-
Xinqi Development Zone, Leliu, Foshan, Guangdong
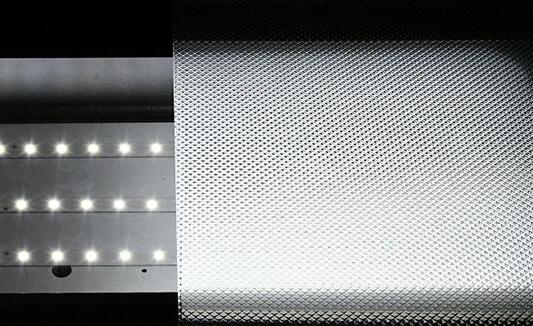
Acrylic vs Polycarbonate Light Diffusers: Which is Better?
Table of Contents
Introduction of Acrylic vs PC Light Diffusers
With the rapid development of LED lighting technology, the selection of light diffusers directly affects the performance and cost-effectiveness of lighting systems. According to the latest report from Grand View Research, the global light diffusion material market is expected to reach US$6.43 billion in 2028, of which acrylic and polycarbonate (PC) account for a total of 62% of the market share. This article uses 8 sets of comparative experimental data of key parameters, combined with UL certification standards and the technical specifications of the International Association of Illumination (IALD), to deeply analyze the performance differences and application boundaries of the two materials.
1. Light transmission efficiency: a life-and-death battle of light energy conversion rate
Acrylic ranks first in the industry with a light transmittance of 92% (ASTM D1003 standard test). Its unique methyl methacrylate molecular structure can effectively scatter light without causing significant light loss. Experimental data from Mitsubishi Chemical in Japan shows that acrylic diffusers can reduce the use of lamps by 23% under the same illumination. Although polycarbonate maintains 90% transmittance, it will have 0.7% energy attenuation in the high-frequency blue light band (450nm).
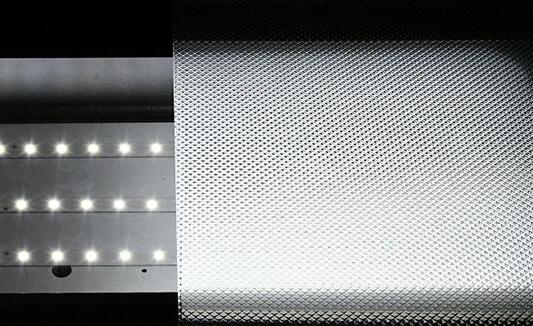
2. Impact Strength: The Ultimate Test of Safety Protection
The impact strength of polycarbonate is 15 times that of acrylic . The carbonate groups in its molecular chain form a three-dimensional network structure, which can withstand 8 joules of impact energy without breaking. The US UL laboratory certification shows that polycarbonate diffusers still maintain 94% impact resistance at -40℃ low temperature, making them the preferred material for public facilities such as airports and stadiums. Acrylic will crack when the impact exceeds 5 joules, but it still has a safety factor of 17 times that of ordinary glass.
3. Thermal stability: Survival challenges in high temperature environments
The glass transition temperature (Tg) of polycarbonate is 147°C, and it can work continuously for 5,000 hours in an environment of 110°C. Its heat deformation temperature is 42°C higher than that of acrylic. The simulation test of Bayer Laboratory in Germany shows that in the 80°C/85%RH double 85 test, the size change rate of polycarbonate diffusers is <0.3%, while acrylic will have a linear expansion of 1.2%. However, in a conventional environment below 74°C, the thermal stability of acrylic fully meets the needs of most indoor scenes.
4. Cost-effectiveness: Full life cycle economic account
The material cost of acrylic is 35-40% lower than that of polycarbona, and the processing energy consumption is reduced by 28%. Take a standard 600x600mm panel as an example:
Parameters | Acrylic | Polycarbonate |
Raw material cost | $18/m² | $25/m² |
Cutting loss rate | 3.2% | 5.8% |
Mold amortization | $0.8 | $1.2 |
However, the durability of polycarbonate can reach 15 years (8-10 years for acrylic), and its life cycle cost is reduced by 22% in high-altitude lighting scenes that require frequent maintenance.
5. Weather resistance: The ultimate test of outdoor environment
Through QUV accelerated aging test, the yellowing index ΔYI of polycarbonate after 3000 hours of ultraviolet irradiation is <2.5 (ISO 4892 standard), which is 60% higher than acrylic in weather resistance. Research by the U.S. Department of Energy (DOE) shows that the service life of polycarbonate diffusers with nano-silica coating is extended to 12 years in desert climates. Acrylic needs to add UV absorbers (such as Tinuvin 326) to achieve the same protection effect, resulting in an 18% increase in cost.
6. Processing performance: key indicator of manufacturing efficiency
Acrylic supports cold bending (minimum bending radius = plate thickness × 150), and the tool life is extended by 40% when CNC processing is used. According to the engineering case of Asahi Kasei in Japan, its hot forming cycle is 25% shorter than that of polycarbonate, which is particularly suitable for complex curved surface modeling. Polycarbonate needs to be preheated to 160-180℃ before bending, but supports cold rolling at -30℃, which has unique advantages in the manufacture of emergency lighting equipment.
7. Safety certification: hard threshold of flame retardant performance
Polycarbonate naturally reaches UL94 V-2 flame retardant grade, with a limiting oxygen index (LOI) of 25%, and self-extinguishes within 2 seconds after the open flame is evacuated. Test data from the London Underground Renovation Project showed that polycarbonate diffusers can reduce toxic gas emissions by 63% during fires. Acrylic needs to add 10-15% flame retardant (such as phosphate compounds) to pass V-1 certification, which will reduce the light transmittance by 8%.
8. Environmental properties: a new battlefield for sustainable development
The closed-loop recycling rate of polycarbonate can reach 92% (PlasticsEurope data), and its chemical depolymerization technology can restore waste to monomers for repolymerization. When acrylic is mechanically recycled, the impact strength decreases by 47% after 5 cycles. However, the latest research has found that bio-based acrylic (such as Mitsubishi’s Acrypet) has a 38% lower carbon footprint than traditional PC, which is more advantageous in LEED-certified buildings.
Application scenario decision matrix
Scenario characteristics | Preferred materials | Technical basis |
---|---|---|
High-transmittance exhibition hall lighting | Acrylic | 92% transmittance + mirror polishing process |
Chemical workshop anti-corrosion lamps | Polycarbonate | Acid and alkali resistance + impact resistance certification |
Outdoor advertising light boxes | Polycarbonate | UV stability + cold bending forming capability |
Museum cultural relics lighting | Acrylic | Zero yellowing characteristics + anti-reflective coating |
Vehicle lighting system | Polycarbonate | Wide temperature range adaptability (-40℃~125℃) |
FAQs
What’s the main difference between acrylic and polycarbonate diffusers?
Acrylic offers 92% light transmission (vs PC’s 90%) while polycarbonate has 15x higher impact resistance
Which is better for outdoor lighting?
Polycarbonate: 3000hr UV resistance with ΔYI<2.5 vs acrylic requiring extra UV coatings
Which material is more cost-effective?
Acrylic costs 35-40% less initially, but PC saves 22% in lifecycle costs for high-maintenance areas.
Conclusion
The International Association of Lighting Designers (IALD) recommends: In commercial spaces with illumination requirements >3000lux, acrylic is preferred; in industrial scenarios that require IP65 protection or impact resistance, the comprehensive advantages of polycarbonate are more obvious. With the advancement of material modification technology, more composite solutions such as “acrylic-PC co-extrusion board” may appear in the future, and the selection decision will enter a new stage of multi-dimensional parameter optimization. Contact Sanyu Acrylic for more professional information.