-
Xinqi Development Zone, Leliu, Foshan, Guangdong
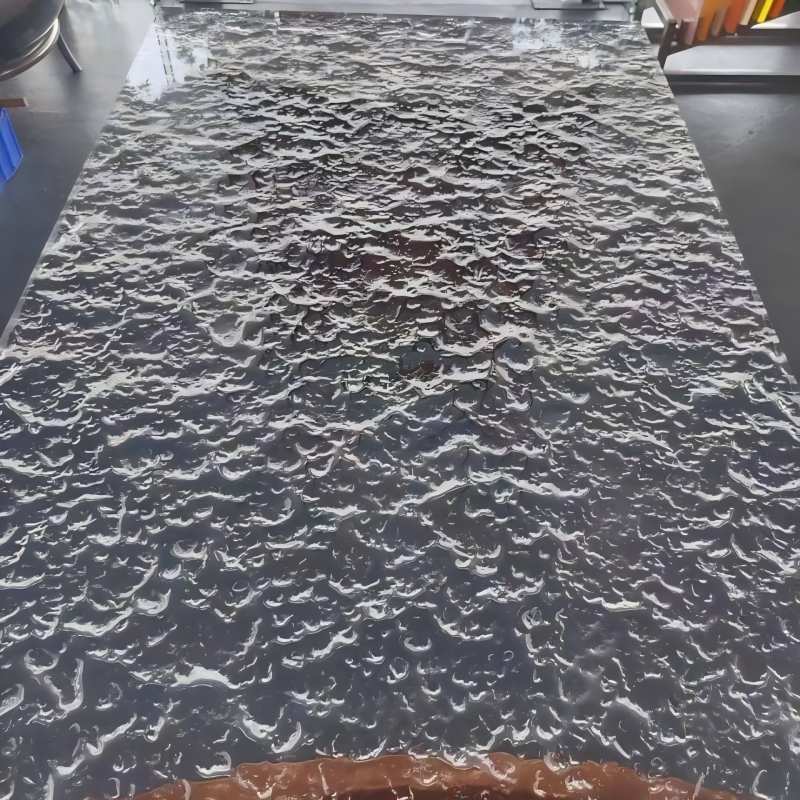
Analysis of 6 Core Advantages of Extruded Acrylic Sheet
Summarize
The scale of the global acrylic industry exceeded 1.71 million tons in 2020 (Statista data), among which the acrylic plate produced by the extrusion process is reshaping the modern manufacturing pattern because of its unique performance advantages. By comparing the casting process, this paper systematically analyzes the excellent performance of extrusion acrylic in six core dimensions, including optical performance, processing efficiency and weather resistance, and cites the research results of authoritative institutions such as the American Chemical Society (ACS) to provide a scientific decision-making basis for material selection.
I. Advantages of industrial production: the cost revolution brought about by continuous process
The extrusion process adopts a continuous production line driven by a spiral drill system. Compared with the intermittent production of the casting process, the single-line daily production capacity can be increased by 300% (Plastics Today industry report). This standardized process of high-temperature melting-mold molding-cooling and shaping not only reduces 15-20% per unit energy consumption, but also realizes the flexible production of 0.5-12mm thickness plates, which perfectly adapts to the precision manufacturing needs of automobile dashboards and medical devices.
II. Breakthrough in optical performance: the technological innovation behind 92% light transmittance
The American Materials Testing Association (ASTM) D1003 standard test shows that the light transmittance of extruded acrylic is 92%, exceeding 85% of ordinary glass. The secret lies in the precisely controlled temperature gradient (180-220℃) and pressure parameters (1.5-3MPa) during the extrusion process, so that the PMMA molecular chain is arranged in an orderly manner. For example, the 3D curved acrylic used in the Tesla Cybertruck panoramic skyscreen realizes the optical surface with 0.5mm accuracy through the extrusion process.
III. Leap in mechanical properties: the impact strength is 17 times that of glass
According to the ACS Journal of Applied Materials, the fracture toughness of extruded acrylic is 1.6MPa·m¹/², which is 17 times that of ordinary sodium-calcium glass. This characteristic stems from the directional distribution technology of toughening agents introduced in the extrusion process. The typical case is the three-layer extruded acrylic composite structure adopted by the Boeing 787 porthole, which successfully passed the 9J impact test stipulated by the FAA.
IV. Environmental adaptability: weather-resistant password for ten years of outdoor use
The ultraviolet accelerated aging test (ISO 4892-3) confirms that the extruded acrylic with UV stabilizer has a yellowing index ΔY<2 after 5000 hours of testing. According to the tracking data of the British Institute of Architecture (BRE), the squeezed acrylic dome used in the London Eye viewing module has a light transmittance of only 3.2% in a 10-year service life cycle, which confirms its excellent weather resistance.
V. Lightweight revolution: the density is only 50% of glass
The extrusion process stabilizes the acrylic density at 1.18g/cm³ (2.5g/cm³ for glass), which has a disruptive impact on the field of new energy vehicles. The roof of the BMW iX adopts 4mm extruded acrylic to replace the traditional glass, reducing the weight of a single piece by 4.2kg. With the extruded curved surface structure, the wind resistance coefficient is reduced by 0.03cd.
VI. Processing friendliness: the secondary molding efficiency is increased by 40%
The German Plastics Processing Association (GKV) research points out that the extruded acrylic thermal deformation temperature (HDT) is 8-10℃ lower than that of casting products, which increases the CNC processing speed to 3m/min. The curved display cabinet used in Apple’s direct-sale store uses the easy-to-process characteristics of the extruded plate to shorten the traditional 7-day hot bending cycle to 72 hours.
Sum up
From medical equipment to aerospace technology, extruding acrylic is reconstructing the material application map with six performance advantages. The 17-year technical accumulation of Sanyu New Materials (passing ISO9001 certification) shows that by optimizing the extrusion process parameters and additive formula, special-grade plates with light transmittance of >93% and bending strength > 110MPa can be customized. It is recommended to obtain UL yellow cards and other certification documents when purchasing, and refer to technical specifications such as Plastics Engineering Handbook for quality verification.