-
Xinqi Development Zone, Leliu, Foshan, Guangdong
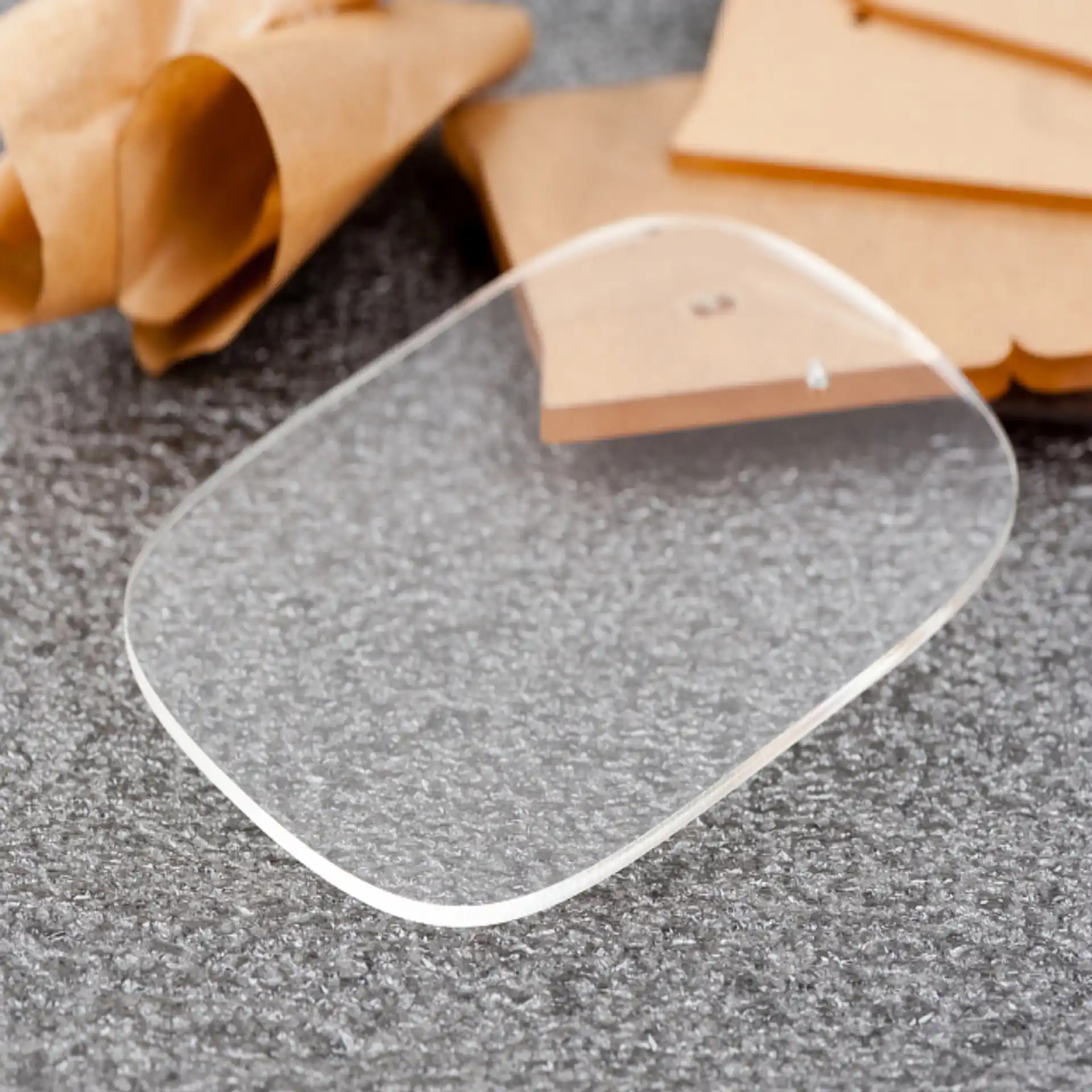
Achieve Glass-Like Acrylic Edges With Flame Polishing
In the fields of high-end displays, building curtain walls and art installations, the edge finish of an acrylic board often determines the final value of the product. When traditional grinding and polishing are difficult to achieve glass-like transparent edges, flame polishing technology stands out with its high efficiency and excellent results – the operator sweeps the edge of the acrylic with a flame spray gun, and the originally matte and rough edge instantly becomes as transparent as crystal. Behind this magical process is the precise grasp of material properties and thermal control.
1. The technical essence of flame polishing
Flame polishing is essentially a surface micro-melting reshaping technology. Acrylic (PMMA) is a thermoplastic material. When heated to about 105°C, it reaches the softening point. At this time, the surface molecular layer flows but the overall structure remains solid. Flame polishing takes advantage of this characteristic. It melts the surface fine defects at a short high temperature, uses surface tension to re-level the material, and forms an optically transparent edge after cooling.
Compared with mechanical polishing, flame polishing has significant advantages for complex geometric structures. Whether it is the curved grooves of advertising crystal characters or the inner hole structure of special-shaped sculptures, the flame can reach the dead corners that are difficult to handle with traditional tools. Experimental data shows that it only takes 15-20 seconds for a professional operator to complete the edge polishing of 1 meter of acrylic, which is more than 5 times more efficient than mechanical polishing. However, this technology has basic requirements for material thickness. Only plates above 3mm can withstand thermal shock without deformation. Thin plates require more advanced skills.
2. Equipment selection and flame optimization
Flame quality is the key factor in the success of polishing:
- Hydrogen-oxygen flame polisher: It produces hydrogen-oxygen mixed gas through electrolysis of water, with a combustion temperature of about 2800°F. The flame is pure and free of carbon particles, avoiding contamination of the acrylic surface. It is the first choice for high-end processing
- Propane spray gun: It has a low cost but needs to be precisely adjusted to a blue conical flame (length 5-10cm). The yellow flame tip will cause soot deposition
- Butane micro torch: It is suitable for small area repairs and is easy to control
The automatic flame spray mechanism developed in the patented technology (CN202311144808.2) realizes real-time adjustment of flame intensity through a dual-path gas supply system to ensure uniform heating of plates of different thicknesses. Safety configuration is equally important. The work area must be equipped with an explosion-proof ventilation system, and the operator must wear carbon fiber heat-resistant gloves (protection level ≥800℃) and a UV-proof mask.
3. Standardized operation process
Substrate pretreatment The acrylic edge after cutting needs to be initially polished with 400-grit sandpaper to eliminate saw marks, and then finely polished with 800-grit or above water sandpaper until there is no obvious grain. After each process, it must be cleaned with anhydrous alcohol and lint-free cloth. Any oil stains or dust will form permanent defects at high temperatures.
Dynamic thermal control technology
- Keep a 5-10cm distance between the spray gun and the plate, and move at a uniform speed of 10cm/s
- Each edge is treated for no more than 1 second
- The thick plate adopts the “multiple flash burning” strategy (cooling after 30 seconds each time)
Observing the melting state is the core technical point: If the mirror reflection appears on the surface, immediately remove the flame. If tiny bubbles or misty white marks are generated, it means that it is overheated. For thin plates with a thickness of less than 3mm, a copper plate can be attached to the back to help dissipate heat.
4. Polishing solutions for special structures
Internal hole polishing (such as hole structures with a diameter of 16mm and a wall thickness of 2.5mm) requires creative methods:
- Convert the micro spray gun to an L-shaped curved nozzle
- Adjust the flame intensity to 1/3 of the normal value
- Use intermittent operation of “0.5 second spot burning + rotating the workpiece”
- Pre-embed the metal core rod in the hole to absorb excess heat
Curved edge processing requires combined with automated equipment. The displacement flame polishing device described in patent CN117584436B controls the spray gun trajectory through a programmable servo system and synchronously rotates the workpiece to maintain the optimal polishing angle. For super large plates (>2m), it is recommended to use a positioning workbench with a water-cooled interlayer to prevent local temperature accumulation.
5. Quality defect analysis and control
Common problems in flame polishing are essentially the product of thermal runaway:
- Edge curling: mostly due to heat concentration on the right-angle edge of the thick plate, pre-chamfering 45° can disperse stress
- Atomized white spots: flame stays for too long, causing molecular degradation, and need to be lightly polished with 800-grit sandpaper before re-polishing
- Bubble pits: the moisture content of the material exceeds the standard (should be <0.2%), and it needs to be dried at 80℃ for 4 hours before processing
Environmental factors are often ignored: When humidity>70%, water vapor condenses on the cold plate surface, resulting in star-shaped cracks on the polished surface; Wind speed>1m/s causes uneven cooling and deformation. It is recommended to operate in a constant temperature and humidity workshop (temperature 23±2℃, humidity 50±5%).
6. Technological evolution and innovation direction
Current cutting-edge technologies focus on intelligent control:
- Infrared temperature measurement module monitors the surface temperature of the board in real time
- Visual system automatically identifies edge geometric features
- Parameter adaptive adjustment (such as the servo linkage system in the patent of Longnan Xintao Acrylic Technology)
Hydrogen-oxygen polishing machines are upgrading towards green manufacturing. The new generation of equipment integrates a wastewater circulation system, and the electrolysis efficiency is increased to 3.2kWh/m³, which is 40% more energy-efficient than traditional equipment. The composite process (such as flame + chemical polishing liquid assistance) can process 0.8mm ultra-thin boards, expanding the technical boundaries.
Data comparison of a high-end display rack manufacturer: Traditional cloth wheel polishing takes 7 minutes per piece, with a pass rate of 85%; after the integrated transformation of the flame polishing system, the single piece processing is reduced to 1.2 minutes, and the pass rate jumps to 98%.
Conclusion: The temperature philosophy of Seiko Art
Flame polishing transforms seemingly destructive heat energy into a means of creating perfection. The essence of this skill lies in the precise balance of heat and time. From the agility of manual spray guns to the precision of automated equipment, the evolution of technology has always revolved around a core goal: to capture the magic moment of gloss freeze at the moment when acrylic molecules begin to flow. When the first beam of light penetrates the polished edge without hindrance, the sublimation from industrial products to optical works of art is completed.
Authoritative resource expansion:
- International Acrylic Manufacturers Association – Material technical standards
- SGS material test report – Polished surface weathering data
- German Roth flame polishing equipment – Industrial-grade solutions
- American Society of Plastics Engineers – Thermoplastic processing technology white paper
FAQs
Q1: Which flame type is best for acrylic polishing?
A: Hydrogen-oxygen mix creates soot-free flames, while propane requires precise blue-cone adjustment to avoid carbon deposits.
Q2: Can thin acrylic sheets (<3mm) be flame polished?
A: Yes, using copper heat-sink backing and 0.5-second flash heating intervals to prevent warping.
Q3: Why do white streaks appear during polishing?
A: Caused by overheating. Cool the sheet, lightly sand with 800-grit paper, and repolish at lower temperature.
Q4: How to polish curved acrylic edges effectively?
A: Use programmable servo systems with rotational workpiece holders to maintain optimal flame angle.
Q5: What humidity level is required?
A: Maintain 50±5% RH. Above 70% causes micro-cracks from moisture condensation.