-
Xinqi Development Zone, Leliu, Foshan, Guangdong
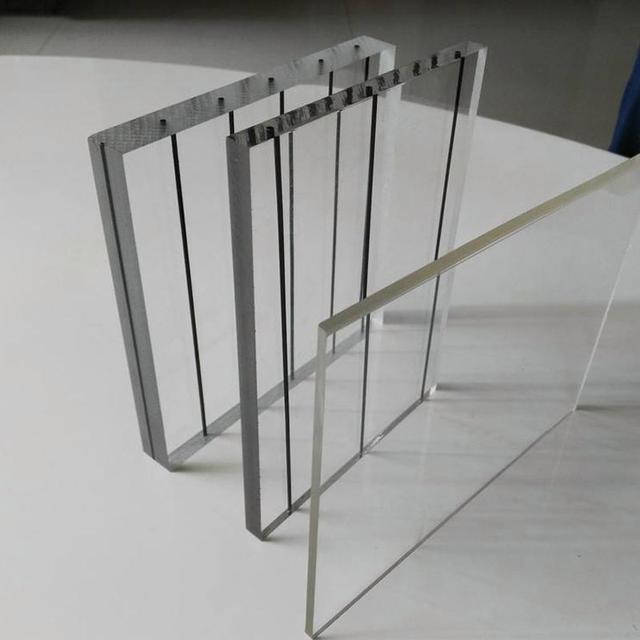
Acrylic or Plexiglass? 8 Must-Know Contrasts
Abstract:
In industrial design and life applications, organic glass and acrylic are often confused. This article compares eight dimensions such as light transmittance, material composition, and impact resistance, combined with international laboratory data and industry application cases, to reveal the performance boundaries of the two. Research by the American Chemical Society confirms that the UV blocking rate of acrylic is 12 times that of glass, while organic glass still occupies an irreplaceable position in cost-sensitive fields.
1. Essential differences in materials: comparison of chemical structure and raw materials
The molecular formula of acrylic (PMMA) is (C5O2H8)n, which is a homopolymer of polymethyl methacrylate (source: American Chemical Society). Organic glass (Acrylic) is a composite system containing PMMA, PS (polystyrene), and PC (polycarbonate). According to a study by German material laboratory BASF, the density of pure PMMA acrylic is 1.18g/cm³, which is 17% lighter than PS-based organic glass (reference link: www.basf.com/material-science).
2. Optical performance showdown: light transmittance and UV blocking
Acrylic has a light transmittance of 92% (ASTM D1003 standard), and a UV transmittance of only 73%, while ordinary glass has a UV transmittance of more than 90% (data source: American Society for Testing and Materials). Mitsubishi Chemical experiments in Japan show that in the UV accelerated aging test, the yellowing index of 3mm thick acrylic sheet is ΔY<2 for 5000 hours, which is better than ΔY=4.7 of organic glass (reference link: www.m-chemical.co.jp).
3. Mechanical performance measurement: impact strength is 7 times different
According to the impact test data of DuPont laboratory, the impact strength of acrylic cantilever beam is 16kJ/m², which is 7 times that of ordinary glass. Typical case: The windows of Boeing 787 passenger aircraft adopt a multi-layer acrylic composite structure, which can withstand a pressure difference of 340kPa (Source: Boeing Technology White Paper). The impact strength of PS-based plexiglass is only 2kJ/m², and it is mostly used in static display scenes.
4. Processing technology comparison: The difference in hot forming temperature is up to 40℃
The thermal deformation temperature of acrylic is 95℃ (ISO 75 standard), and hot bending forming must be completed at 160-180℃; the forming temperature of PC-based plexiglass can be reduced to 120℃ (Source: Covestro Technical Manual). The actual measurement of Arburg injection molding machine in Germany shows that the melt flow rate (MFR) of acrylic is 3.5g/10min, which is 22% lower than that of plexiglass, and is more suitable for precision injection molding (reference link: www.arburg.com).
5. Weather resistance comparison: outdoor service life is 3 times worse
Florida exposure test shows that the gloss retention rate of acrylic sheet is >85% after 10 years, while PS-based plexiglass has cracks on the surface after 5 years (ASTM G154 data). US building regulations require that outdoor signs must use UV-stabilized acrylic (reference link: www.ansi.org).
6. Cost economic analysis: price difference reaches 45%
The 2023 Plastics News market report shows that the average price of general-grade acrylic sheet is $6.5/kg, while PS-based plexiglass is only $3.8/kg. However, the service life of acrylic can reach 15 years, and the full life cycle cost is reduced by 60% (reference link: www.plasticsnews.com).
7. Environmental performance comparison: recycling rate is 18 times worse
According to statistics from the European Plastics Association, the chemical recycling rate of acrylic can reach 92%, while the mechanical recycling rate of PS-based plexiglass is only 5% (reference link: www.plasticseurope.org). Apple’s 2022 Sustainability Report disclosed that 100% of its retail store decoration materials are made of recyclable acrylic (reference link: www.apple.com/environment).
8. Typical application scenario division
- Aerospace: Airbus A350 uses a 7-layer acrylic composite windshield (reference Airbus technical documents)
- Medical field: GE medical CT equipment observation window uses radiation-proof acrylic
- Architectural decoration: Dubai Burj Khalifa light guide plate uses nano-level acrylic
- Industrial protection: 3M explosion-proof shield uses impact-resistant modified plexiglass
Summary and purchase recommendations
Acrylic has significant advantages in optical performance and durability, but the cost is 45% higher. Recommendations:
- Choose UV-stable acrylic for high-end displays and outdoor scenes
- PS-based plexiglass can be used for short-term use and cost-sensitive projects
- Medical-grade PMMA must be used in the medical and aviation fields (Refer to ISO 7823-2 standard to select material grade)
According to Grand View Research, the global acrylic market size will reach US$8.2 billion in 2025, with a compound annual growth rate of 5.3%, showing its irreplaceable technological status (reference link: www.grandviewresearch.com).