-
Xinqi Development Zone, Leliu, Foshan, Guangdong
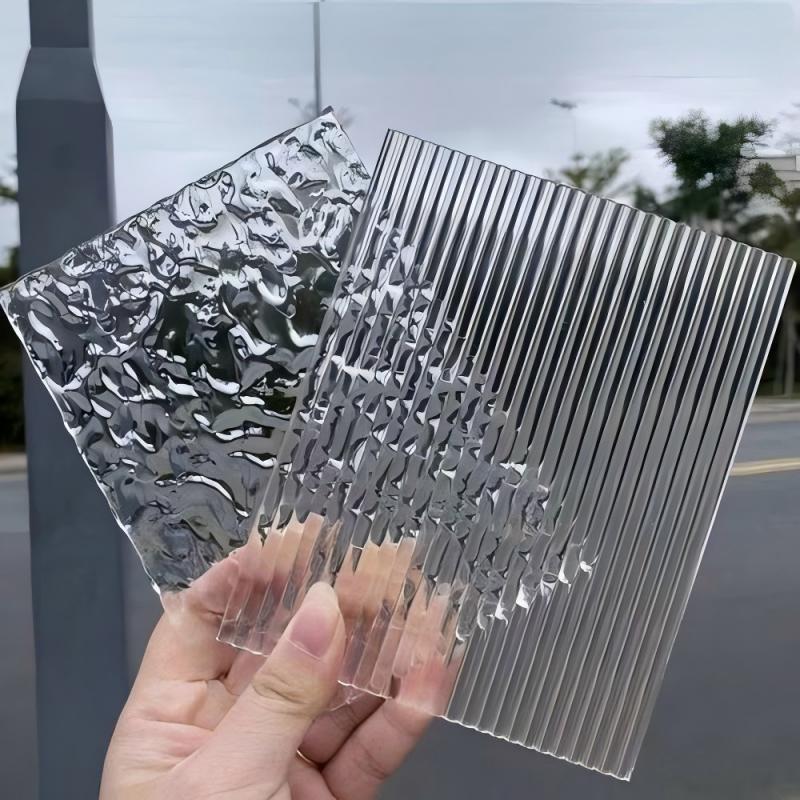
Acrylic Sheet Classification: 8 Key Dimensions Revealing Core Advantages
Abstract:
Acrylic sheets have become essential materials in construction, advertising, and home furnishing industries due to their exceptional light transmission, weather resistance, and formability. This article systematically analyzes acrylic sheet classifications through 8 critical dimensions including manufacturing processes, performance parameters, and application scenarios. It provides detailed comparisons between cast and extruded acrylics, citing ASTM standards and PlasticsEurope industry reports. Includes a golden selection checklist and emerging smart material trends.
1. Production Process: Molecular Structure Revolution in Casting vs. Extrusion
Cast acrylic forms high molecular weight structures (>1,000,000) through mold curing, achieving 92% light transmittance and 90MPa flexural strength (ASTM D638), ideal for aquarium windows. Extruded acrylic features linear molecular chains (600,000-800,000 MW) enabling 0.8-3mm thin sheets production with ±0.05mm thickness tolerance.
2. Optical Performance: Precision Control of Light Transmission
- Transparent Grade: ≥92% transmittance with <1% UV transmission
- Diffused Grade: 0.6-1.2 Haze value for LED light homogenization
- Colored Grade: ΔE<2.0 after 10-year outdoor exposure (ISO 105-B02)
3. Mechanical Properties: Rigidity-Flexibility Balance
Cast panels achieve Rockwell M100 hardness (ASTM D785), while extruded sheets allow cold bending at 150× thickness radius.
4. Surface Treatments: Functional & Aesthetic Innovations
- Mirror Finish: >95% reflectivity with Ra≤0.01μm roughness
- Frosted Surface: 0.3-0.8μm micropores maintaining 80% light transmission
- Embossed Patterns: 120 texture options via KURZ hot stamping
5. Specialized Functions: From Fire Resistance to Antibacterial
- Flame Retardant: UL94 V-0 certified with >28% oxygen index
- Anti-static: 10^6-10^9Ω surface resistance (IEC 61340)
- Antimicrobial: 99.9% bacteria inhibition (JIS Z 2801)
6. Extrusion Process Advantages
- Cost Efficiency: 40% energy reduction vs. casting
- Thickness Control: ±0.05mm (ISO 2768-m)
- Production Speed: 6m/min continuous output
- Eco-friendly: <50μg/m³ VOCs emission (EPA 311)
7. Application Scenario Matrix
Requirement | Cast Acrylic | Extruded Acrylic |
---|---|---|
Load Capacity | >50kg/m² | <30kg/m² |
Temperature Range | -40℃~90℃ | -20℃~70℃ |
Processing Method | CNC machining | Thermal bending |
Cost Consideration | Premium projects | Mass production |
8. Future Trends: Intelligent Acrylic Solutions
Evonik’s smart dimming panels with ITO layers (Evonik) enable 5%-80% light adjustment. Mitsubishi Rayon’s UV-responsive sheets (Patent JP2020158904A) auto-frost at >5mW/cm² intensity.
Conclusion:
Acrylic classification systems enable precise material “modularization”. While cast acrylic dominates high-end markets, extrusion technology drives industrial democratization. Implement the “Four-Dimensional Selection Framework”: 1) Mechanical/Environmental Requirements 2) Processing Methods 3) Budget Constraints 4) Future-Proofing via Plastics Industry Association Toolkit. Nano-modified acrylics are transitioning from passive substrates to active functional interfaces.