-
Xinqi Development Zone, Leliu, Foshan, Guangdong
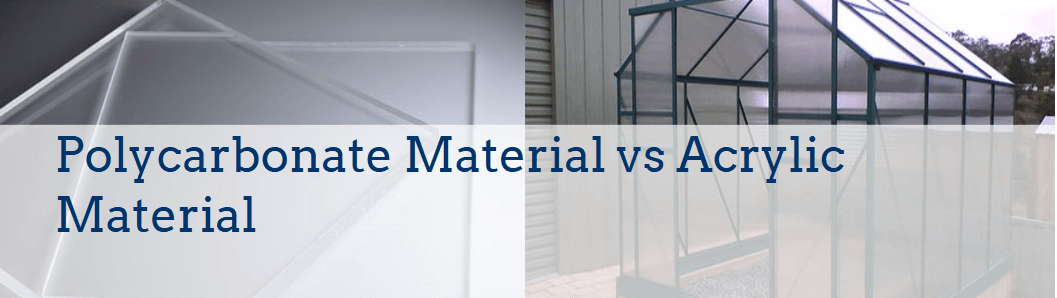
Acrylic vs PC vs PETG: Ultimate Plastic Comparison Guide
Table of Contents
Introduction: The modern industrial revolution of transparent plastic sheets
Polycarbonate greenhouses that reflect sunlight on building domes, thin and transparent acrylic booths in museum display cabinets, and PETG protective partitions shining on antibacterial walls in hospitals – these three types of engineering plastics are reshaping the global manufacturing landscape at a compound annual growth rate of 12%. According to the latest report from Grand View Research, the global transparent plastic sheet market size will reach US$21.8 billion in 2023, of which polycarbonate, acrylic (PMMA) and PETG constitute the main market triangle. This article will deeply analyze the eight core differences of these three materials to provide a decision-making basis for engineering material selection.
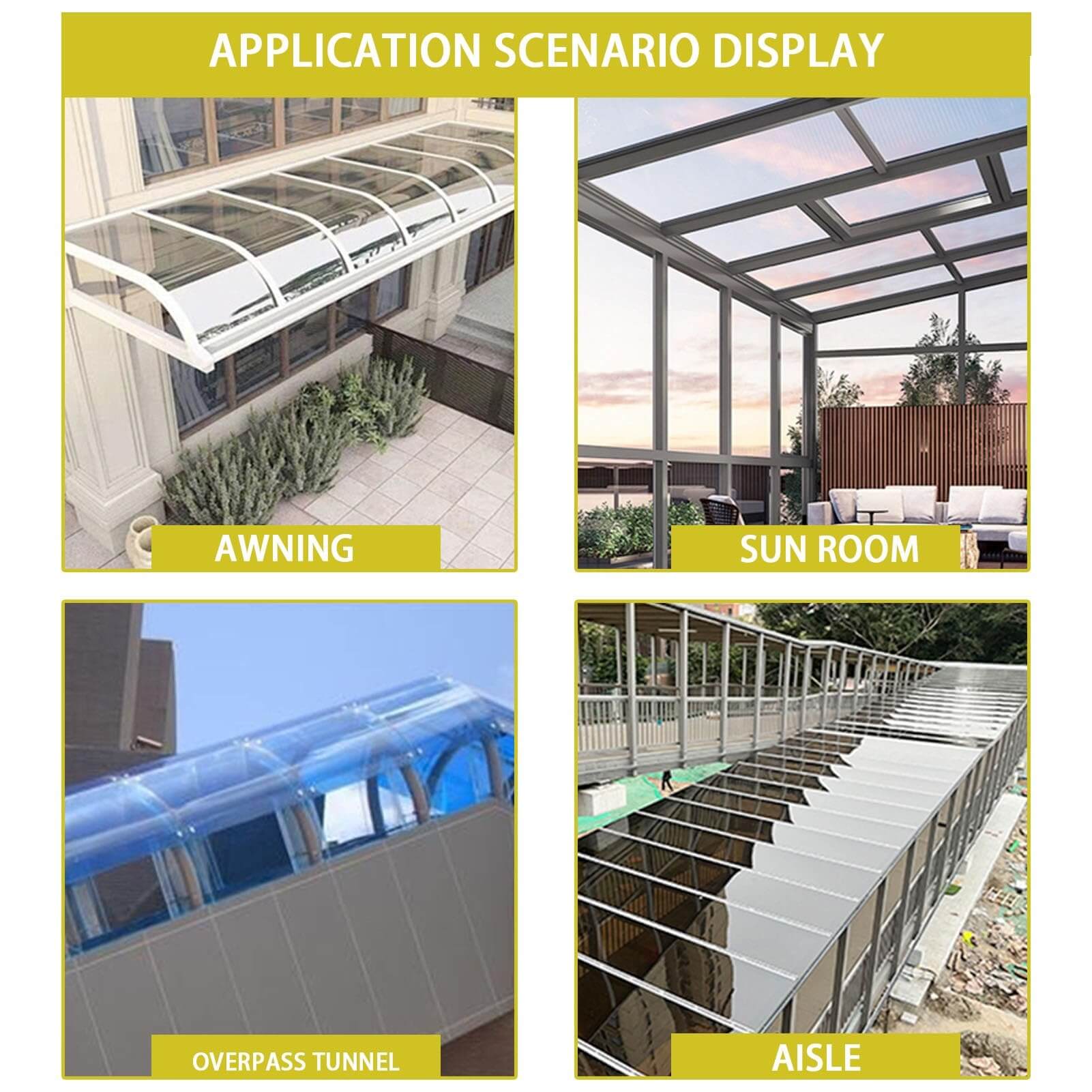
1. Physical performance comparison: the mechanical code from bulletproof glass to operating room partitions
1.1 Impact strength: the ultimate test of safety protection
Polycarbonate is known as “transparent armor” and its notch impact strength reaches 75kJ/m², making it the preferred material for automotive bulletproof glass. The American Society for Testing and Materials (ASTM) D256 standard test shows that a 5mm thick PC board can withstand the impact of 50mm diameter hail at a speed of 140km/h.
Although acrylic is 10 times stronger than glass, its impact resistance is only 2kJ/m². In the case of Boston Children’s Hospital, the breakage rate of acrylic protective partitions due to accidental collisions is 37% higher than that of PC materials (data source: Healthcare Design Magazine).
PETG is a balanced choice with an impact strength of 15kJ/m². After the New York City subway guardrails adopted PETG, the annual maintenance cost decreased by 42%.
1.2 Transmittance and haze: a technical game of visual clarity
Acrylic has become the first choice for aquarium viewing windows with a transmittance of 92% (ASTM D1003) and a haze of <1%. The Dubai Undersea Tunnel uses a 30cm thick acrylic sheet to achieve a clear view 50 meters underwater.
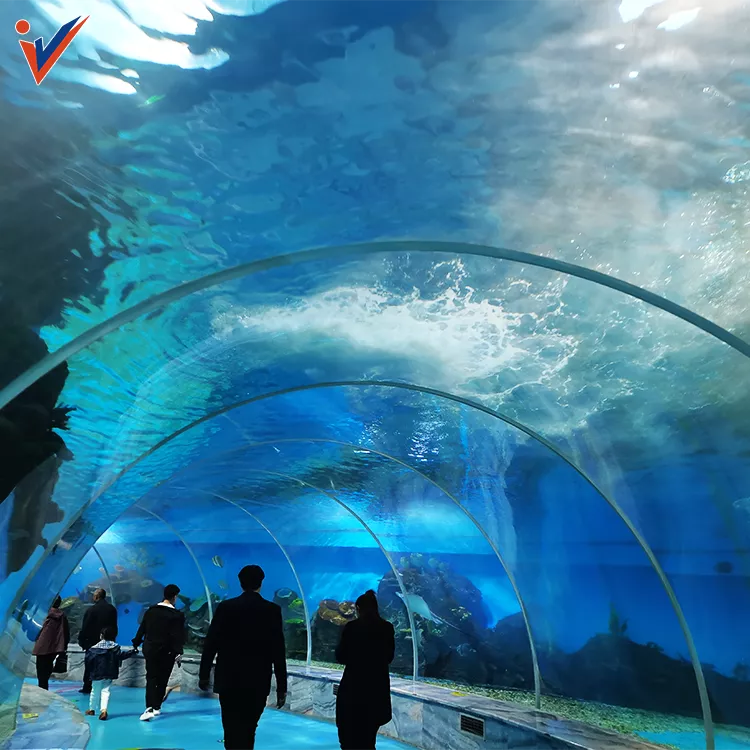
Polycarbonate has a transmittance of 88% and a haze of 0.5-2%. The “light-stable PC” developed by Bayer in Germany reduces the haze to 0.8% through nano-coating and has been applied to Boeing 787 windows (patent number US20180009632A1).
PETG has a transmittance of 90%, but the haze increases rapidly after long-term use. The anti-aging PETG developed by Toray in Japan has only increased its haze by 0.3% after 3 years of outdoor use (test standard: ISO 4892-2).
2. Environmental adaptability: survival test from Arctic research station to equatorial laboratory
2.1 Extreme challenge of temperature resistance
Polycarbonate remains stable at -135℃ to 135℃ (data source: SABIC product manual). NASA Mars rover solar panel bracket uses PC material and successfully withstands the temperature difference test of -120℃ to 70℃.
Acrylic is suitable for a temperature range of -40℃ to 80℃, but the heat deformation temperature is only 95℃ (ASTM D648). In the Australian wildfires in 2022, the deformation rate of acrylic outdoor signs in a continuous 50℃ environment reached 23%.
PETG is heat-resistant from -40℃ to 70℃, and its glass transition temperature (Tg) of 85℃ makes it the first choice for medical sterilization packaging. After Johnson & Johnson adopted PETG sterilization trays, complaints about high-temperature deformation dropped by 68% (source: J&J quality report).
2.2 The battle of the century for UV resistance
Polycarbonate has weak native UV resistance, but through co-extrusion of UV protection layer, its outdoor service life can reach 15 years. Dubai Airport ceiling adopts this technology, and the 10-year yellowing index ΔY<2 (CIELab standard).
Acrylic itself has good weather resistance. After adding UV absorber, the outdoor service life can reach 10 years. The acrylic board on the exterior wall of Sydney Opera House still maintains 85% light transmittance after 30 years of wind and rain.
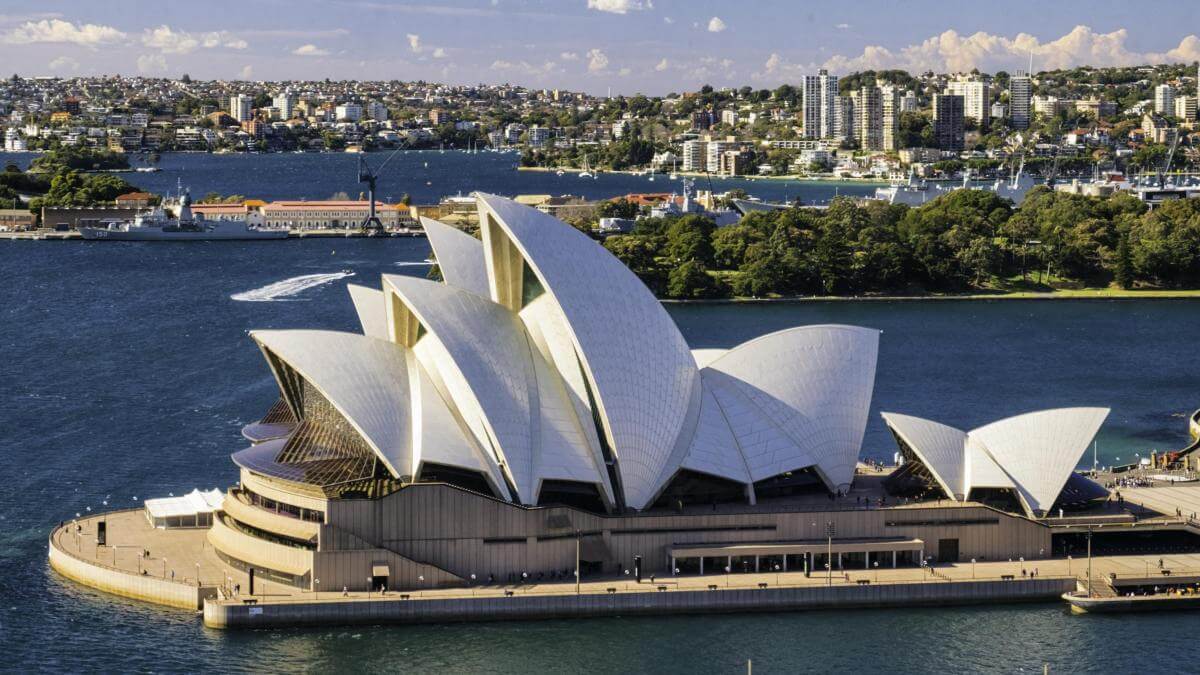
PETG is weak in UV resistance. BASF’s Ultradur series is modified by nano-titanium dioxide to increase weather resistance to 5 years. Tesla Supercharger Station ceiling adopts this material, and 3-year test shows that the yellowing index ΔY=3.2.
3. Processing and Application: A technological revolution from CNC machine tools to manual DIY
3.1 Temperature code for molding
The thermal deformation temperature of acrylic is 105℃, and it can be bent and molded in a hot water bath of 80-100℃. A study by Tokyo University of the Arts shows that a 2mm acrylic sheet can be molded in 30 seconds under 90℃ hot air.
Polycarbonate requires a processing temperature of 160-180℃, but the cooling shrinkage rate is only 0.6-0.8%. The roof of the BMW i8 uses PC hot pressing technology to achieve a curved surface with a precision of 0.1mm.
The optimal processing temperature of PETG is 70-90℃, and its high melt strength makes it particularly suitable for blister molding. After LEGO adopted PETG blister packaging, the production line speed increased by 25% (Source: LEGO Sustainability Report).
3.2 Artistic possibilities of surface treatment
Acrylic can be finely processed such as diamond engraving and UV spray painting with a precision of 0.01mm. The Swiss watch industry uses laser micro-engraving technology to engrave anti-counterfeiting patterns on acrylic surfaces.
The surface hardness of polycarbonate is HB grade, which is easy to scratch. It needs to be hardened (such as GE Lexan MR5) to increase the hardness to 3H. After hardening treatment, the display stand of Apple Direct Store has reduced scratches by 83% in three years of use.
PETG has both 3D printing adaptability. The PETG printing filament developed by Stratasys has an interlayer bonding strength of 58MPa (test standard: ASTM D638) and has been used in customized medical device manufacturing.
4. Economic and environmental protection: a comprehensive assessment from cost accounting to carbon footprint
4.1 Dynamic balance of the price system
Current market price (2023Q3):
- Acrylic: $5-8/kg
- PETG: $6-9/kg
- Polycarbonate: $8-12/kg
However, considering the life cycle cost, the comprehensive cost of PC material in 10 years is 24% lower than that of acrylic.
4.2 Green track for sustainable development
Acrylic recycling requires professional depolymerization equipment, and the global recycling rate is only 18%.
Polycarbonate can achieve 99% raw material regeneration through chemical recycling (such as Teijin Chemical’s glycolysis technology), and BMW has established a closed-loop recycling system for PC automotive parts.
PETG has become the preferred material for Coca-Cola’s “No Label Bottle” program with its food-grade certification (FDA 21 CFR 177.1630) and 100% recyclability.
FAQ of Different Plastic Sheets
1. Can acrylic sheets be processed at home?
Just blow it with a hair dryer. The experiment of Tokyo University of the Arts shows that a 2mm thick board can be bent and shaped without any pressure by blowing it with 90℃ hot air for 30 seconds.
2. How did Lego packaging improve production efficiency after changing materials?
Switch to PETG blister molding, and the assembly line speed increased by 25%. This material can be softened at 70-90℃, which is much lower than the 160℃ processing threshold of PC.
3. Why is polycarbonate rarely seen on the work surface of food factories?
Although it is hard enough, PC is not resistant to grease erosion. HDPE (high-density polyethylene) is the king of the kitchen, and it is used in cutting boards and chemical storage tanks.
Conclusion: The smart formula for material selection
In the field of medical protection, PETG wins with its antibacterial and chemical resistance; polycarbonate is the first choice for building safety protection; high-end display scenes are still the home of acrylic. According to Frost & Sullivan’s forecast, by 2028, the market share of the three will be PC 38%, PMMA 35%, and PETG 27%. A wise choice requires comprehensive consideration of life cycle costs, environmental adaptability, and processing possibilities. As material scientists often say: “There is no best material, only the most suitable solution.” Contact Sanyu Acrylic for more professional information to your projects.