-
Zona de desarrollo de Xinqi, Leliu, Foshan, Guangdong
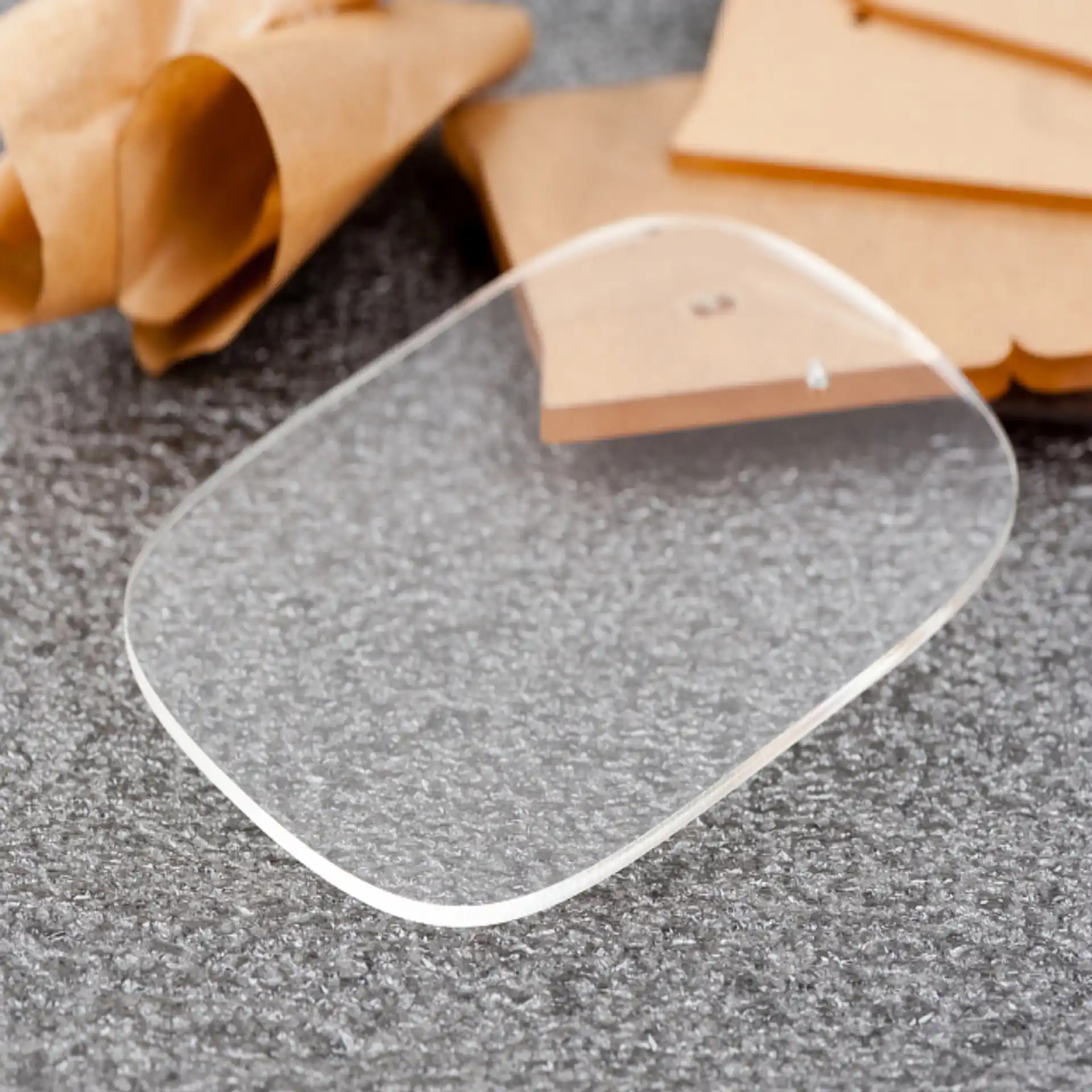
Logre bordes acrílicos como el vidrio con el pulido a la llama
En los campos de las pantallas de alta gama, la construcción de muros cortina y las instalaciones de arte, el acabado de los bordes de un tablero acrílico a menudo determina el valor final del producto. Cuando el pulido y el esmerilado tradicionales son difíciles de lograr bordes transparentes como el vidrio, tecnología de pulido a la llama destaca por su alta eficiencia y excelentes resultados: el operador barre el borde del acrílico con una pistola rociadora de llama, y el borde originalmente mate y áspero se vuelve instantáneamente tan transparente como el cristal. Detrás de este proceso mágico se encuentra la comprensión precisa de las propiedades del material y el control térmico.
1. La esencia técnica del pulido a la llama
El pulido a la llama es esencialmente una tecnología de remodelación por microfusión superficial. El acrílico (PMMA) es un material termoplástico. Cuando se calienta a unos 105 °C, alcanza el punto de reblandecimiento. En este momento, la capa molecular superficial fluye, pero la estructura general permanece sólida. El pulido a la llama aprovecha esta característica. Derrite los defectos finos de la superficie a una temperatura alta y corta, utiliza la tensión superficial para volver a nivelar el material y forma un borde ópticamente transparente después del enfriamiento.
En comparación con el pulido mecánico, el pulido a la llama tiene ventajas significativas para estructuras geométricas complejas. Ya sean las ranuras curvas de los caracteres de cristal publicitarios o la estructura de orificios internos de las esculturas con formas especiales, la llama puede llegar a los rincones muertos que son difíciles de manejar con las herramientas tradicionales. Los datos experimentales muestran que un operador profesional solo tarda entre 15 y 20 segundos en completar el pulido de los bordes de 1 metro de acrílico, lo que es más de 5 veces más eficiente que el pulido mecánico. Sin embargo, esta tecnología tiene requisitos básicos para el grosor del material. Solo las placas de más de 3 mm pueden soportar el choque térmico sin deformarse. Las placas delgadas requieren habilidades más avanzadas.
2. Selección de equipos y optimización de la llama
La calidad de la llama es el factor clave para el éxito del pulido:
- Pulidora de llama de hidrógeno y oxígeno: Produce gas mixto de hidrógeno y oxígeno a través de la electrólisis del agua, con una temperatura de combustión de aproximadamente 2800 °F. La llama es pura y no contiene partículas de carbono, lo que evita la contaminación de la superficie acrílica. Es la primera opción para el procesamiento de alta gama
- Pistola rociadora de propano: Tiene un bajo costo, pero debe ajustarse con precisión a una llama cónica azul (longitud 5-10 cm). La punta de la llama amarilla provocará la deposición de hollín
- Microantorcha de butano: Es adecuada para reparaciones en áreas pequeñas y es fácil de controlar
El mecanismo automático de rociado de llama desarrollado en la tecnología patentada (CN202311144808.2) realiza el ajuste en tiempo real de la intensidad de la llama a través de un sistema de suministro de gas de doble vía para garantizar un calentamiento uniforme de placas de diferentes grosores. La configuración de seguridad es igualmente importante. El área de trabajo debe estar equipada con un sistema de ventilación a prueba de explosiones, y el operador debe usar guantes de fibra de carbono resistentes al calor (nivel de protección ≥800 ℃) y una máscara a prueba de rayos UV.
3. Proceso de operación estandarizado
Pretratamiento del sustrato El borde acrílico después del corte debe pulirse inicialmente con papel de lija de grano 400 para eliminar las marcas de sierra, y luego pulirse finamente con papel de lija de agua de grano 800 o superior hasta que no haya grano evidente. Después de cada proceso, debe limpiarse con alcohol anhidro y un paño sin pelusa. Cualquier mancha de aceite o polvo formará defectos permanentes a altas temperaturas.
Tecnología de control térmico dinámico
- Mantener una distancia de 5-10 cm entre la pistola rociadora y la placa, y moverse a una velocidad uniforme de 10 cm/s
- Cada borde se trata durante no más de 1 segundo
- La placa gruesa adopta la estrategia de "quemado flash múltiple" (enfriamiento después de 30 segundos cada vez)
Observar el estado de fusión es el punto técnico central: Si aparece el reflejo del espejo en la superficie, retire inmediatamente la llama. Si se generan pequeñas burbujas o marcas blancas neblinosas, significa que está sobrecalentado. Para placas delgadas con un grosor de menos de 3 mm, se puede colocar una placa de cobre en la parte posterior para ayudar a disipar el calor.
4. Soluciones de pulido para estructuras especiales
Pulido de orificios internos (como estructuras de orificios con un diámetro de 16 mm y un grosor de pared de 2,5 mm) requiere métodos creativos:
- Convierta la micro pistola rociadora en una boquilla curva en forma de L
- Ajuste la intensidad de la llama a 1/3 del valor normal
- Utilice el funcionamiento intermitente de "quemado puntual de 0,5 segundos + rotación de la pieza de trabajo"
- Preincruste el varilla de núcleo de metal en el orificio para absorber el exceso de calor
Borde curvo El procesamiento requiere combinarse con equipos automatizados. El dispositivo de pulido de llama de desplazamiento descrito en la patente CN117584436B controla la trayectoria de la pistola rociadora a través de un sistema servo programable y gira sincrónicamente la pieza de trabajo para mantener el ángulo de pulido óptimo. Para placas súper grandes (>2 m), se recomienda utilizar un banco de trabajo de posicionamiento con una intercapa refrigerada por agua para evitar la acumulación de temperatura local.
5. Análisis y control de defectos de calidad
Los problemas comunes en el pulido a la llama son esencialmente el producto de la fuga térmica:
- Rizado de bordes: principalmente debido a la concentración de calor en el borde en ángulo recto de la placa gruesa, el achaflanado previo de 45° puede dispersar la tensión
- Manchas blancas atomizadas: la llama permanece demasiado tiempo, lo que provoca la degradación molecular, y debe pulirse ligeramente con papel de lija de grano 800 antes de volver a pulir
- Hoyos de burbujas: el contenido de humedad del material excede el estándar (debe ser <0.2%), y debe secarse a 80 ℃ durante 4 horas antes del procesamiento
Los factores ambientales a menudo se ignoran: Cuando la humedad>70%, el vapor de agua se condensa en la superficie de la placa fría, lo que provoca grietas en forma de estrella en la superficie pulida; Velocidad del viento>1m/s provoca un enfriamiento y una deformación desiguales. Se recomienda operar en un taller de temperatura y humedad constantes (temperatura 23 ± 2 ℃, humedad 50 ± 5%).
6. Evolución tecnológica y dirección de la innovación
Las tecnologías de vanguardia actuales se centran en control inteligente:
- El módulo de medición de temperatura infrarroja monitorea la temperatura de la superficie de la placa en tiempo real
- El sistema visual identifica automáticamente las características geométricas de los bordes
- Ajuste adaptativo de parámetros (como el sistema de enlace servo en la patente de Longnan Xintao Acrylic Technology)
Las máquinas de pulido de hidrógeno y oxígeno se están actualizando hacia fabricación ecológica. La nueva generación de equipos integra un sistema de circulación de aguas residuales, y la eficiencia de la electrólisis aumenta a 3,2 kWh/m³, que es un 40% más eficiente energéticamente que los equipos tradicionales. El proceso compuesto (como la asistencia líquida de pulido químico + llama) puede procesar placas ultradelgadas de 0,8 mm, lo que amplía los límites técnicos.
Comparación de datos de un fabricante de estantes de exhibición de alta gama: el pulido tradicional con ruedas de tela tarda 7 minutos por pieza, con una tasa de aprobación del 85%; después de la transformación integrada del sistema de pulido a la llama, el procesamiento de una sola pieza se reduce a 1,2 minutos y la tasa de aprobación salta al 98%.
Conclusión: La filosofía de la temperatura del arte de Seiko
El pulido a la llama transforma la energía térmica aparentemente destructiva en un medio para crear la perfección. La esencia de esta habilidad radica en el equilibrio preciso de calor y tiempo. Desde la agilidad de las pistolas rociadoras manuales hasta la precisión de los equipos automatizados, la evolución de la tecnología siempre ha girado en torno a un objetivo central: capturar el momento mágico del brillo congelado en el momento en que las moléculas de acrílico comienzan a fluir. Cuando el primer haz de luz penetra en el borde pulido sin obstáculos, se completa la sublimación de los productos industriales a las obras de arte ópticas.
Expansión de recursos autorizados:
- Asociación Internacional de Fabricantes de Acrílico – Estándares técnicos de materiales
- Informe de prueba de materiales SGS – Datos de meteorización de la superficie pulida
- Equipo alemán de pulido a la llama Roth – Soluciones de grado industrial
- Sociedad Estadounidense de Ingenieros de Plásticos – Libro blanco sobre tecnología de procesamiento de termoplásticos
PREGUNTAS FRECUENTESs
P1: ¿Qué tipo de llama es mejor para el pulido de acrílico?
R: La mezcla de hidrógeno y oxígeno crea llamas sin hollín, mientras que el propano requiere un ajuste preciso del cono azul para evitar depósitos de carbono.
P2: ¿Se pueden pulir a la llama las láminas acrílicas delgadas (<3 mm)?
R: Sí, utilizando un respaldo de disipador de calor de cobre e intervalos de calentamiento flash de 0,5 segundos para evitar que se deforme.
P3: ¿Por qué aparecen rayas blancas durante el pulido?
R: Causado por el sobrecalentamiento. Enfríe la lámina, lije ligeramente con papel de lija de grano 800 y vuelva a pulir a una temperatura más baja.
P4: ¿Cómo pulir los bordes acrílicos curvos de manera efectiva?
R: Utilice sistemas servo programables con soportes giratorios para piezas de trabajo para mantener el ángulo de llama óptimo.
P5: ¿Qué nivel de humedad se requiere?
R: Mantenga una HR de 50 ± 5%. Por encima del 70% provoca microfisuras por condensación de humedad.