-
Xinqi Development Zone, Leliu, Foshan, Guangdong
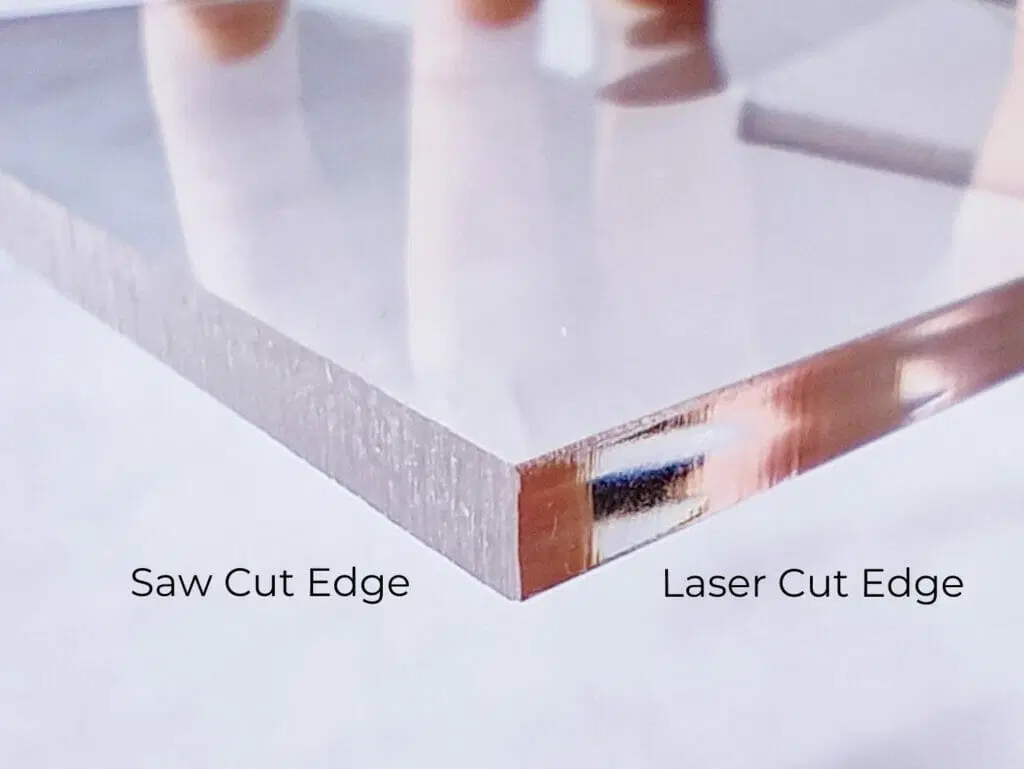
7 Expert Skills of Efficient Acrylic Perspex Sheet Cutting
Table of Contents
Introduction
Acrylic glass has become a star material in the fields of architectural decoration, industrial manufacturing, etc. due to its excellent properties such as 92% light transmittance and impact resistance that is 10 times that of ordinary glass. Its easy processing characteristics allow DIY enthusiasts and professional manufacturers to achieve personalized creation. This article systematically analyzes 7 mainstream cutting technologies and comes with a safe operation guide verified by an authoritative organization to help you accurately master this core process.
Scribing and breaking method: an economical and efficient thin plate solution
▶ Applicable scenarios: transparent/colored plates with a thickness of ≤6mm
▶ Core tools: tungsten steel scribing knife + metal ruler (Swann-Morton professional tools are recommended)
▶ Technical points:
- Double-sided scribing principle: 1/8 depth on both sides to ensure uniform stress distribution
- 45° angle control: keep the tool and the plate at a standard angle (refer to ASTM D5947 test standard)
- Thermal stress relief: use a hot air gun to locally heat the broken section at 60-80℃ (the U.S. Occupational Safety and Health Administration OSHA recommends wearing heat-insulating gloves)
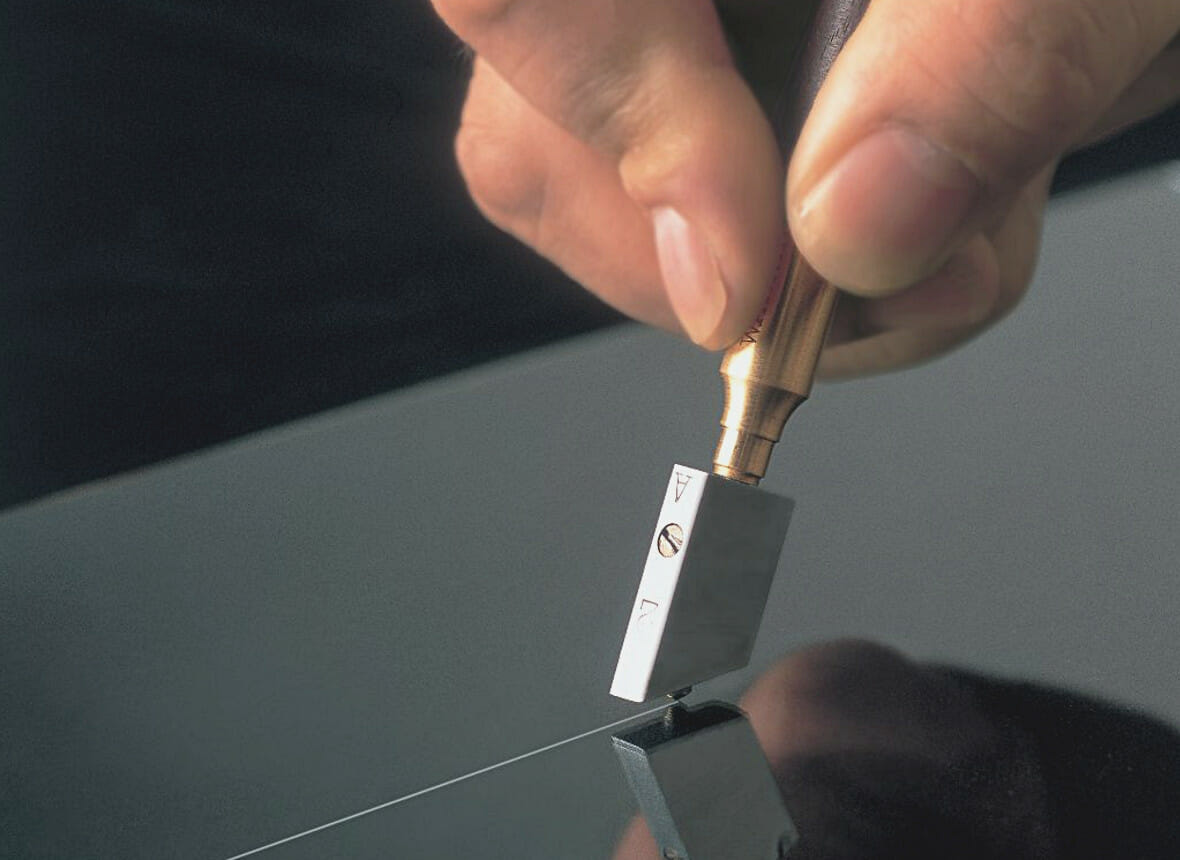
Hand saw cutting method: a modern interpretation of traditional craftsmanship
▶ Tool selection:
- Japanese IRWIN 18TPI fine-toothed hand saw (suitable for plates ≤10mm)
- Swedish Bahco 14TPI variable pitch saw (handling 12-20mm thick plates)
▶ Advanced skills:
- Vibration suppression: double-sided tape + vacuum suction cup for dual fixation (refer to the German Festo pneumatic clamp standard)
- Cutting lubrication: use 3M 08946 professional cutting fluid to reduce the friction coefficient by more than 30%
- Angle correction: pause every 10cm to check the saw path offset and adjust the feed direction in time
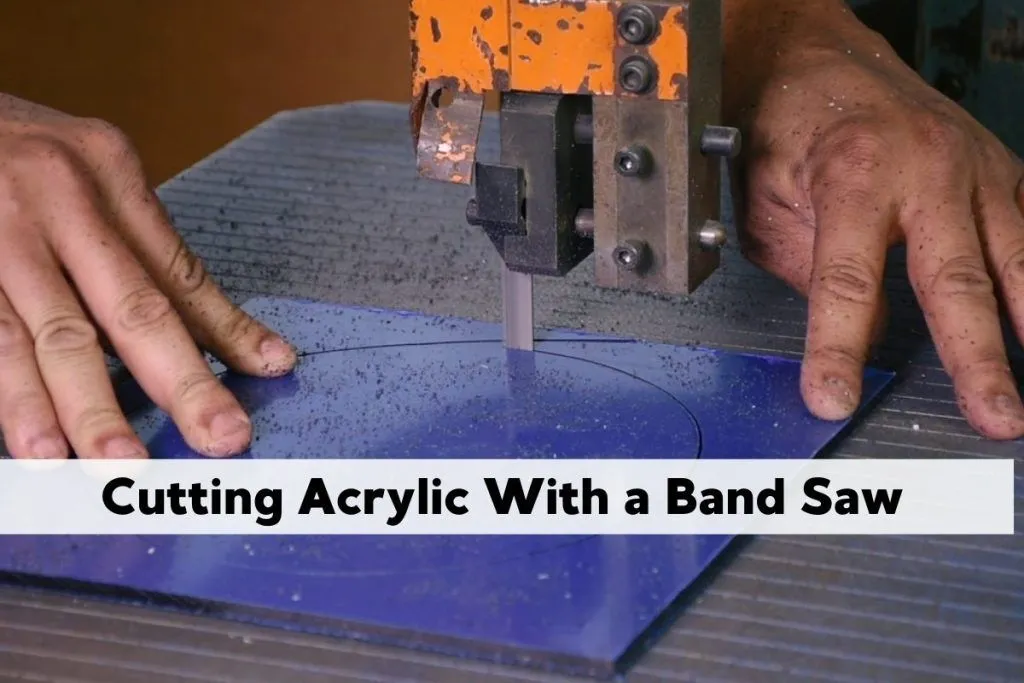
Precision control of curved saws: the path to achieve complex shapes
▶ Equipment configuration:
- Bosch GST 65BE laser-guided curved saw
- Festool T101AO anti-melt edge special saw blade
▶ Key parameters:
- Speed control: 6000-8000rpm (low value for thick plates)
- Feed speed: 15-25cm/min (refer to Makita technical white paper)
- Cooling solution: compressed air + water-soluble coolant combination system (in line with ISO 14000 environmental protection standards)
Band saw system optimization: industrial-grade processing solution
▶ Equipment selection:
- Italian MEP MS-260NC CNC band saw (cutting accuracy ±0.1mm)
- Lenox Diemaster 2 bimetallic saw blade (3TPI coarse tooth/6TPI fine tooth combination)
▶ Process innovation:
- Sawdust management: integrated negative pressure suction system (efficiency increased by 40%)
- Thermal deformation control: PTC ceramic heating plate pre-tightening technology (thermal stress reduced by 65%)
- Cutting monitoring: integrated infrared thermometer to provide real-time feedback on cutting surface temperature (data interface complies with OPC UA standard)
Laser cutting technology: the ultimate solution for precision machining
▶ Equipment parameters:
- TRUMPF TruLaser 5030 fiber laser (power 3000W)
- Auxiliary gas: 99.99% high-purity nitrogen (cutting surface haze value ≤5%)
▶ Process breakthrough:
- Parameter optimization: 0.8mm nozzle + 1.5bar air pressure combination (cutting speed increased by 25%)
- Focus control: dynamic Z-axis adjustment system (cutting width fluctuation ≤ 0.02mm)
- Exhaust gas treatment: four-stage filtration system (meet EPA Tier4 emission standards)
Safety protection system: operating specifications that cannot be ignored
▶ Personal protection:
- 3M 6800 full mask + 60926 gas filter canister combination
- Ansell 37-155 anti-cut gloves (compliant with EN388 standards)
▶ Environmental control:
- Ventilation requirements: ≥15 times/hour air change (refer to ACGIH industrial hygiene standards)
- Electrostatic protection: install Simco IonStorm XC3 ion wind bar
- Waste treatment: classification collection system (RoHS 2.0 certified)
Surface finishing: the transformation from rough to fine products
▶ Polishing process:
- Rough polishing: 320#→600# diamond belt continuous polishing
- Fine polishing: cerium oxide polishing paste + wool wheel combination (surface roughness Ra≤0.01μm)
- Flame polishing: propane/oxygen mixed flame instantaneous treatment (duration ≤0.5 seconds)
▶ Quality inspection:
- Use Mitutoyo surface roughness meter for quantitative analysis
- Pass ASTM D1003 standard transmittance test
FAQ of Acrylic Sheet Cutting
How to reduce edge cracking when cutting with a hand saw?
Choose an 18TPI fine-tooth hand saw (such as Japan IRWIN), lubricate with 3M cutting fluid, and use a vacuum suction cup to fix the plate to reduce vibration.
How to avoid acrylic melting when cutting with a curved saw?
Control the speed at 6000-8000rpm, use water-soluble coolant, and maintain a feed speed of 15-25cm/min (refer to Makita technical parameters).
How high can the accuracy of laser cutting be?
TRUMPF TruLaser 5030 equipment can achieve ±0.02mm accuracy, and the kerf width fluctuation is ≤0.02mm (needs to be matched with 99.99% nitrogen assist).
How to quickly polish and restore transparency after cutting?
First, use 320#→600# abrasive belt for rough polishing, then use cerium oxide polishing paste + wool wheel for fine polishing, or propane flame instantaneous treatment (≤0.5 seconds).
Conclusion
From traditional handicrafts to intelligent laser cutting, acrylic processing technology is undergoing a revolutionary change. When choosing a cutting solution, three factors should be considered comprehensively: material thickness, processing accuracy, and cost-effectiveness. For small and medium-sized processing needs, it is recommended to use the line breaking method combined with mechanical polishing; for mass production, laser cutting equipment equipped with MCT CNC system is preferred.
As an industry leader certified by ISO 9001, Sanyu Acrylic provides a complete product line from 1mm ultra-thin plates to 20mm engineering thick plates, and is equipped with the German TRUMPF laser cutting center to meet various customized needs. Visit www.bestacrylicsheet.com to obtain free samples and technical solutions.