-
Xinqi Development Zone, Leliu, Foshan, Guangdong
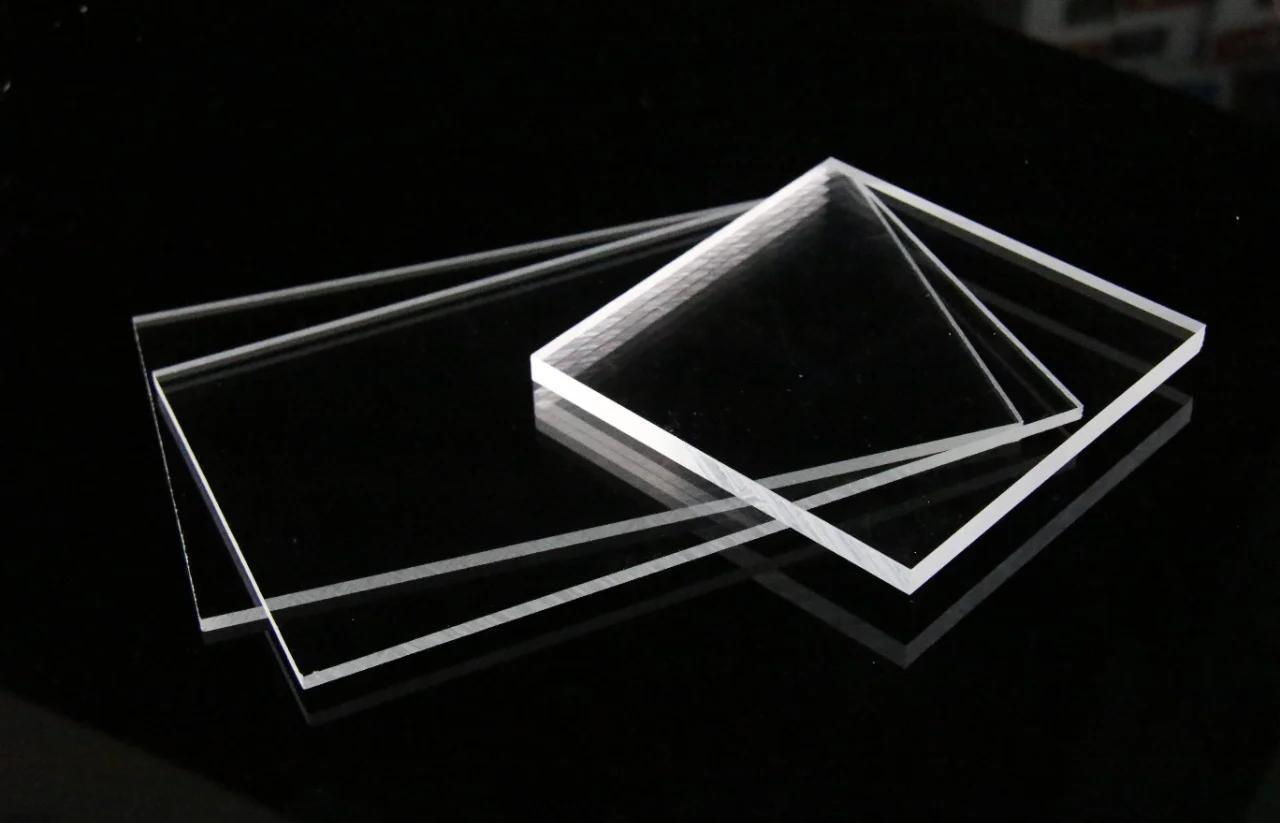
Ultra Clear Acrylic Sheets with Lifetime UV Protection
A piece of “sunscreen” plastic board is quietly occupying the global high-end architecture and outdoor advertising market, behind which is the 30-year offensive and defensive battle between material scientists and ultraviolet rays.
Sunlight is the “ultimate killer” of transparent Acrylplatten. Ordinary acrylic will show visible yellowing, reduced light transmittance and even surface cracking after only 1-2 years of outdoor exposure. The culprit of this phenomenon is ultraviolet rays, which only account for 5% of sunlight, but are enough to destroy the chemical bonds of polymer molecular chains.
When ultraviolet rays (especially the wavelength of 290-400nm) continuously irradiate the acrylic surface, oxygen molecules will be stimulated to produce active free radicals, triggering photooxidative degradation chain reaction. The breakage of molecular chains causes the material’s light transmittance to decrease, and the accumulation of carbonyl compounds appears as an annoying yellow.
1. Ultraviolet “photoaging” attack chain
The aging of ordinary acrylic boards under ultraviolet rays is not a linear process. Experiments show that the yellowing index can increase by 30% in the first 6 months, and the transmittance plummets from 92% to below 80%, which is direct evidence that ultraviolet rays destroy the covalent bonds inside the material. When microcracks appear on the surface of the material, the aging process will accelerate geometrically.
Traditional solutions such as adding organic UV absorbers (such as benzotriazoles) can delay yellowing in the short term, but the absorbers themselves will be exhausted within 2-3 years, and decompose faster in high temperature environments.
2. Molecular defense of anti-UV additives
The core breakthrough of modern anti-UV acrylic sheets lies in “ultraviolet light conversion technology”. By adding nano-scale inorganic UV shielding agents (such as titanium dioxide and zinc oxide), high-energy ultraviolet rays are converted into harmless heat energy. Top products such as the Tomson TC-1 series can block 99% of ultraviolet rays, and the transmittance remains at 91.5% after 15,000 hours of accelerated aging (equivalent to 15 years outdoors).
More cutting-edge technologies, such as Zhejiang Shenmei’s patented titanium dioxide-silicon dioxide composite sol (patent number CN118755129A), construct a silicon-oxygen network on the surface of titanium elements. It not only retains the UV shielding function of titanium dioxide, but also inhibits its photocatalytic activity, preventing the acrylic substrate from being degraded secondary.
3. Dual protection mechanism of nano coating
The single additive strategy is still limited, and industry-leading companies have turned to the “substrate + coating” synergistic protection system:
- Substrate layer: Polypropylene adipate and polymethyl methacrylate are used to form an interpenetrating network structure, and flexible polyester molecules are embedded in the gaps between PMMA chain segments, which not only maintains transparency but also improves toughness
- Beschichtung: Polyurethane substrate is grafted with titanium dioxide-silicon dioxide composite sol, and sprayed to form a 400-600μm protective film with a UV blocking rate of over 99.5%
This design requires ultraviolet rays to break through the chemical bond barrier of the coating before they can reach the substrate. Actual measurements show that the coated acrylic sheet is exposed to a hot and humid environment (temperature 60℃/humidity 90%) for 5 years, and the yellowing index increases by less than 1/10 of that of ordinary sheets.
4. Co-evolution of anti-yellowing and material toughness
Long-term UV resistance must solve the problem of material embrittlement. The TC-1 formula developed by Tomson Technology introduces flexible segments into the substrate, making the impact resistance of the sheet 20 times that of ordinary glass. A 3mm thick plate can withstand a full-strength hammering by an adult without breaking, and will not produce sharp fragments after breaking.
The stability of mechanical properties directly determines the outdoor service life. The acrylic substrate toughened by polypropylene adipate has a tensile strength retention rate of over 95% in the temperature difference cycle test from -30℃ to 80℃, which completely solves the pain point of traditional acrylic embrittlement in winter.
5. Practical verification of economic efficiency and environmental adaptability
The case of the Hangzhou Asian Games Rock Climbing Center using UV-resistant acrylic curtain walls is very convincing:
- 92% Lichtdurchlässigkeit 3.2m x 11.5m super-large panels to build all-weather skylights
- Combined with nano self-cleaning coating to reduce the impact of dust accumulation on light transmittance
- It is expected that 30-year service life will save 12 million yuan in maintenance costs
Different application scenarios require differentiated protection strategies: Clean room anti-static panels (such as yellow UV-resistant acrylic) prevent static electricity from adsorbing dust through surface resistance of 106-108Ω, while filtering out ultraviolet rays; Building Integrated Photovoltaic (BIPV) components need to take into account both high light transmittance and ultraviolet shielding to ensure that the lower photovoltaic cells are not affected by thermal effects.
6. Standard Evolution and Future Material Atlas
GB/T 44551-2024 “Determination Method for Weathering Resistance of Optical Functional Films” implemented in 2024 will include the solvent induction method into the national standard for the first time. This method accelerates aging by simulating environmental corrosive media, and predicts the actual life of the material more accurately than the traditional xenon lamp test.
The next generation of technology has begun to show its edge:
- Self-healing coating: microencapsulated UV absorber, released with the gradient of light intensity
- Smart dimming acrylic: electrochromic material and anti-UV layer composite, dynamic light transmittance adjustment range of 40%-80%
- Bio-based anti-aging agent: UV absorbing components extracted from plant polyphenols, biodegradable
From the giant curtain wall of the Hangzhou Asian Games venue to the anti-static compartment of the semiconductor factory, the value chain of anti-UV acrylic board is still extending. Thomson Technology’s 250mm cast thick plate has been used in the lighting dome of the Antarctic research station. In the polar day environment where the ultraviolet intensity is doubled, it still maintains optical stability after the test of -60℃.
When choosing anti-yellowing acrylic plates, you need to look for three technical labels: 99% UV blocking rate, 15,000-hour aging certification report, and substrate-coating double protection structure. This set of golden parameters will determine whether your building will gradually fade into a specimen of the old times or continue to shine with the light of technology in the next thirty years.
FAQs
Q1: How fast does regular acrylic turn yellow outdoors?
A: Unprotected sheets show visible yellowing within 1-2 years, losing over 12% transparency.
Q2: What’s inside UV-resistant acrylic?
A: Nano TiO2/SiO2 composites convert UV to heat, blocking 99% rays without self-degradation.
Q3: How to verify 10-year anti-yellowing claims?
A: Demand 15,000-hour accelerated aging reports per GB/T 44551-2024 standard.
Q4: Can UV acrylic survive extreme cold?
A: Yes. Flexible polymer networks maintain 95% strength at -60°C (proven in Antarctic stations).
Q5: Why choose coated vs. bulk-modified acrylic?
A: Dual-layer protection extends service life 3X vs. additive-only sheets in humid climates.
Q6: Does anti-UV coating reduce clarity?
A: Premium coatings (<600nm) maintain 92% light transmission – higher than standard glass.