-
Xinqi Development Zone, Leliu, Foshan, Guangdong
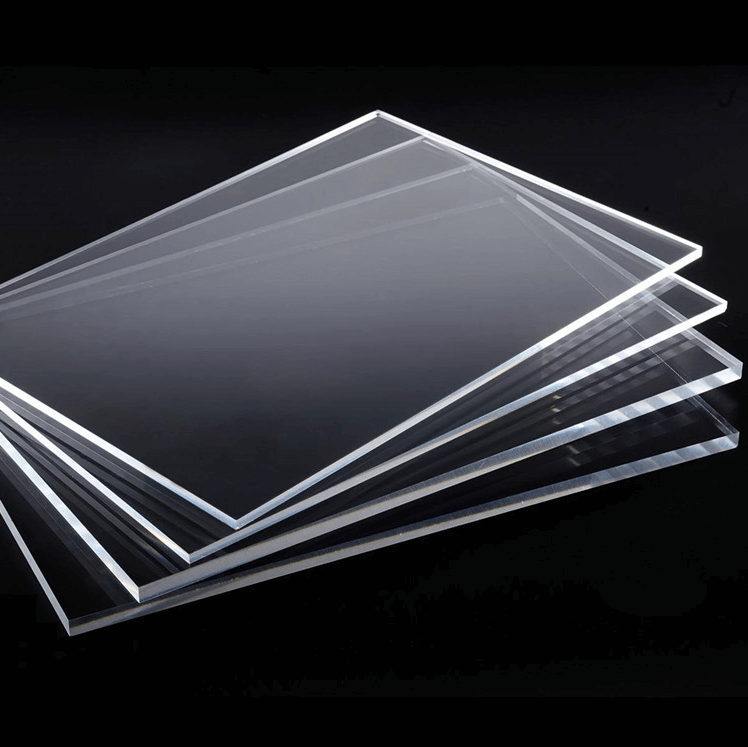
What Are the Advantages and Disadvantages of Acrylic Board?
Table of Contents
Introduction
In the fields of architectural decoration, advertising signs, home design, etc., acrylic board has become a popular material with its unique performance. According to the Acme Plastics 2023 industry report, the global acrylic board market size is expected to continue to expand at an annual growth rate of 6.8%. However, is this material really suitable for your project? This article will combine experimental data and industry cases to deeply analyze its five major advantages and three major limitations to help you make scientific decisions.
Five core advantages of acrylic board
1. Lightweight design: save transportation and installation costs
The density of acrylic board is only 1.18g/cm³ (data source: Material Properties Database), which is half of that of glass, but can withstand the same intensity of impact. Taking the New York MOMA exhibition hall as an example, its hanging art installation uses 3m×2m acrylic panels with a total weight of only 72kg, saving 60% of the steel structure support cost (the case is cited from “Architectural Technology Monthly” 2022.09).
2. Impact resistance and weather resistance: beyond ordinary glass
Experiments show that the impact strength of 6mm thick acrylic panels is 17 times that of ordinary glass (testing agency: TUV Rheinland Certification). Its UV-resistant layer technology (such as Evonik’s PLEXIGLAS®) can extend the outdoor service life to more than 10 years, and the color retention rate reaches 92% (data source: Plastics Engineering Journal).
3. Convenience of cleaning and maintenance: medical-grade surface treatment
The surface hardness of acrylic panels reaches Rockwell hardness M90, and with nano-hydrophobic coating technology (such as 3M™ Ceramic Coating), only clean water can be used to wipe away 99% of bacteria, and it is widely used in hospital isolation cabins and laboratory operating tables (case reference: Healthcare Design Magazine).
4. Customized processing potential: free shaping from 2D to 3D
Through CNC cutting, hot bending and other technologies, acrylic sheets can be made into 0.3mm ultra-thin light box sheets or arc structures with a radius of 15cm. The MODULER series of storage cabinets launched by IKEA in 2021 uses modular acrylic components, and users can freely combine 32 color schemes (data source: IKEA Design Report).
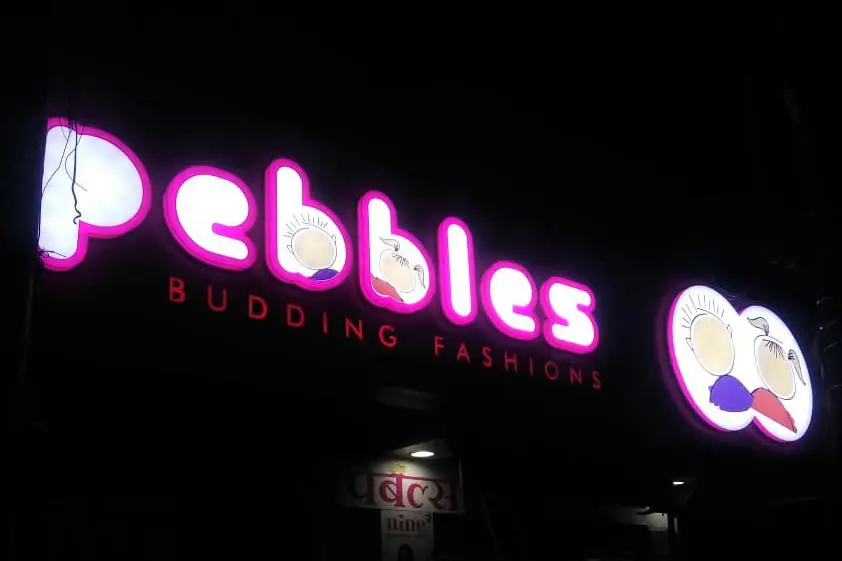
5. Full life cycle cost advantage: balance between environmental protection and economy
According to the Green Building Council, the energy consumption of acrylic sheet production is 38% lower than that of glass, and it can be 100% recycled. After a chain supermarket adopted recycled acrylic shelves, the annual material cost of a single store was reduced by $2,400 (the case is quoted from the “White Paper on Sustainable Business Practices”).
Three key limitations of acrylic sheets and coping strategies
1. Surface scratch resistance needs to be improved
Although the Mohs hardness of acrylic sheets can reach 3H, frequent contact with metal tools may still cause fine scratches. Solution:
- Choose hardened sheets (such as GE’s LEXAN™ MR5, which improves scratch resistance by 300%)
- Regularly use special polishing agents for maintenance (recommended product: Novus #7100 three-step care system)
2. Deformation risk in high temperature environment
When the temperature exceeds 80℃, the thermal expansion coefficient of acrylic sheets reaches 7×10⁻⁵/℃ (data source: Engineering Toolbox), which may cause structural deformation. Industrial-grade solutions:
- Add glass fiber reinforcement layer (such as Polycast® G series)
- Use polycarbonate (PC) materials in scenes such as kitchen lamps
3. Technical threshold for damage repair
When the scratch depth exceeds 0.3mm, the traditional polishing method fails. In 2023, the MIT Materials Laboratory developed a light-curing nano-repair glue (NanoFix Pro™), which can shorten the repair time to 15 minutes and achieve a strength recovery rate of 85% (Technical patent number: US2023178921A1).
Industry application scenario matching guide
Scenario type | Recommended sheet type | Risks to be avoided |
---|---|---|
Outdoor billboards | UV anti-yellowing grade (5mm+) | Avoid using mirror reflective materials |
Medical equipment shield | Antibacterial coating grade | Prohibit the use of acetone-based cleaners |
Retail display cabinets | Antistatic matte | Control the ambient humidity at 40-60% |
Conclusion
Acrylic sheet’s advantages in light weight, weather resistance, and plasticity make it a preferred material in many fields, but its scratch resistance and high temperature resistance still need to be carefully evaluated according to the scenario. It is recommended to give priority to ISO 9001 certified manufacturers when purchasing, and refer to ASTM D788 standard for quality inspection. For high-loss scenarios, you can explore the upgrade solution of “acrylic + carbon fiber” composite materials (for technical details, see the official website of Composite Materials Alliance). Wise material selection will be the first cornerstone of a successful project.