-
Xinqi Development Zone, Leliu, Foshan, Guangdong
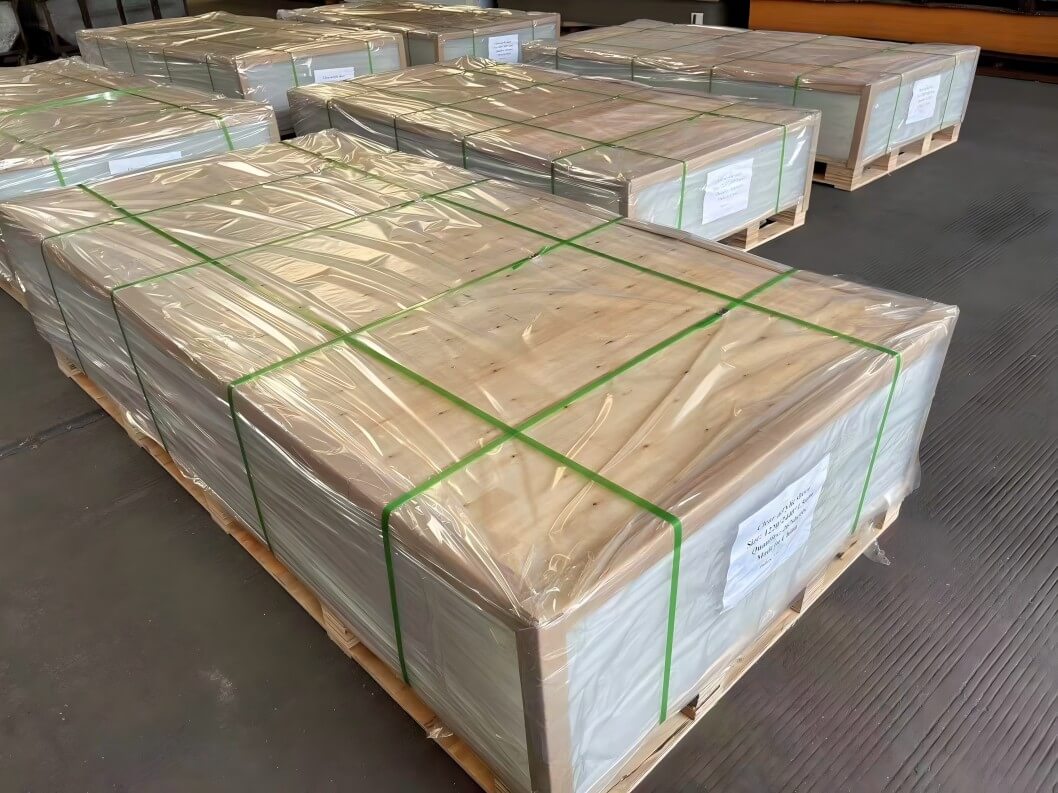
How Acrylic Thickness/Density Affects Shipping Costs?
Table of Contents
Introduction
Acrylic sheets have become the preferred material for industries such as advertising, construction, and furniture due to their high light transmittance, weather resistance, and ease of processing. However, their transportation costs often fluctuate significantly due to differences in thickness and density. Studies have shown that transportation costs can account for 15%-30% of the total material cost. This article analyzes how the thickness and density of acrylic sheets affect transportation costs from five dimensions: weight calculation, loading efficiency, packaging reinforcement, damage risk, and transportation strategy, combined with authoritative data and cases, to provide companies with a scientific cost reduction solution.
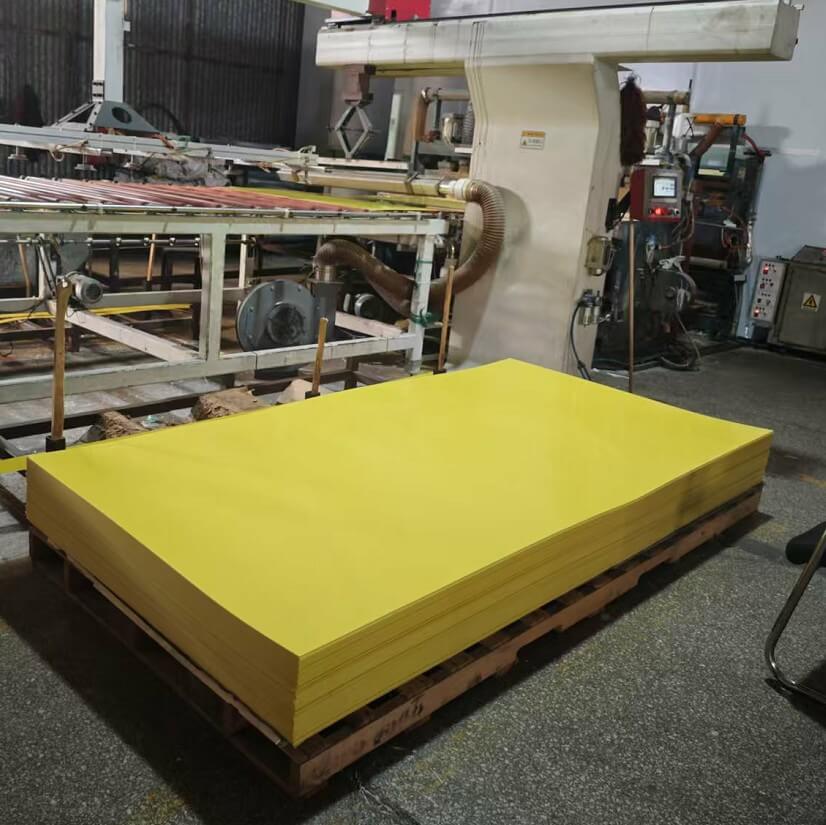
Weight and freight calculation: “Hidden costs” under constant density
The density of acrylic sheets is stable at 1.19~1.20g/cm³ , but the thickness directly affects the weight of a single sheet. For example, a 3mm thick (1220mm×2440mm) sheet weighs about 8.7kg, while a 10mm thick sheet of the same size weighs 29kg, an increase of 233%. In a logistics model that charges by weight (such as air freight or LTL land transport), freight increases linearly with thickness. Based on the FedEx land transport unit price of $0.5/kg, the freight cost of a single 10mm sheet is $10.15 higher than that of a 3mm sheet, and the cost difference can reach tens of thousands of dollars when transporting in large quantities (case reference: FedEx freight calculator).
Loading efficiency: How thickness “compresses” space profit
Transportation cost is not only related to weight, but also constrained by space utilization. Thinner acrylic sheets can be stacked in multiple layers to maximize the use of container volume. Taking a standard 40-foot container (volume 67m³) as an example, 3mm sheets can load 1,500 sheets, while 10mm sheets can only accommodate 450 sheets, reducing space utilization by 70%. If the unit price of sea freight is US$2,000/container, the unit transportation cost of 10mm sheets is as high as US$4.44/sheet, which is 3.3 times that of 3mm sheets (US$1.33/sheet). Enterprises need to balance loading volume and weight cost through thickness selection.
Packaging reinforcement needs: the “protection fee” trap of thick sheets
Because of the large weight of a single piece, thick sheets are prone to damage to corners due to vibration during transportation. To reduce risks, logistics companies often require additional wooden frame support or shock-proof foam, which increases packaging costs by 20%-40%. According to data from the American Packaging Association, the cost of reinforcing 10mm sheets is about $8 per sheet, while 3mm sheets only cost $3. In addition, overweight sheets may trigger a “non-standard cargo” surcharge, further pushing up costs.
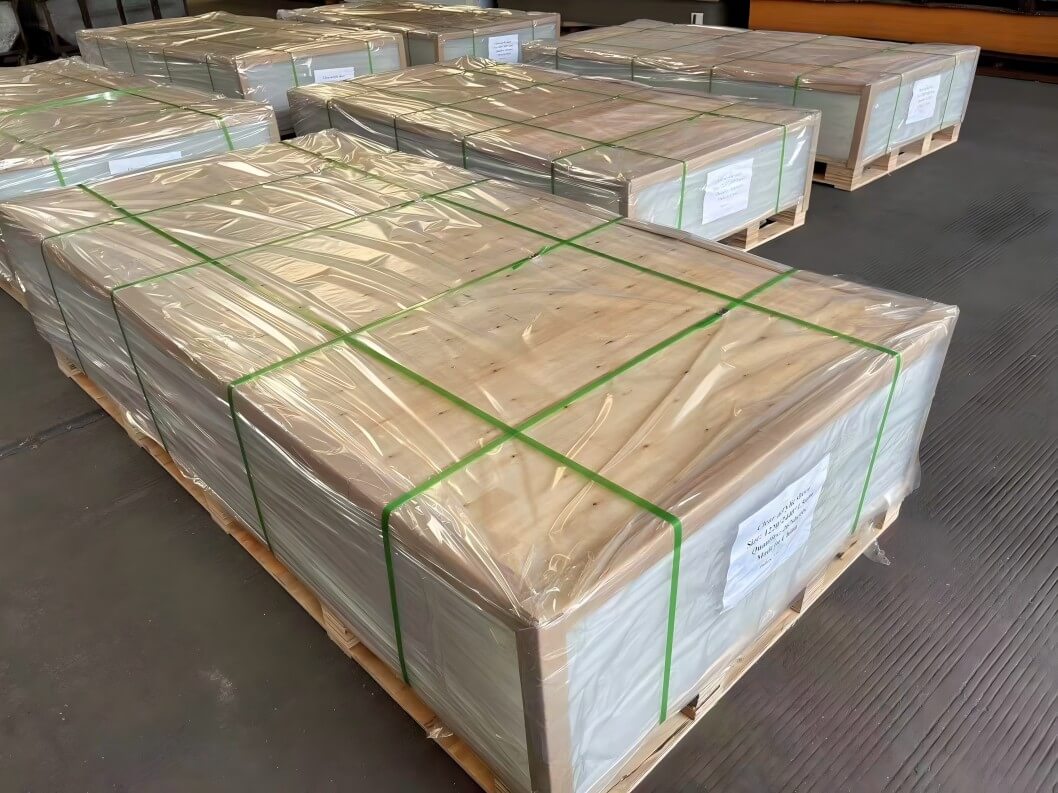
Damage rate and risk cost: the “damage resistance advantage” of thick sheets
Although thick sheets have high transportation costs, their impact resistance can reduce the risk of damage. Experiments show that the damage rate of 3mm sheets in long-distance transportation is about 5%, while that of 10mm sheets is less than 1%. Calculated at a single sheet value of $200, transporting 1,000 3mm sheets may result in a claim loss of $10,000, while thick sheets only cost $2,000. Enterprises need to assess risks based on transportation distance: short-distance transportation may prefer thick plates, while long-distance transportation requires comprehensive cost and breakage rate to select moderate thickness.
Transportation Strategy Optimization: Multidimensional Data-Driven Decision Model
- Sea Transportation Priority: Thick plates are suitable for sea transportation because of their heavy weight but durability. Taking the China-U.S. West Coast route as an example, the cost of sea transportation is only 1/6 of that of air transportation (Source: World Bank Logistics Report).
- Mixed Loading: Combine orders of different thicknesses for transportation and use thin plates to fill the gaps in the container.
- Regional Warehouses: Set up warehouses near the target market to reduce the frequency of long-distance transportation. For example, IKEA reduced the transportation cost of plates by 12% through global warehouses.
FAQ
How to optimize the transportation strategy for acrylic boards?
① Prioritize sea transportation; ② Mix orders of different thicknesses; ③ Set up warehouses for target markets, such as IKEA reducing costs by 12% through warehouses.
Which is more suitable for transporting acrylic boards, sea transportation or air transportation?
Thick boards are suitable for sea transportation (the cost is 1/6 of air transportation), and thin boards or urgent orders can be transported by air. The weight and timeliness need to be balanced.
How to calculate the shipping cost of a single acrylic sheet?
Formula: Single sheet freight = (weight × unit price) + packaging fee + surcharge. For example, the sea freight cost of a 10mm sheet is about US$4.44 per sheet (including packaging).
Is there a recommended thickness with the “best cost performance”?
A comprehensive assessment of the transportation distance is required. For example, 5-8mm is recommended for export trade, and 10mm or more can be selected for local short-distance to reduce the breakage rate.
Is it possible that the density may change due to different production processes?
The density error of regular manufacturers is ≤0.01g/cm³ (refer to Röhm standard), and the slight difference has no actual impact on the transportation cost.
Conclusion
The transportation cost of acrylic plates is the result of the combined effect of thickness, density, packaging, risk and logistics strategy. Enterprises need to establish data models to quantify the “full-link cost” of plates of different thicknesses, and make flexible choices based on transportation distance and order size. For example, for export trade, 5-8mm plates can be used to balance loading capacity and damage resistance, while local orders can use specifications above 10mm to reduce packaging costs. Through scientific decision-making, enterprises can reduce transportation costs by 10%-25% while ensuring delivery quality (Source: MIT Supply Chain Management Research).