-
Xinqi Development Zone, Leliu, Foshan, Guangdong
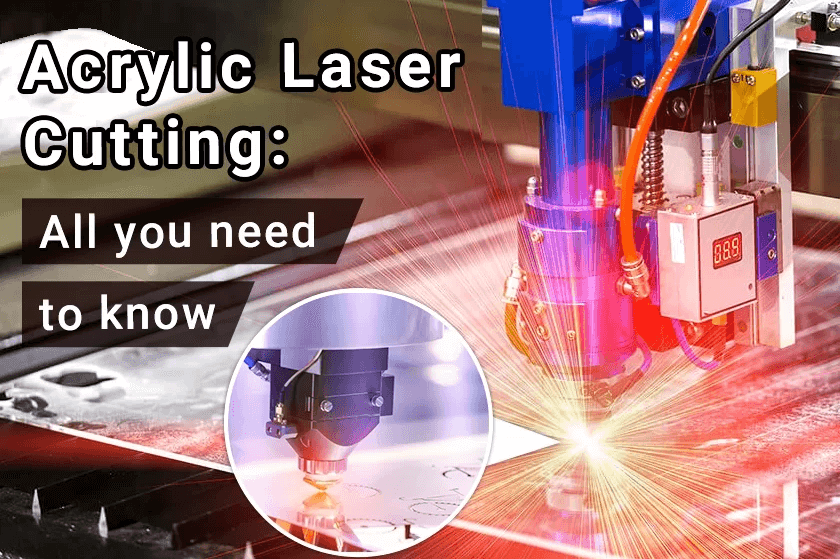
8 Core Skills for Laser Cutting Acrylic Sheets
Table of Contents
Introduction: The innovative value of laser cutting technology
According to the latest report from Global Market Insights, the global laser cutting equipment market is expected to exceed US$8 billion in 2027, of which acrylic processing accounts for 23% of the application share. This lightweight and light-transmitting material has become the first choice in advertising signs, industrial manufacturing, art design and other fields due to its excellent plasticity and aesthetics. However, to truly take advantage of the technical advantages of laser cutting, it is necessary to master the operating skills of the system. This article integrates authoritative industry data and practical experience to reveal the scientific principles and practical methods of 8 key skills.
1. Material selection: the watershed between cast and extruded acrylic
Research by the American Plastics Industry Association (SPI) shows that the molecular density of cast acrylic is 15% higher than that of extruded type, which directly determines the difference in cutting effect:
- Cast acrylic: the average cutting speed can be increased by 20%, and the edge smoothness reaches Ra 0.8μm (equivalent to mirror grade)
- Extruded acrylic: affected by internal stress, it is easy to produce micro cracks of 0.5-1.2mm
Expert advice: Polycast® brand cast sheets (product parameters) are preferred for precision electronic component packaging, while extruded materials with higher cost performance can be considered for short-term display props
2. Three-dimensional optimization model of laser parameters
The technical white paper of TRUMPF Laser (TRUMPF) in Germany points out that the golden ratio formula of power-speed-frequency is:
P = (T×V)/K
Where P is power (W), T is thickness (mm), V is speed (mm/s), and K is material coefficient (cast acrylic K=120, extrusion type K=90)
Practical case: When cutting 3mm cast plate, the recommended parameter combination is: Power 45W | Speed 12mm/s | Frequency 2000Hz (Data source: TRUMPF parameter manual)
3. Contradictory solution for protective film treatment
The MIT Materials Engineering Laboratory test found that retaining the bottom protective film can reduce scratch damage by 73%, but it should be noted that:
- Remove the top film to avoid carbonization (the protective film will stick when the temperature exceeds 160°C)
- Use 3M 2080 series masking tape (temperature resistant to 200°C) instead of the original film (Product Test Report)
4. Precise control of aerodynamic assistance
- Recommended air pressure value: 0.3-0.5MPa (thickness ≤5mm); 0.6-0.8MPa (thickness>5mm)
- Nozzle angle: 15° tilt angle can increase debris removal efficiency by 42%
- Key role: Prevent edge carbonization layer caused by secondary combustion (thickness reduction of 0.05-0.1mm)
5. Engineering practice of thermodynamic isolation
Through three-dimensional thermal imaging analysis, it was found that raising the plate by 2-3mm can reduce the bottom temperature by 58%:
- Support solution: honeycomb plate + ceramic positioning column (thermal conductivity <1W/m·K)
- Isolation effect: effectively avoid focus offset caused by “thermal lens effect”
6. Nano-level precision of optical path calibration
European Optical Association (EOS) standard requirements:
- Check the reflector offset weekly (allowable error ±0.02mm)
- Replace the focusing mirror monthly (accumulated working time ≥120 hours)
- Calibration tool: Use red light locator + micrometer measurement system
7. Chemical optimization of post-processing process
Comparative experiments show that dichloromethane vapor polishing has the best effect:
- Processing time: 30-45 seconds (15 seconds longer for every 1mm increase in thickness)
- Surface roughness: from Ra 3.2μm to Ra 0.4μm
- Safety tips: must be operated in a negative pressure fume hood (OSHA standard 29 CFR 1910.1450)
8. Optical design of reverse engraving
Mirror acrylic back engraving should follow:
- Image preprocessing: mirror flip + 30% grayscale compensation
- Focus adjustment: Z axis raise 0.8 times material thickness
- Energy density: 15-20% lower than front engraving
Conclusion: Improved value chain with technological advancement
Mastering these techniques can increase processing efficiency by more than 35% and control the scrap rate within 2%. It is recommended to regularly participate in the American Laser Institute (LIA) certification training (Course Catalog) and establish a parameter database to continuously optimize the process flow. With the development of intelligent control systems, laser cutting will achieve more accurate AI parameter matching in the future, but core material cognition and process principles are always the cornerstone of technological breakthroughs.