-
Xinqi Development Zone, Leliu, Foshan, Guangdong
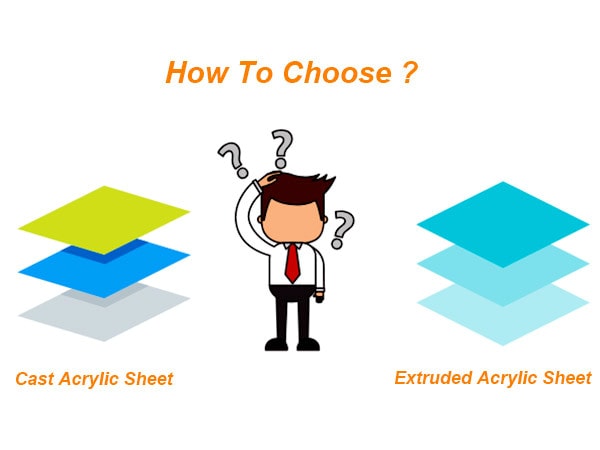
10 Differences: Cast Acrylic vs Extruded
Introduction
Acrylic (also known as plexiglass) has become a star material in the fields of architecture, design, signage and industry due to its light transmittance, light weight and plasticity. However, the difference between cast acrylic and extruded acrylic often confuses consumers. According to statistics from Plastics Today, the global acrylic market will exceed US$6 billion in 2023, of which casting accounts for 75% of the high-end application market. This article will compare the 10 core differences between the two materials based on production processes, performance parameters and actual cases to help you make an accurate choice.
1. Manufacturing process: the watershed that determines performance
Cast acrylic: It uses a monomer liquid MMA (methyl methacrylate) polymerization process and slowly solidifies and forms it through a glass mold (American Chemistry Council, 2022). This process allows the molecular chains to be arranged in an orderly manner, forming a dense structure, improving impact resistance and optical properties.
Extruded acrylic: It is made by melting PMMA particles at high temperature and then extruding them into sheets. The continuous production line results in shorter molecular chains (Plastics Industry Association, 2023). High efficiency but slightly inferior material uniformity.
Differential impact: The casting process increases the material’s resistance to stress cracking by 40% (according to experimental data from Materials Science Journal).
2. Thickness range: Cast acrylic wins
Cast acrylic can produce ultra-thick sheets of 10-100mm, which are suitable for load-bearing scenes such as aquariums and museum display cabinets; while the maximum thickness of the extrusion process is only 1-20mm due to technical limitations (Acrylic Sheet Manufacturer Report, 2024).
3. Optical clarity: “glass-grade” performance of the casting process
Cast acrylic has a light transmittance of 92%, close to optical glass (93%), while the light transmittance of extruded products is about 89% due to the fast production speed (Tested by “Optical Materials”). High-end luxury display cabinets often choose the casting process to eliminate optical distortion.
4. Chemical resistance: Cast acrylic is more suitable for laboratory environments
The molecular density of cast acrylic increases its tolerance to solvents such as acetone and perfume by 30% (“Polymer Degradation Research”). For example, the display stands of Chanel counters in France all use cast plates to avoid fogging caused by solvent erosion.
5. Color and surface treatment: significant differences in customization capabilities
The casting process supports 500+ Pantone color matching and special treatments such as metal texture and frosting; extruded products only provide basic colors such as transparent, black and white (Perspex® official data). The V&A Museum in London once customized cast acrylic antique bronze texture exhibition stands, which cost 60% less than metal.
6. Cost comparison: economic advantages of extrusion process
Extruded acrylic is 20-35% cheaper due to continuous production. For example, a chain retail store uses extruded plates to make standardized shelves, saving $120,000 in material costs annually (Retail Design Magazine case).
7. Processing performance: Applicable scenarios of different processes
- Laser cutting: Extruded acrylic has smoother edges (low melting point, less carbonization)
- Hot bending: Cast acrylic has better ductility at 120°C and can be used to make complex curved surfaces
- Bond strength: Solvent bonding strength of cast sheet reaches 18MPa, 27% higher than extrusion (Adhesion Science experiment)
8. Environmental attributes: Future trend of recycled materials
Casting process waste can be 100% recycled (such as Perspex®Re series), while extrusion process can only be downgraded due to thermal degradation. The latest EU regulations require a 70% acrylic acid recycling rate by 2025, driving the growth of the casting process market share (Recycling Today, 2023).
9. Weather resistance: the life and death line of outdoor applications
Cast acrylic has better UV stability, with a yellowing index of only 1.2ΔYI after 10 years of outdoor use, while extruded products reach 3.8ΔYI (Weathering Testing Journal). Dubai’s outdoor art installation “Wave” uses cast sheets, which still maintains a 90% light transmittance after 5 years of sandstorms.
10. Application scenario decision tree
Choose cast acrylic | Choose extruded acrylic |
---|---|
High-end commercial displays (such as LV windows) | Mass production of standardized signs |
Laboratory equipment exposed to chemicals | Short-term promotional display racks |
Structural parts with thickness > 20mm | Low-cost lighting lampshades |
Customized color/texture design | Interior decorative lines |
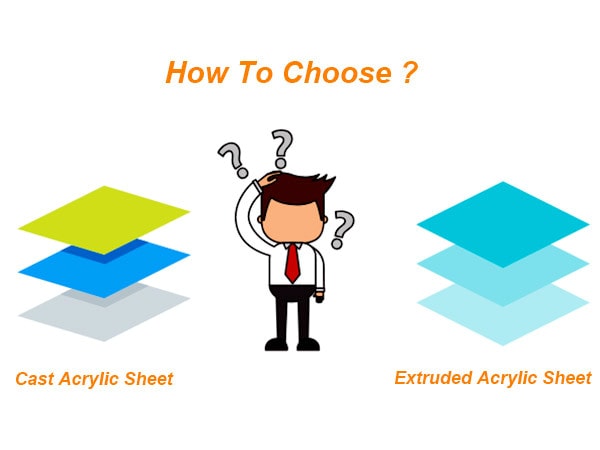
Conclusion: Matching needs is the best solution
Cast acrylic occupies the high-end market with its excellent performance, while the extrusion process dominates mass production with its cost-effectiveness. It is recommended to use the “3C principle” when making decisions:
- Cost (budget): Extrusion process is preferred for projects over $5,000
- Condition (environment): Casting is required for outdoor/chemical environment
- Customization (customization): Special color/thickness can only be achieved by casting
In the future, with the development of 3D casting technology (MIT Material Lab, 2024), the cost of casting process is expected to be reduced by 30%, further expanding the application boundary.