacio en 70%. Si el precio unitario del flete marítimo es de US$2.000/contenedor, el coste unitario de transporte de las chapas de 10 mm asciende a US$4,44/hoja, lo que supone 3,3 veces el de las chapas de 3 mm (US$1,33/hoja). Las empresas tienen que equilibrar el volumen de carga y el coste de peso mediante la selección del espesor.
Necesidades de refuerzo de los envases: la trampa de la "tasa de protección" de las láminas gruesas
Debido al gran peso de una sola pieza, las planchas gruesas son propensas a sufrir daños en las esquinas a causa de las vibraciones durante el transporte. Para reducir los riesgos, las empresas de logística suelen exigir un soporte adicional de madera o espuma antichoque, lo que aumenta los costes de embalaje en 20%-40%. Según datos de la American Packaging Association, el coste de reforzar las planchas de 10 mm es de aproximadamente $8 por plancha, mientras que las de 3 mm sólo cuestan $3. Además, las planchas con sobrepeso pueden dar lugar a un recargo por "carga no estándar", lo que incrementa aún más los costes.
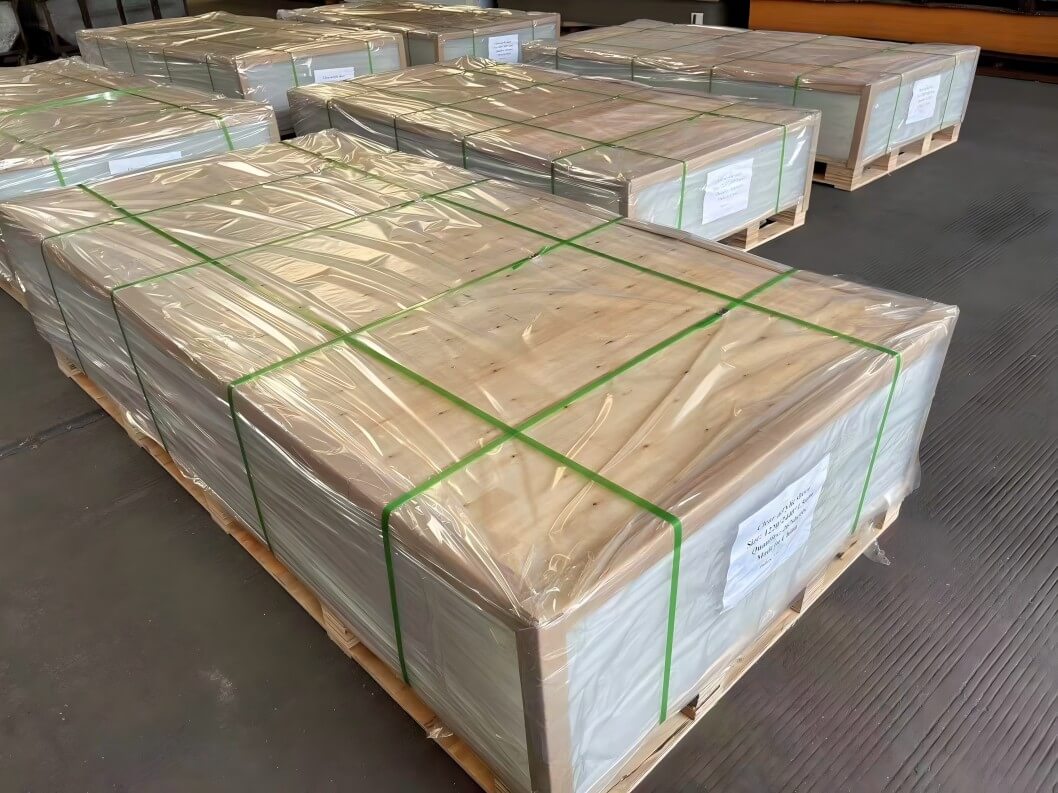
Índice de daños y coste del riesgo: la "ventaja de la resistencia a los daños" de las chapas gruesas
Aunque las planchas gruesas tienen unos costes de transporte elevados, su resistencia a los impactos puede reducir el riesgo de daños. Los experimentos demuestran que el índice de daños de las planchas de 3 mm en el transporte de larga distancia es de unos 5%, mientras que el de las planchas de 10 mm es inferior a 1%. Si se calcula el valor de cada lámina en $200, el transporte de 1.000 láminas de 3 mm puede suponer una pérdida por siniestro de $10.000, mientras que las láminas gruesas sólo cuestan $2.000. Las empresas tienen que evaluar los riesgos en función de la distancia de transporte: el transporte a corta distancia puede preferir planchas gruesas, mientras que el transporte a larga distancia requiere un coste y un índice de rotura exhaustivos para seleccionar espesores moderados.
Optimización de la estrategia de transporte: Modelo de decisión multidimensional basado en datos
- Transporte marítimo Prioridad: Las planchas gruesas son adecuadas para el transporte marítimo por su gran peso pero durabilidad. Tomando como ejemplo la ruta entre China y la costa oeste de Estados Unidos, el coste del transporte marítimo es solo 1/6 del del transporte aéreo (Fuente: Informe sobre logística del Banco Mundial).
- Carga mixta: Combine pedidos de distintos grosores para el transporte y utilice placas finas para rellenar los huecos del contenedor.
- Almacenes regionales: Establecer almacenes cerca del mercado objetivo para reducir la frecuencia del transporte de larga distancia. Por ejemplo, IKEA redujo el coste de transporte de platos en 12% mediante almacenes globales.
PREGUNTAS FRECUENTES
¿Cómo optimizar la estrategia de transporte de placas acrílicas?
① Dar prioridad al transporte marítimo; ② Mezclar pedidos de distintos grosores; ③ Establecer almacenes para mercados objetivo, como IKEA reduciendo costes por 12% a través de almacenes.
¿Qué es más adecuado para transportar tableros acrílicos, el transporte marítimo o el aéreo?
Los tableros gruesos son adecuados para el transporte marítimo (el coste es 1/6 del transporte aéreo), y los tableros finos o los pedidos urgentes pueden transportarse por avión. Hay que equilibrar el peso y la puntualidad.
¿Cómo calcular los gastos de envío de una sola lámina acrílica?
Fórmula: Flete de una hoja = (peso × precio unitario) + tasa de embalaje + recargo. Por ejemplo, el coste del flete marítimo de una hoja de 10 mm es de aproximadamente US$4,44 por hoja (embalaje incluido).
¿Existe un grosor recomendado con el "mejor rendimiento de costes"?
Se requiere una evaluación exhaustiva de la distancia de transporte. Por ejemplo, se recomiendan 5-8 mm para el comercio de exportación, y 10 mm o más pueden seleccionarse para distancias cortas locales para reducir la tasa de rotura.
¿Es posible que la densidad cambie debido a los distintos procesos de producción?
El error de densidad de los fabricantes habituales es ≤0,01g/cm³ (según la norma Röhm), y la ligera diferencia no tiene ninguna repercusión real en el coste del transporte.
Conclusión
El coste de transporte de las placas acrílicas es el resultado del efecto combinado del grosor, la densidad, el embalaje, el riesgo y la estrategia logística. Las empresas necesitan establecer modelos de datos para cuantificar el "coste de enlace completo" de las placas de distintos grosores, y hacer elecciones flexibles en función de la distancia de transporte y el tamaño del pedido. Por ejemplo, para el comercio de exportación, pueden utilizarse placas de 5-8 mm para equilibrar la capacidad de carga y la resistencia a los daños, mientras que los pedidos locales pueden utilizar especificaciones superiores a 10 mm para reducir los costes de embalaje. Mediante una toma de decisiones científica, las empresas pueden reducir los costes de transporte en 10%-25%, garantizando al mismo tiempo la calidad de la entrega (Fuente: Investigación del MIT sobre gestión de la cadena de suministro).